Summary Statement
This OSHA PowerPoint reviews OSHA's inspection policy for enforcing CPL 2-1.36 for hoisting employees on a hoist line to their work stations on communication towers. Although dated, this PowerPoint contains striking images.
- Is capable of identifying existing and predictable hazards in surroundings or in working conditions which are unsanitary, hazardous or dangerous to employees
- Has authorization to take prompt corrective measures
- Has recognized degree, certificate or professional standing, or has extensive knowledge, training and experience
- Has successfully demonstrated ability to solve or resolve problems related to subject matter, the work or project
- Is authorized, designated and deemed competent and qualified by the employer
- Is approved or assigned by the employer to perform a specific duty type(s) or to be at a specific location(s) at the job site
- Anti- two-blocking device:
- Used on all hoists except when an employer can demonstrate that ambient radiation frequency (RF) precludes such use
- In such case, a site-specific safety and health program will be established and maintained onsite to ensure that:
Equipment
- Two-blocking cannot occur
- Effective communications between the hoist operator and personnel being hoisted is maintained
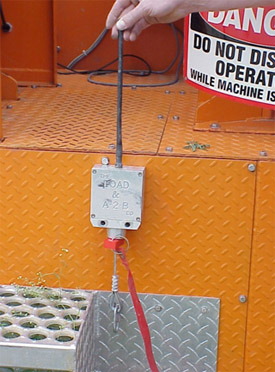 |
- Anti-two-blocking tower mount transmitter
|
- No more than two employees may be hoisted on load line at one time (effective 3/26/02)
- Pre-lift meeting reviews procedures and appropriate requirements in this guideline (CPL 2-1.36)
- Equipment:
- Anti-two-block device used on all hoists
- Rigging, hoist line and slings shall have factor of 10/1
- Hoist line used to raise or lower employees equipped with swivel
- Spin-resistant wire rope prohibited
- When hoisting personnel, the hoist capacity load rating de-rated by a factor of 2 (reduced by half)
- All employees provided with and required to use proper PPE, which inspected before each use
- Guide line used except where employer can demonstrate specific circumstances or conditions to preclude use
- Gin poles thoroughly inspected by competent person before each use to determine they’re free of defects, including but not limited to:
- Damaged and/or missing members
- Corrosive damage
- Missing fasteners
- Broken welds at joints
- General deterioration
- Gin pole attached to tower as designed by RPE, and minimum of two attachment locations at bottom and near top
- Personnel load and material capacities of lifting system in use posted onsite near hoist operator’s location
- All trial lifts, inspections and proof tests documented and documentation left onsite
- Except where demonstrated that its use is precluded, a personnel platform must be used to hoist more than one employee to work station (1926.550(g))
- When a Bostswain’s seat-type or full body harness used to hoist employees, the following applies:
- No more than two employees at a time
- Harness attached to hook by lanyard
- Only locking type snaphooks used
- Harness equipped with two side rings and at least one front and one back D ring
- Hoist line hook equipped with safety latch which can be locked in a closed position
- Use of free-spooling (friction lowering) prohibited
- When hoist line used to raise or lower employee(s), no other load shall be attached to any hoist line
- No other load shall be raised or lowered at same time on same hoist
- As-built drawings approved by RPE provides lifting capacity of gin pole and available at job site
- Gin pole raising line not to be used to raise or lower employees
- Employees must maintain 100% tie off when moving between hoist line and tower
- Maximum rate of travel shall not exceed 200 feet per minute when guide line used to control personnel hoists
- When guide line cannot be used, rate of hoisted employee’s travel shall not exceed 100 feet per minute
- In all personnel hoist situations, maximum rate shall not exceed 50 feet per minute when personnel being lifted approach within 50 feet of top block
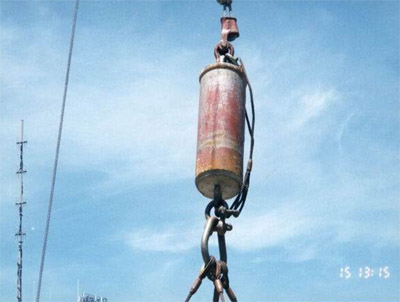 |
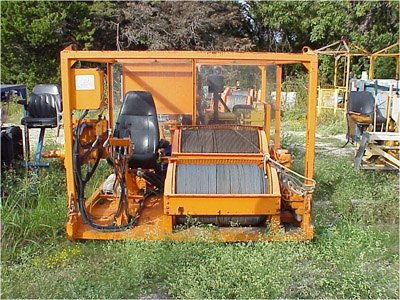 |
Anti-two-block warning system |
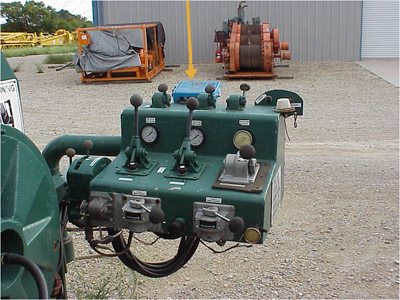 |
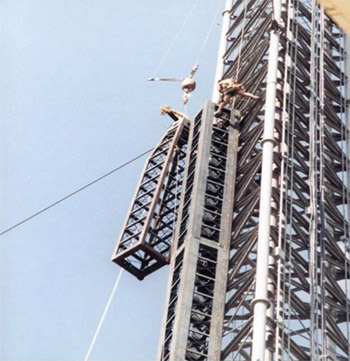 |
Rooster Head |
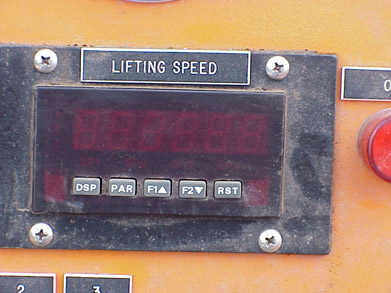 |
Speed control and speed indication are required, especially for personnel rated hoists. |
- Employees being hoisted shall remain in continuous sight of and/or in direct communications with operator or signal person
- When radios used, they shall be non-trunking, closed 2-way selective frequency systems
- When hand signals used, employees must use industry standard hand signals
- Held prior to trial lift at each location
- Meeting shall:
- Be attended by hoist operator, employees to be lifted and crew chief
- Review procedures to be followed and all appropriate requirements
- Be repeated for any employee newly assigned
- All trial lifts, inspections and proof tests documented, with documentation remaining onsite during length of project
- Pre-lift meeting documented, with documentation remaining onsite during length of project
… Fall protection during climbing is necessary part of fall safety. However, climbers sometimes faced with climbing in areas with inadequate anchorage points (typically during antenna climbing). In these cases, first man up carries and attaches safety rope for use during time of work performance. Fall protection rope removed when all work completed.
… Though free climbing not authorized, antenna manufacturers do not presently have way to provide fall protection that meets minimum anchorage requirements.
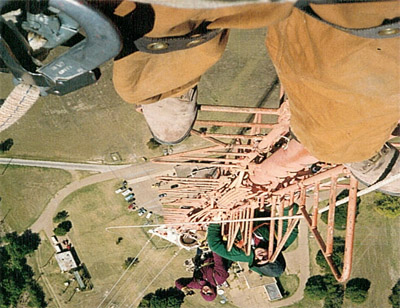 |
First man up attaches safety line. Once attached, all others can attach to it. Depending upon the number of personnel on the antenna, more than one rope may be required. |
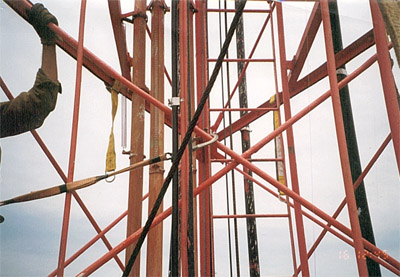 |
The use of portable type anchorage points can make difficult attachment locations safe. Cross arms shown here are one such means. |
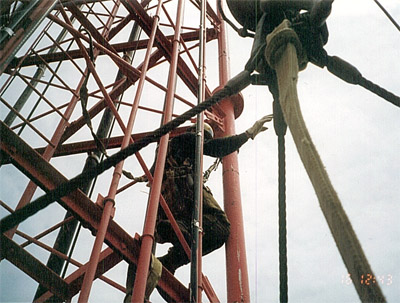 |
Climber is attached with fall protection lanyard and positioning device. |
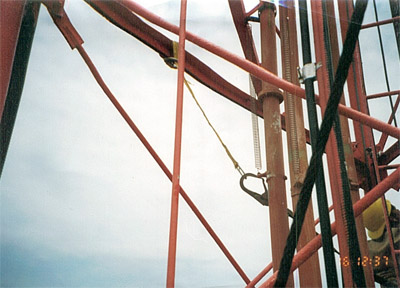 |
Climber is using a cross arm anchorage point to allow him to work in an area that does not have an adequate anchorage point. |
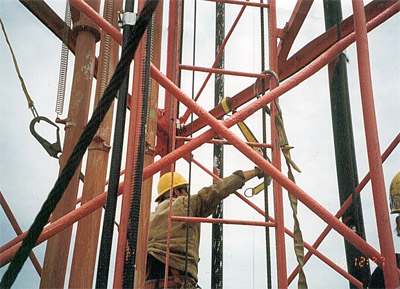 |
Climber is transferring from one anchorage point to another. |
- The following NOT in place and NOT currently a rule:
- “Qualified climber” is term used in tower industry and by National Association of Tower Erectors (NATE)
- Though term used, still not an accepted principle by OSHA
- “Federal Register”
- Vol. 55, No. 69
- April 10, 1990
- 1910 Walking and Working Surfaces and Personal Protective Equipment (Fall Protection Systems)
- Indeed, OSHA believes that the amount of time employees would spend installing, inspecting and maintaining fall protection on fixed ladders could substantially exceed the amount of time that ‘qualified climbers’ would be spending to climb the ladders.
- Therefore, as an alternative, OSHA believes it appropriate to allow “qualified climbers” as defined by OSHA to climb these ladders without fall protection under certain conditions.
- First, the employer would have to certify that the employee is a “qualified climber,” as provided in 1910.32(b)(5) of this proposal.
- Second, once the “qualified climber” reaches a work station, the employer would be required to provide appropriate fall protection.
- “Qualified climbers” as provided in 1910.23(a)(2), ladders and step bolts on triangulation, telecommunication electrical power towers and poles and similar structures, including stacks and chimneys, need not have ladder safety devices, cages or wells if only “qualified climbers” are permitted to use these ladders or step bolts. Such “qualified climbers” shall meet the following requirements.
- (i) “Qualified climbers” shall be physically capable (demonstrated through observations of actual climbing activities or by a physical examination) of performing the duties which may be assigned them.
- (ii) “Qualified climbers” shall have successfully completed a training or apprenticeship program that covered hands-on training for the safe climbing of ladders or step bolts and shall be retrained as necessary to ensure the necessary skills are maintained.
- (iii) The employer shall ensure through performance observations, and formal classroom or on the job training, that the “qualified climber” has the skill to safely perform the climbing.
- (iv) “Qualified climbers” shall have climbing duties as one of their routine work activities and
- (v) “Qualified climbers,” when reaching their work position, shall be protected by a fall protection system meeting the requirements of 1910.28.
- 1910.268 Telecommunications
- (g) Personal climbing equipment – (1) General body belts and pole straps shall be provided and the employer shall ensure their use when work is performed at positions more than four feet (1.2m) above the ground, on poles and on towers, except as provided in paragraphs (n)(7) and (n)(8) of this section.
- … Personal fall protection systems shall meet the applicable requirements set forth in Subpart I of this part. The employer shall ensure that all climbing equipment is inspected prior to each day’s use to determine that it is in safe working condition.
- … Production samples of personal fall protection systems shall be certified by the manufacturer or a qualified person as having been tested in accordance with and as meeting the requirements of Subpart I of this part as applicable.
- Currently no program for “qualified climbers”
- However, if company set up for a “qualified climber” program, the proposed rules would be a minimum starting point for establishing safe climber’s program
- Absolute best method for maintaining climber safety is 100% fall protection
- Accidents from falls do not have to be from towers
- Can happen from any height, so think about what you are doing