Summary Statement
Discusses OSHA’s lockout/tagout standard, including when it applies, how to craft a written program, equipment you would need and steps that must be taken.
Recently, an employee was cleaning the unguarded side of an operating saw. The employee was caught in the moving parts of the saw and pulled into a nip point between the saw blade and the idler wheel, resulting in fatal injuries. This accident was caused by the failure to shut down or turn off the equipment to perform maintenance. If the employee utilized a lockout/tagout procedure, he would still be alive today.
The Control of Hazardous Energy Source Standard (29 CFR l9lO.l47), which is more commonly known as the Lockout/Tagout Standard, is a Federal Occupational Safety and Health Administration (OSHA) program, It is designed to prevent the unexpected startup, or energizing, of machinery and equipment during service and maintenance operations which could cause injury to employees. It is also designed to prevent the release of stored energy which could cause injury to employees. Industry has been obligated to comply with the Lockout/Tagout Standard since January 3,l990.
-
The lockout standard
applies if:
- The employee is required to remove or bypass a guard or other safety device during service and maintenance.
- An associated danger zone exists during a machine operating cycle.
- The employee is required to place any body part into an area of the machinery or equipment where work is actually being performed upon the material being processed.
Minor tool changes, adjustments, and other minor service activities, which take place during normal production, are not included in the Lockout/Tagout Standard provided they are 1) routine, repetitive, and integral to the use of the equipment, and 2) that they are performed using alternative measures which provide effective protection for the employee.
Energy Sources
Most people immediately think of electricity as a potentially hazardous energy source. There are other sources of energy, though, that can be just as hazardous. These energy sources include thermal, chemical, pneumatic, hydraulic, mechanical, and gravity, It is important to remember that all sources of energy that have the potential to unexpectedly startup, energize, or release must be identified and locked, blocked, or released before servicing or maintenance is performed.
Written Lockout/Tagout
Program
-
The written program
must have:
- A specific statement as to the intended use of the program.
- Specific steps for shutting down, isolating, and blocking machinery and equipment in order to control hazardous energy.
- Specific procedures for the placement and removal of lockout/tagout devices as well as the method of identifying an individual's locks or tags.
- Requirements for verifying the effectiveness of the lockout/ tagout device by testing procedures for machinery and equipment.
- A detailed training program for employees who perform the service and maintenance and for employees who are indirectly affected by those operations.
- Descriptions of company lockout/tagout policies regarding multiple lockout/tagouts, outside personnel, shift changes, and training of employees.
Equipment
An audit should be conducted on all machines and equipment to identify all potentially dangerous energy sources and all energy isolating devices. By doing this,employers will be able to establish all appropriate lockout/tagout procedures.
Employee Classifications
Two types of personnel are directly affected by the Lockout/ Tagout Standard: Affected Employees and Authorized Employees. OSHA defines an Affected Employee as an employee whose job requires him/her to operate or use machinery or equipment on which servicing or maintenance is being performed under a lockout/tagout procedure or whose job requires him/her to work in an area in which servicing or maintenance is being performed under a lockout/tagout procedure. OSHA defines an Authorized Employee as an employee who implements a lockout/tagout procedure on machinery or equipment in order that servicing or maintenance may be performed. Often, an authorized employee and an affected employee may be the same person.
Steps in
a Typical Lockout/Tagout Procedure
-
Phase I - Locks,
Blocks or Releases Energy:
- The authorized employee notifies all affected employees that a lockout/tagout procedure is ready to begin.
- The machinery or equipment is de-energized.
- The authorized employee releases or restrains all stored energy.
- All locks and tags are checked for defects. If any are found, the lock or tag is discarded and replaced.
- The authorized employee places a personalized lock or tag on the energy isolating device.
- The authorized employee tries stating the machinery or equipment to ensure that it has been isolated from its energy source. The machine is then de-energized again after this test.
- The machinery or equipment is now ready for service or maintenance.
-
Phase 2 - Returns
the Machinery or Equipment to Production:
- The authorized employee checks the machinery or equipment to be certain no tools have been left behind.
- All safety guards are checked to be certain that they have been replaced properly.
- All affected employees are notified that the machinery or equipment is about to go back into production.
- The authorized employee performs a secondary check of the area to ensure that no one is exposed to danger.
- The authorized employee removes the locks and/or tags from the energy isolating device and restores energy to the machinery or equipment.
This basic example of the lockout/tagout procedure is used when only one person is performing service or maintenance on machinery or equipment and when no testing or positioning of the equipment is required.
Multiple Lockout
In a multiple lockout/tagout procedure, each person working on the machinery or equipment must place a lock or tag on the energy isolating device. If the energy isolating device will not accept multiple locks or tags, a hasp (a multiple lockout device) may be used. The locks or tags must be placed in such a way that energy cannot be restored to the machinery or equipment until every lock or tag is removed, As each employee involved no longer needs to maintain his/her lockout/tagout protection, that employee removes his/her lock or tag. The employee attaching the lock or tag is the only person authorized to remove the lock or tag.
Testing And Positioning
Before a machine can be placed in service the positioning of pats is sometimes required.-
The following procedure
should be followed when testing or positioning machinery or equipment
during service and maintenance:
- The authorized employee makes certain that the work area is clear of tools and materials.
- The authorized employee notifies all affected employees that the machinery or equipment will be positioned or tested.
- All employees leave the area
- Locks or tags are removed.
- The machine is started and tested or positioned.
- When testing or positioning is complete, the machinery or equipment is de-energized following the proper lockout/tagout procedure for servicing or the machine is returned to production via the appropriate procedure.
Exemptions to Lockout / Tagout Standards
This standard covers the servicing and maintenance of machines and equipment where the unexpected energizing,startup, or release of energy could cause injury to employees. The standard establishes minimum performance requirements for the control of such hazardous energy,and applies to the control of energy during normal servicing /and or maintenance of machines and equipment However, this standard does not apply to construction,agriculture and maritime employment; installation under the exclusive control of electrical utilities; exposure to electrical hazards from work on, near, or with conductors or equipment in electrical utilization installation; and oil and gas well drilling and servicing. Although there are exemptions to these standards this may not eliminate your personal liability. If you have questions concerning liability obtain legal advice.Inspections And Training
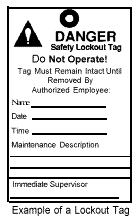
-
All employees
working in an area requiring lockout/tagout procedures must be trained.
Training must include:
- The recognition of lockout/tagout devices and the importance of not disturbing or removing them unless authorized.
- The safe application, use, and removal of energy controls,
- The limitations of tags in a lockout/tagout procedure.
Training must occur whenever there is a change in job assignment, a change in machinery or equipment, an energy control procedure change, or a change in a process that presents a new hazard. Retraining is to be conducted whenever the employer believes that employees' knowledge of energy control procedures is inadequate and as part of the annual inspection.
Outside Personnel
When outside personnel, such as contractors, arc on site and engaged in activities that require compliance with the Lockout/Tagout Standard, the on-site employer and the outside employer must inform one another of their lockout/tagout procedures. It is the responsibility of the on-site employer to ensure that his/her employees understand and comply with the methods of the other's lockout/tagout procedures.
Shift Changes
A high percentage of accidents historically occur shortly after a shift change and are often due to a lack of communication. During a shift change, exiting personnel should meet oncoming personnel at the lockout/tagout device. The oncoming authorized employee should place his/her lock or tag on the energy isolating device before the exiting authorized employee removes his /her lock or tag. If this is not possible, the oncoming authorized employee should place his/her lock or tag on the energy isolating device immediately after the exiting authorized employee removes his/her lock or tag. Exiting employees should inform oncoming employees of any problems or concerns regarding the service and maintenance of machinery or equipment.
Lockout/Tagout Checklist
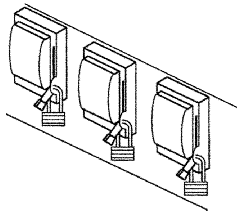
-
The checklist below
has been developed to assist in complying with the Lockout/Tagout Standard:
- Audit all machinery and equipment for types and magnitudes of energy and potential hazards,
- identify and document all machinery and equipment for which a lockout/tagout procedure must be developed.
- Identify and document, by name and by job title, all affected employees.
- Identify and document, by name and by job title, all employees authorized to perform lockout/tagout procedures.
- Describe and document types and locations of energy isolating devices for all machinery and equipment identified in Step 2.
- Describe and document the types of energy involved and the methods to be used to dissipate or restrain the energy for all machinery and equipment identified in Step 2.
- Describe and document the method established to isolate the energy (lock or tag) and any additional safety measures to be taken.
- Develop a written Lockout/Tagout Program.
Summary
The Control of Hazardous Energy Source Standard requires employers to isolate machinery and equipment from its energy sources and to lock or tag them before service or maintenance is performed The standard also requires that all employees be trained in the company's lockout/tagout policies and procedures.