Summary Statement
Excavation and trenching are among the most hazardous
construction operations. The Occupational Safety and Health
Administration’s (OSHA) Excavation standards, 29 Code
of Federal Regulations (CFR) Part 1926, Subpart P, contain
requirements for excavation and trenching operations. This
booklet highlights key elements of the standards and describes safe work practices that can protect workers from cave-ins and other hazards.
2015
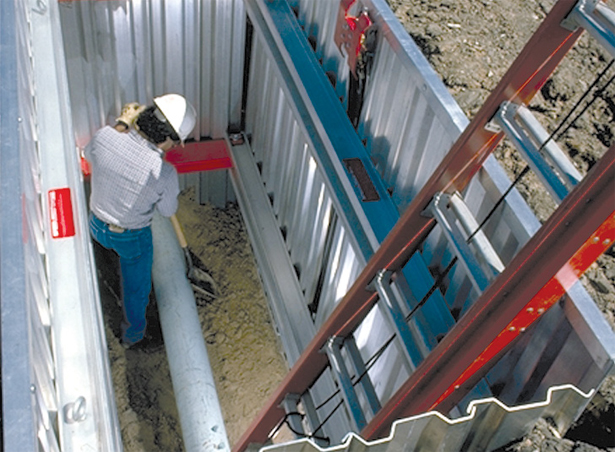
Photo courtesy of Speed Shore Corp.
Table of Contents
- Introduction
- Preplanning
- Protective Systems
- How can employers prevent cave-ins?
- What types of protective systems can employers use to protect workers from cave-ins?
- What other precautions do employers need to take to protect workers from cave-ins?
- What are the requirements for safely installing and removing protective systems?
- What do employers need to do to maintain materials and equipment used for protective systems?
- Additional Hazards and Protections
- What other excavation hazards do employers need to address?
- What is the effect of water accumulation on excavation safety and what do employers need to do to protect workers from water-related excavation hazards?
- How can employers protect workers from hazardous atmospheres inside excavations?
- What means of access and egress must employers provide?
- What protective equipment are employers required to provide to workers in pier holes and confined footing excavations?
- When must employers conduct site inspections?
- Conclusion
- Workers’ Rights
- OSHA Assistance, Services and Programs
- NIOSH Health Hazard Evaluation Program
- OSHA Regional Offices
- How to Contact OSHA
Introduction
Excavation and trenching are among the most hazardous construction operations. The Occupational Safety and Health Administration’s (OSHA) Excavation standards, 29 Code of Federal Regulations (CFR) Part 1926, Subpart P, contain requirements for excavation and trenching operations. This booklet highlights key elements of the standards and describes safe work practices that can protect workers from cave-ins and other hazards.
What is the difference between an excavation and a trench?
OSHA defines an excavation as any man-made cut, cavity, trench, or depression in the Earth’s surface formed by earth removal. A trench is defined as a narrow excavation (in relation to its length) made below the surface of the ground. In general, the depth of a trench is greater than its width, but the width of a trench (measured at the bottom) is not greater than 15 feet (4.6 m).
What are the dangers of trenching and excavation operations?
Trenching and excavation work presents serious hazards to all workers involved. Cave-ins pose the greatest risk and are more likely than some other excavation-related incidents to result in worker fatalities. One cubic yard of soil can weigh as much as a car. An unprotected trench can be an early grave. Employers must ensure that workers enter trenches only after adequate protections are in place to address cave-in hazards. Other potential hazards associated with trenching work include falling loads, hazardous atmospheres, and hazards from mobile equipment.
What do the OSHA Excavation standards cover, and how do they protect workers?
The standards apply to all open excavations made in the Earth’s surface, including trenches. Following the requirements of the standards will prevent or greatly reduce the risk of cave-ins and other excavation-related incidents.
What are the soil classification categories?
Some of the compliance methods permitted under the Excavation standards require a competent person to classify soil and rock deposits as:
- Stable rock;
- Type A soil;
- Type B soil; or
- Type C soil.
See Appendix A to Subpart P of Part 1926 – Soil Classification.
Stable Rock – Natural solid mineral matter that can be excavated with vertical sides and remain intact while exposed.
Type A – Cohesive soils with an unconfined compressive strength of 1.5 tons per square foot (tsf) (144 kPa) or greater. Examples include: clay, silty clay, sandy clay, and clay loam. Certain conditions preclude soil from being classified as Type A. For example, no soil is Type A if it is fissured or has been previously disturbed. See Appendix A to Subpart P of Part 1926, paragraph (b) – Definitions (Type A), for a detailed definition of Type A soil.
Type B – Includes cohesive soil with an unconfined compressive strength greater than 0.5 tsf (48 kPa) but less than 1.5 tsf (144 kPa) and granular cohesionless soils (such as angular gravel, similar to crushed rock, silt, silt loam, sandy loam, and, in some cases, silty clay loam and sandy clay loam). See Appendix A to Subpart P of Part 1926, paragraph (b) — Definitions (Type B), for a detailed definition of Type B soil.
Type C – Cohesive soil with an unconfined compressive strength of 0.5 tsf (48 kPa) or less, granular soils (including gravel, sand, and loamy sand), submerged soil or soil from which water is freely seeping, submerged rock that is not stable, or material in a sloped, layered system where the layers dip into the excavation or with a slope of four horizontal to one vertical (4H:1V) or steeper. See Appendix A to Subpart P of Part 1926, paragraph (b) — Definitions (Type C), for a detailed definition of Type C soil.
Note: Unconfined compressive strength means the load per unit area at which a soil will fail in compression. It can be determined by laboratory testing or estimated in the field using a pocket penetrometer, thumb penetration tests, or other methods.
See the video link below for additional guidance on classifying soil: www.osha.gov/dts/vtools/construction/ soil_testing_fnl_eng_web.html.
A competent person is an individual, designated by the employer, who is capable of identifying existing and predictable hazards in the surroundings or working conditions which are unsanitary, hazardous or dangerous to workers, and who is authorized to take prompt corrective measures to eliminate them.
Under the Excavation standards, tasks performed by the competent person include:
- Classifying soil;
- Inspecting protective systems;
- Designing structural ramps;
- Monitoring water removal equipment; and
- Conducting site inspections.
Preplanning
Why is preplanning important to excavation work?
No matter how many trenching, shoring, and backfilling jobs an employer has done in the past, it is important to approach each new job with care and preparation. Many on-the-job incidents result from inadequate initial planning. Waiting until after the work starts to correct mistakes in shoring or sloping slows down the operation, adds to the cost of the project, and makes a cave-in or other excavation failure more likely.
What safety factors should be considered when bidding on a job?
Before preparing a bid, employers should know as much as possible about the jobsite and the materials they will need to have on hand to perform the work safely and in compliance with OSHA standards. A safety checklist may prove helpful when employers are considering new projects. Factors to consider may include:
- Traffic
- Proximity and physical condition of nearby structures
- Soil classification
- Surface and ground water
- Location of the water table
- Overhead and underground utilities
- Weather
- Quantity of shoring or protective systems that may be required
- Fall protection needs
- Number of ladders that may be needed
- Other equipment needs.
Employers can gather the information they need through jobsite studies, observations, test borings for soil type or conditions, and consultations with local officials and utility companies. This information will help employers determine the amount, kind, and cost of safety equipment they will need to perform the work safely.
How can employers avoid hitting underground utility lines and pipes during excavation work?
Before starting work, the Excavation standards require employers to do the following:
- Determine the approximate location(s) of utility installations — including sewer, telephone, fuel, electric, and water lines. One common industry practice is to call 811, the “Call Before You Dig” number, to establish the location of any underground utility installations in the work area.
- Contact and notify the utility companies or owners involved to inform them of the proposed work within established or customary local response times.
- Ask the utility companies or owners to establish the location of underground installations prior to the start of excavation work. If they cannot respond within 24 hours (unless the period required by state or local law is longer) or cannot establish the exact location of the utility installations, employers may proceed with caution, which includes using detection equipment or other acceptable means to locate utility installations.
- Determine the exact location of underground installations by safe and acceptable means when excavation operations approach the approximate location of the installations.
- Ensure that while the excavation is open, underground installations are protected, supported or removed as necessary to safeguard workers.
Protective Systems
How can employers prevent cave-ins?
OSHA generally requires that employers protect workers from cave-ins by:
- Sloping and benching the sides of the excavation;
- Supporting the sides of the excavation; or
- Placing a shield between the side of the excavation and the work area.
What types of protective systems can employers use to protect workers from cave-ins?
In many cases the type of protective system needed is well known and simple to use. At other times employers will undertake the more complex process of designing a protective system. Designing a protective system requires consideration of many factors, including: soil classification, depth of cut, water content of soil, weather and climate, and other operations in the vicinity. Employers are free to choose the most practical design that will provide the necessary protections. Any system used must meet the required performance criteria.
The Excavation standards describe various methods and approaches that can be used to design protective systems. Examples of protective systems that can be used to comply with the Excavation standards include:
- Sloping the sides of the excavation to an angle not steeper than 1½:1 (for every foot of depth, the trench must be excavated back 1½ feet). A slope of this gradation is safe for any type of soil.
- Designing a sloping and benching system in accord with tabulated data, such as tables and charts, approved by a registered professional engineer. This data must be in writing and must include enough explanatory information (including the criteria for selecting a system and the limits on the use of the data) for the user to be able to select an appropriate protective system. At least one copy of the data, which identifies the registered professional engineer who approved it, must be kept at the worksite during construction of the protective system. After the system is completed, the data may be stored away from the jobsite, but a copy must be provided upon request to an OSHA compliance officer.
- Using a trench box or shield approved by a registered professional engineer or designed in accord with tabulated data approved by a registered professional engineer.
The Excavation standards do not require a protective system when an excavation is made entirely in stable rock or when an excavation is less than 5 feet (1.52 meters) deep and a competent person has examined the ground and found no indication of a potential cave-in.
What other precautions do employers need to take to protect workers from cave-ins?
The Excavation standards require employers to provide support systems, such as shoring, bracing, or underpinning, when necessary to ensure that adjacent structures (including adjoining buildings, walls, sidewalks and pavements) remain stable for the protection of workers. The standards also prohibit excavation below the base or footing of any foundation or retaining wall that could be reasonably expected to pose a hazard to workers unless:
- The employer provides a support system, such as underpinning;
- The excavation is in stable rock; or
- A registered professional engineer determines that the structure is far enough away from the excavation that it would not be affected by the excavation activity or that the excavation work will not pose a hazard to workers.
Excavations that would undermine sidewalks, pavement, and appurtenant structures are prohibited unless the employer provides an appropriately designed support system or another effective method of protecting workers from the possible collapse of those structures.
What are the requirements for safely installing and removing protective systems?
The Excavation standards require employers to take certain steps to protect workers when installing and removing support systems. For example:
- Members of support systems must be securely connected to prevent sliding, falling, kickouts or predictable failure.
- Support systems must be installed and removed in a manner that protects workers from cave-ins and structural collapses and from being struck by members of the support system.
- Members of support systems must not be overloaded.
- Before temporary removal of individual members, additional precautions are required, such as installing other structural members to carry loads imposed on the support system.
- Removal must begin at, and progress from, the bottom of the excavation.
- Backfilling must progress together with the removal of support systems from excavations.
In addition, the standards permit excavation of 2 feet (0.61 meters) or less below the bottom of the members of a support system, but only if the system is designed to resist the forces calculated for the full depth of the trench and there are no indications, while the trench is open, of a possible loss of soil from behind or below the bottom of the support system. Employers must coordinate the installation of support systems with the excavation work.
What do employers need to do to maintain materials and equipment used for protective systems?
Employers are responsible for maintaining materials and equipment used for protective systems. Defective and damaged materials and equipment can cause protective systems to fail and lead to other excavation hazards. Employers must ensure that:
- Materials and equipment are free from damage or defects that might impair their proper function;
- Manufactured materials and equipment are used and maintained consistent with the manufacturer’s recommendations and are used so as to prevent worker exposure to hazards;
- A competent person examines any damaged materials or equipment to evaluate its suitability for continued use; and
- If a competent person cannot assure that damaged material or equipment can support the intended loads or is otherwise suitable for use, the materials and equipment are removed from service until evaluated and approved by a registered professional engineer.
Additional Hazards and Protections
What other excavation hazards do employers need to address?
In addition to cave-ins and related hazards, workers involved in excavation work are exposed to hazards involving falling loads and mobile equipment. To protect workers from these hazards, OSHA requires employers to take certain precautions. For example, employers must:
- Protect workers from excavated or other materials or equipment that could pose a hazard by falling or rolling inside the excavation by placing and keeping such materials or equipment at least 2 feet (0.61 meters) from the edge and/or by using a retaining device to keep the materials or equipment from falling or rolling into the excavation.
- Provide a warning system (such as barricades, hand or mechanical signals, or stop logs) when mobile equipment is operated adjacent to an excavation, or when such equipment must approach the edge of an excavation, and the operator does not have a clear and direct view of the edge.
- Protect workers from loose rock or soil that could fall or roll from an excavation face by scaling to remove loose material, installing protective barricades at appropriate intervals, or using other equivalent forms of protection.
- Institute and enforce work rules prohibiting workers from working on faces of sloped or benched excavations at levels above other workers unless the workers at the lower levels are adequately protected from the hazards of falling, rolling, or sliding material or equipment.
- Institute and enforce work rules prohibiting workers from standing or working under loads being handled by lifting or digging equipment.
- Require workers to stand away from vehicles being loaded or unloaded to protect them from being struck by any spillage or falling materials. (Operators may remain inside the cab of a vehicle being loaded or unloaded if the vehicle is equipped, in accord with 29 CFR 1926.601(b)(6), to provide adequate protection for the operator.)
What is the effect of water accumulation on excavation safety and what do employers need to do to protect workers from water-related excavation hazards?
Water in an excavation can undermine the sides of the excavation and make it more difficult for workers to get out of the excavation. The OSHA standards prohibit employers from allowing workers to enter an excavation where water has accumulated or is accumulating unless adequate precautions are taken to protect workers. Such precautions can include special support or shield systems to prevent cave-ins, water removal to control the water level, or the use of a safety harness and lifeline. If an employer uses water removal equipment to control or prevent water accumulation, the equipment and operations must be monitored by a competent person to ensure proper use. If excavation work interrupts the natural drainage of surface water, the OSHA standards also require the use of diversion ditches, dikes, or other suitable means to prevent surface water from entering the excavation and to provide adequate drainage of the adjacent area. In addition, a competent person must inspect excavations subject to runoffs from heavy rains, and excavations subject to such runoffs are subject to the requirements described previously in this paragraph.
How can employers protect workers from hazardous atmospheres inside excavations?
Atmospheric testing is required before workers enter an excavation greater than 4 feet (1.22 meters) in depth where an oxygen deficiency or a hazardous atmosphere is present or could reasonably be expected, such as in excavations in landfill areas or excavations in areas where hazardous substances are stored nearby. If there are any hazardous conditions present, the employer must ensure that adequate precautions are taken to prevent employee exposure to those conditions. Such precautions include providing workers with proper respiratory protection or ventilation. In addition, when controls are used to reduce the level of atmospheric contaminants to acceptable levels, testing must be conducted as often as necessary to ensure that the atmosphere remains safe.
If hazardous atmospheric conditions exist or may reasonably be expected to develop in an excavation, the employer must ensure the ready availability of emergency rescue equipment, such as breathing apparatus, a safety harness and line, or a basket stretcher. This equipment must be attended when in use.
Note: In addition to the Excavation standards’ provisions on hazardous atmospheres in excavations, OSHA’s Confined Spaces in Construction standard (29 CFR Part 1926, Subpart AA) applies to non-excavation work within a confined space located in an excavation. These standards are intended to complement each other and address two distinct hazards: hazardous atmospheres in excavations and the additional hazards associated with confined spaces located within excavations. For example, the Confined Spaces in Construction standard covers entry into a prefabricated storm drain, other pipe, or manhole even if located at the bottom of an open excavation.
What means of access and egress must employers provide?
OSHA requires employers to provide ladders, steps, ramps, or other safe means of egress for workers working in trench excavations 4 feet (1.22 meters) or deeper. The means of egress must be located so as not to require workers to travel more than 25 feet (7.62 meters) laterally within the trench.
Any structural ramps used solely for worker access or egress must be designed by a competent person. Structural ramps used for access or egress of equipment must be designed by a competent person qualified in structural design. Also, structural members used for ramps or runways must be uniform in thickness and joined in a manner to prevent tripping or displacement.
What protective equipment are employers required to provide to workers in pier holes and confined footing excavations?
Employers must ensure that any worker who enters a bellbottom pier hole or similar deep and confined footing excavation wears a harness with a lifeline. The lifeline must be attached securely to the harness and must be separate from any line used to handle materials. Also, the lifeline must be individually attended by an observer at all times when the worker wearing the lifeline is in the excavation.
When must employers conduct site inspections?
Employers must ensure that a competent person inspects all excavations, adjacent areas, and protective systems daily for possible cave-ins, indications of failures in protective systems and equipment, hazardous atmospheres, and other hazardous conditions. Inspections must be done prior to the start of work and as needed throughout the shift. Inspections are also required after natural events, such as rainstorms, or other hazard-increasing occurrences, such as blasting work. If an inspector finds any unsafe conditions during an inspection, the employer must clear workers from the hazardous area until the necessary safety precautions have been taken.
Conclusion
When employers share the details of their safety and health programs with workers, they should emphasize the critical role workers play in keeping the jobsite safe. Employers also need to emphasize specific practices that will help reduce the risk of on-the-job injuries at excavation sites. Such practices can include the following:
- Know where underground utilities are located before digging.
- Keep excavated soil (spoils) and other materials at least 2 feet (0.61 meters) from trench edges.
- Keep heavy equipment away from trench edges.
- Identify any equipment or activities that could affect trench stability.
- Test for atmospheric hazards such as low oxygen, hazardous fumes, and toxic gases when workers are more than 4 feet deep.
- Inspect trenches at the start of each shift.
- Inspect trenches following a rainstorm or other water intrusion.
- Inspect trenches after any occurrence that could have changed conditions in the trench.
- Do not work under suspended or raised loads and materials.
- Ensure that personnel wear high-visibility or other suitable clothing when exposed to vehicular traffic.
Employers should consider establishing and maintaining safety and health management systems that provide systematic policies, procedures, and practices for protecting workers from job-related safety and health hazards. See www.osha.gov/ Publications/safety-health-management-systems.pdf.
Workers’ Rights
Workers have the right to:
- Working conditions that do not pose a risk of serious harm.
- Receive information and training (in a language and vocabulary the worker understands) about workplace hazards, methods to prevent them, and the OSHA standards that apply to their workplace.
- Review records of work-related injuries and illnesses.
- File a complaint asking OSHA to inspect their workplace if they believe there is a serious hazard or that their employer is not following OSHA’s rules. OSHA will keep all identities confidential.
- Exercise their rights under the law without retaliation, including reporting an injury or raising health and safety concerns with their employer or OSHA. If a worker has been retaliated against for using their rights, they must file a complaint with OSHA as soon as possible, but no later than 30 days.
For more information, see OSHA’s Workers page.
OSHA Assistance, Services and Programs
OSHA has a great deal of information to assist employers in complying with their responsibilities under OSHA law. Several OSHA programs and services can help employers identify and correct job hazards, as well as improve their injury and illness prevention program.
Establishing an Injury and Illness Prevention Program
The key to a safe and healthful work environment is a comprehensive injury and illness prevention program.
Injury and illness prevention programs are systems that can substantially reduce the number and severity of workplace injuries and illnesses, while reducing costs to employers. Thousands of employers across the United States already manage safety using injury and illness prevention programs, and OSHA believes that all employers can and should do the same. Thirty-four states have requirements or voluntary guidelines for workplace injury and illness prevention programs. Most successful injury and illness prevention programs are based on a common set of key elements. These include management leadership, worker participation, hazard identification, hazard prevention and control, education and training, and program evaluation and improvement. Visit OSHA’s Injury and Illness Prevention Programs web page at www.osha.gov/dsg/topics/ safetyhealth for more information.
Compliance Assistance Specialists
OSHA has compliance assistance specialists throughout the nation located in most OSHA offices. Compliance assistance specialists can provide information to employers and workers about OSHA standards, short educational programs on specific hazards or OSHA rights and responsibilities, and information on additional compliance assistance resources. For more details, visit www.osha.gov/dcsp/compliance_assistance/cas.html or call 1-800-321-OSHA (6742) to contact your local OSHA office.
Free On-site Safety and Health Consultation Services for Small Business
OSHA’s On-site Consultation Program offers free and confidential advice to small and medium-sized businesses in all states across the country, with priority given to highhazard worksites. Each year, responding to requests from small employers looking to create or improve their safety and health management programs, OSHA’s On-site Consultation Program conducts over 29,000 visits to small business worksites covering over 1.5 million workers across the nation.
On-site consultation services are separate from enforcement and do not result in penalties or citations. Consultants from state agencies or universities work with employers to identify workplace hazards, provide advice on compliance with OSHA standards, and assist in establishing safety and health management programs.
For more information, to find the local On-site Consultation office in your state, or to request a brochure on Consultation Services, visit www.osha.gov/consultation, or call 1-800-321-OSHA (6742).
Under the consultation program, certain exemplary employers may request participation in OSHA’s Safety and Health Achievement Recognition Program (SHARP). Eligibility for participation includes, but is not limited to, receiving a fullservice, comprehensive consultation visit, correcting all identified hazards and developing an effective safety and health management program. Worksites that receive SHARP recognition are exempt from programmed inspections during the period that the SHARP certification is valid.
Cooperative Programs
OSHA offers cooperative programs under which businesses, labor groups and other organizations can work cooperatively with OSHA. To find out more about any of the following programs, visit www.osha.gov/cooperativeprograms.
Strategic Partnerships and Alliances
The OSHA Strategic Partnerships (OSP) provide the opportunity for OSHA to partner with employers, workers, professional or trade associations, labor organizations, and/or other interested stakeholders. OSHA Partnerships are formalized through unique agreements designed to encourage, assist, and recognize partner efforts to eliminate serious hazards and achieve model workplace safety and health practices. Through the Alliance Program, OSHA works with groups committed to worker safety and health to prevent workplace fatalities, injuries and illnesses by developing compliance assistance tools and resources to share with workers and employers, and educate workers and employers about their rights and responsibilities.
Voluntary Protection Programs (VPP)
The VPP recognize employers and workers in private industry and federal agencies who have implemented effective safety and health management programs and maintain injury and illness rates below the national average for their respective industries. In VPP, management, labor, and OSHA work cooperatively and proactively to prevent fatalities, injuries, and illnesses through a system focused on: hazard prevention and control, worksite analysis, training, and management commitment and worker involvement.
Occupational Safety and Health Training
The OSHA Training Institute partners with 27 OSHA Training Institute Education Centers at 42 locations throughout the United States to deliver courses on OSHA standards and occupational safety and health topics to thousands of students a year. For more information on training courses, visit www.osha.gov/otiec.
OSHA Educational Materials
OSHA has many types of educational materials in English, Spanish, Vietnamese and other languages available in print or online. These include:
- Brochures/booklets;
- Fact Sheets;
- Guidance documents that provide detailed examinations of specific safety and health issues;
- Online Safety and Health Topics pages;
- Posters;
- Small, laminated QuickCards™ that provide brief safety and health information; and
- QuickTakes, OSHA’s free, twice-monthly online newsletter with the latest news about OSHA initiatives and products to assist employers and workers in finding and preventing workplace hazards. To sign up for QuickTakes visit www.osha.gov/quicktakes.
To view materials available online or for a listing of free publications, visit www.osha.gov/publications. You can also call 1-800-321-OSHA (6742) to order publications.
Select OSHA publications are available in e-Book format. OSHA e-Books are designed to increase readability on smartphones, tablets and other mobile devices. For access, go to www.osha.gov/ebooks.
OSHA’s web site also has information on job hazards and injury and illness prevention for employers and workers. To learn more about OSHA’s safety and health resources online, visit www.osha.gov or www.osha.gov/html/a-z-index.html.
NIOSH Health Hazard Evaluation Program
Getting Help with Health Hazards
The National Institute for Occupational Safety and Health (NIOSH) is a federal agency that conducts scientific and medical research on workers’ safety and health. At no cost to employers or workers, NIOSH can help identify health hazards and recommend ways to reduce or eliminate those hazards in the workplace through its Health Hazard Evaluation (HHE) Program.
Workers, union representatives and employers can request a NIOSH HHE. An HHE is often requested when there is a higher than expected rate of a disease or injury in a group of workers. These situations may be the result of an unknown cause, a new hazard, or a mixture of sources. To request a NIOSH Health Hazard Evaluation go to www.cdc.gov/niosh/hhe/request.html. To find out more, in English or Spanish, about the Health Hazard Evaluation Program:
E-mail HHERequestHelp@cdc.gov or call 800-CDC-INFO (800-232-4636).
OSHA Regional Offices
Region I
Boston Regional Office
(CT*, ME*, MA, NH, RI, VT*)
JFK Federal Building, Room E340
Boston, MA 02203
(617) 565-9860 (617) 565-9827 Fax
Region II
New York Regional Office
(NJ*, NY*, PR*, VI*)
201 Varick Street, Room 670
New York, NY 10014
(212) 337-2378 (212) 337-2371 Fax
Region III
Philadelphia Regional Office
(DE, DC, MD*, PA, VA*, WV)
The Curtis Center 170 S.
Independence Mall West
Suite 740 West
Philadelphia,
PA 19106-3309
(215) 861-4900 (215) 861-4904 Fax
Region IV
Atlanta Regional Office
(AL, FL, GA, KY*, MS, NC*, SC*, TN*)
61 Forsyth Street, SW, Room 6T50
Atlanta, GA 30303
(678) 237-0400 (678) 237-0447 Fax
Region V
Chicago Regional Office
(IL*, IN*, MI*, MN*, OH, WI)
230 South Dearborn Street Room 3244
Chicago, IL 60604
(312) 353-2220 (312) 353-7774 Fax
Region VI
Dallas Regional Office
(AR, LA, NM*, OK, TX)
525 Griffin Street, Room 602
Dallas, TX 75202
(972) 850-4145 (972) 850-4149 Fax
(972) 850-4150 FSO Fax
Region VII
Kansas City Regional Office
(IA*, KS, MO, NE)
Two Pershing Square Building
2300 Main Street, Suite 1010
Kansas City, MO 64108-2416
(816) 283-8745 (816) 283-0547 Fax
Region VIII
Denver Regional Office
(CO, MT, ND, SD, UT*, WY*)
Cesar Chavez Memorial Building
1244 Speer Boulevard, Suite 551
Denver, CO 80204
(720) 264-6550 (720) 264-6585 Fax
Region IX
San Francisco Regional Office
(AZ*, CA*, HI*, NV*, and American Samoa,
Guam and the Northern Mariana Islands)
90 7th Street, Suite 18100
San Francisco, CA 94103
(415) 625-2547 (415) 625-2534
Fax
Region X
Seattle Regional Office
(AK*, ID, OR*, WA*)
300 Fifth Avenue, Suite 1280
Seattle, WA 98104
(206) 757-6700 (206) 757-6705 Fax
* These states and territories operate their own OSHA-approved job safety and health plans and cover state and local government employees as well as private sector employees. The Connecticut, Illinois, Maine, New Jersey, New York and Virgin Islands programs cover public employees only. (Private sector workers in these states are covered by Federal OSHA). States with approved programs must have standards that are identical to, or at least as effective as, the Federal OSHA standards.
Note: To get contact information for OSHA area offices, OSHAapproved state plans and OSHA consultation projects, please visit us online at www.osha.gov or call us at 1-800-321-OSHA (6742).
How to Contact OSHA
For questions or to get information or advice, to report an emergency, fatality, inpatient hospitalization, amputation, or loss of an eye, or to file a confidential complaint, contact your nearest OSHA office, visit www.osha.gov or call OSHA at 1-800-321-OSHA (6742), TTY 1-877-889-5627.
Occupational Safety and Health Act of 1970
“To assure safe and healthful working conditions for working men and women; by authorizing enforcement of the standards developed under the Act; by assisting and encouraging the States in their efforts to assure safe and healthful working conditions; by providing for research, information, education, and training in the field of occupational safety and health.”
For assistance, contact us.
We are OSHA. We can help.
Material contained in this publication is in the public domain and may be reproduced, fully or partially, without permission. Source credit is requested but not required.
This information will be made available to sensory-impaired individuals upon request. Voice phone: (202) 693-1999; teletypewriter (TTY) number: 1-877-889-5627.
This publication is intended to provide information about OSHA’s Excavations standards at 29 CFR Part 1926, Subpart P. The Occupational Safety and Health Act requires employers to comply with safety and health standards promulgated by OSHA or by a state with an OSHA-approved state plan. However, this publication is not itself a standard or regulation, and it creates no new legal obligations.
Trenching and Excavation Safety
U.S. Department of Labor
Occupational Safety and Health Administration
OSHA 2226-10R 2015