Summary Statement
Researchers from the Division of Safety Research of the National Institute for Occupational
Safety and Health (NIOSH) designed, developed, and patented a multifunctional guardrail system
(U.S. Patent No. 7,509,702) that can protect construction workers from falling to lower levels. This paper (#703) was presented at the 2015 ASSE annual meeting and reports on modifications, field testing, and training.
2015
Concurrent Education Session No. 703
Introduction
Fatal Incidents
Workers falling from elevations is the primary cause of fatalities in the U.S. construction industry. A compilation of data for the years 2008 through 2012 from the Census of Fatal Occupational Injuries (CFOI) database, which is maintained by the Bureau of Labor Statistics (BLS) is presented in Table 1 (BLS 2010ab; 2011ab; 2012ab; 2013abc; 2014abc). This Table includes the total number of fatalities in all U.S. industries and, as a comparison, the total number of construction-related fatalities (rows 1 and 3), as well as the total number of fall-related deaths for all U.S. industries and the construction industry (rows 2 and 4). Fall-related fatalities account for about 15% of all fatalities occurring in all U.S. industries. For the Construction industry, fallrelated fatalities average about 35% of all construction-related fatalities. Also in the Table, a separate listing of data is shown for construction workplace situations related to falls from roof edges, and falls through roof and floor holes, and existing skylights (row 5).
This particular category involves situations that could be addressed with a guardrail system to prevent workers on roofs from falling to a lower level.
Finally, other BLS data indicate that roofers are a definite high-risk worker group. The last two rows of data in Table 1 present the overall fatality rates for all construction occupations compared with the overall fatality rates for roofers from 2008 through 2012. For 2012, the fatality rate for roofers (end of row 7) was 42.2 deaths per 100,000 full-time equivalent (FTE) workers, which is more than 3 times the fatality rate of all construction workers (end of row 6), which was 12.9 deaths per 100,000 FTE workers (BLS 2014c).
Condition | 2008 | 2009 | 2010 | 2011 | 2012 |
---|---|---|---|---|---|
Total U.S. occupational fatalities | 5214 | 4551 | 4547 | 4693 | 4628 |
Total U.S. occupational fatal falls | 700 (13%) |
645 (14%) |
635 (14%) |
681 (15%) |
704 (15%) |
Total Construction fatalities | 975 | 834 | 751 | 738 | 806 |
Total Construction fatal falls | 336 (34%) |
283 (34%) |
260 (35%) |
262 (36%) |
290 (36%) |
Construction fatal falls involving roofsa and floor holes |
113 (34%)b (12%)c |
92 (33%)b (11%)c |
92 (35%)b (12%)c |
91 (35%)b (12%)c |
104 (36%)b (13%)c |
Overall fatality rate d all construction workers |
11.8 | 12.4 | 11.8 | 11.9 | 12.9 |
Overall fatality rate d for roofers |
34.4 | 34.7 | 32.4 | 34.1 | 42.2 |
aFrom roof edge, and through roof holes and skylights bPercentage value of "Total Construction fatal falls" cPercentage value of "Total Construction fatalities" dThe fatality rate is the number of fatal occupational injuries per 100,000 full-time equivalent workers |
Workers' Compendation Information
The focus of this paper is on using guardrails to prevent workers from falling from elevated workplaces in residential construction. OSHA has developed an on-line presentation that discusses data from the National Council on Compensation Insurance (NCCI), which indicates that for the period 2005 to 2007, “falls from elevations by roofers cost an average of $106,000.” (OSHA on-line presentation 2012) “The data come from statistics collected from insured employers in 36 states, which comprises approximately 1/3 of total workers’ compensation benefits paid out annually in the US. Self-insured firms and companies in 13 states are not included.” (OSHA on-line 2012)
“Thirty-six States (AK, AL, AZ, AR, CO, CT, DC, FL, GA, HI, ID, IL, IA, KS, KY, LA, ME, MD, MS, MO, MT, NE, NV, NH, NM, OK, OR, RI, SC, SD, TN, TX, UT, VT, VA, WV) report workers’ compensation data for insured employers to [NCCI].” (OSHA on-line 2012) “Among insured roofers for the…policy years 2005-2007 in [the 36] NCCI states, there were reports of 1,511 ‘fall or slip injuries’ from elevations.” (OSHA on-line 2012) The total “incurred (expected) claims costs of ‘falls from elevation’ by insured roofers” for the 3 years was approximately $161 million ($41 million in 2005 plus $65 million in 2006 plus $55 million in 2007) (OSHA on-line 2012). Dividing $161 million by 1,511 total claims results in $106,552 per claim. “In each case, approximately $36,000 was allocated for indemnity (wage replacement) benefits, while $70,000 was for medical care.” (OSHA on-line 2012)
Of course, not every “fall-from-elevation” incident will result in such an excessive cost. But these values certainly should alert construction contractors to the potential of such happenings. By spending a modest amount for a guardrail system, especially one that could be used for multiple job tasks, then that would be a wise investment for a safer workplace.
Fall-related OSHA requirements for construction
Fall-related hazards in the construction industry are enforced by OSHA through Subpart M (Fall Protection) of the Code of Federal Regulations (CFR), Title 29 (Labor), Part 1926 (Construction). Subpart M became effective on February 6, 1995 and contains fall protection requirements for construction work. Additional fall protection requirements can be found throughout Part 1926. Specific requirements for residential construction are explained in section 1926.501(b)(13). This section states that “workers engaged in residential construction six feet or more above lower levels must be protected by conventional fall protection (i.e., guardrail systems, safety net systems, or personal fall arrest systems) or alternative fall protection measures allowed under 1926.501(b) for particular types of work.” (OSHA on-line Residential Construction Q & A)
Guardrail systems must comply with OSHA 1926(b)(3) which states, “Guardrail systems shall be capable of withstanding, without failure, a force of at least 200 pounds (890 N) applied within 2 inches (5.1 cm) of the top edge, in any outward or downward direction, at any point along the top edge.” (OSHA on-line Regulations 2014)
Guardrails can be used to protect workers from falling through unprotected holes and from unprotected roof edges. “Guardrail systems, whether commercially available or built onsite, can provide protection for unguarded roof edges (steep slope and low slope) or interior edges, including balconies or stairways, during residential, commercial, and industrial construction and renovation activities.” (Bobick and McKenzie 49)
NIOSH-developed Guardrail System
Researchers from the Division of Safety Research of the National Institute for Occupational Safety and Health (NIOSH) designed, developed, and patented a multifunctional guardrail system (U.S. Patent No. 7,509,702) that can protect construction workers from falling to lower levels. The original design was developed for use on steep-sloped roofs in residential construction (Bobick and McKenzie, 2011). The bracket that attached to the roof was designed to provide a level walking/working surface for workers and is adjustable to be installed on seven different roof slopes, including 6:12 (27°), 8:12 (34°), 10:12 (40°), 12:12 (45°), 15:12 (51°), 18:12 (56°), and 24:12 (63°, also known as A-frame). Figure 1 shows a typical configuration of the original design of the NIOSH guardrail system for use on steep-sloped roofs. Through extensive lab testing, the final design supported more than twice OSHA’s top-rail strength requirement of 200 pounds when anchored with nails (Bobick and McKenzie 50), and when screw fasteners were used, the system supported more than three times the OSHA strength requirement (unpublished NIOSH data).
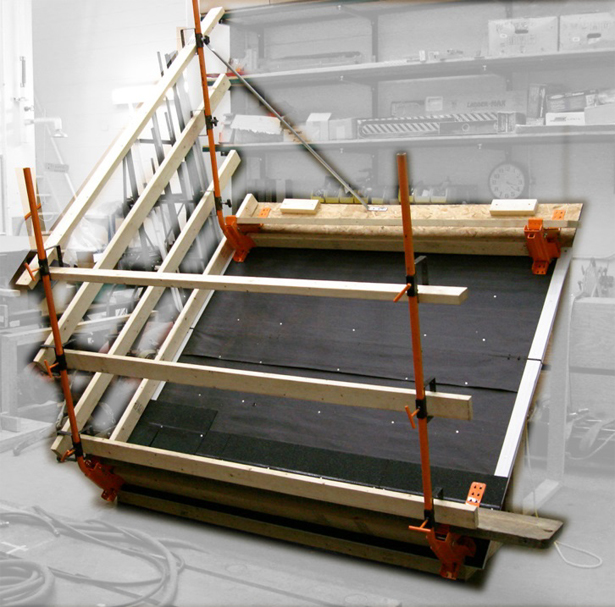
Figure 1. Shown is a typical configuration of the original design of the NIOSH guardrail system.
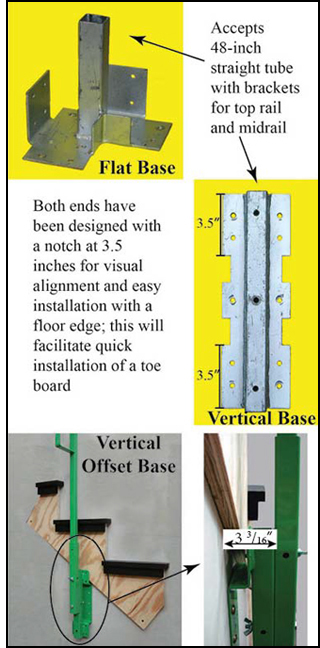
Figure 2. Additional guardrail bases (flat,
vertical, and vertical offset) were developed
with input from construction
contractors.
Based on input from construction contractors, three variations of the original design were developed. Work site visits by the NIOSH research team to Florida and North Carolina were scheduled to demonstrate the functionality of the guardrail system to local contractors. Those two site visits, along with personal discussions with a Virginia-based contractor, resulted in getting practical input from the contractors, who pointed out additional needs for fall protection. These suggestions resulted in three modifications to the original design to address those needs – specifically the flat, vertical, and vertical offset bases. Photos of these guardrail bases are shown in Figure 2 (top, middle, and bottom, respectively). These three variations of the original design permitted the guardrail system to be used on flat and vertical surfaces that also need fall protection, such as unprotected floor holes, second-story floor edges without bannisters, or staircases without handrails, to name a few. Detailed descriptions of those designs have been discussed in Bobick and McKenzie (2011).
A fifth and final design was developed by the NIOSH research team. As mentioned, the roof bracket provides a level walking-working surface anywhere on a steep-sloped roof. On-site observations by the project team indicated that some contractors used a commercially available roofing bracket (sometimes referred to as a “roof jack”) to install a walking-working surface at the downslope edge (eave edge) of the roof for basic slide protection (Figure 3.1). Other contractors use 2-by-4 lumber nailed to the roof (Figure 3.2) or a combination of 2-by-6s supported by 2-by-4s (Figure 4) to serve as a slide guard or to provide something to brace their foot against while working on the roof.
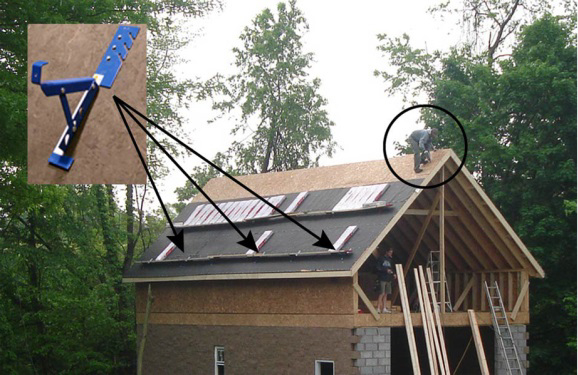
Figure 3.1 Typical roof construction, using roof jacks (inset, upper left) for
placement of supplies
and fall protection. An unrestrained worker is shown (in circle) at
the roof peak.
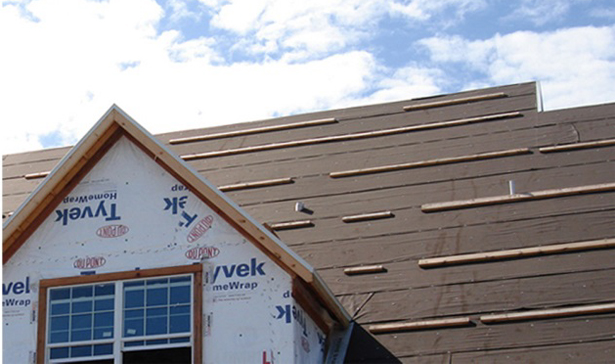
Figure 3.2 Typical roof construction, using 2-by-4 lumber for fall protection.
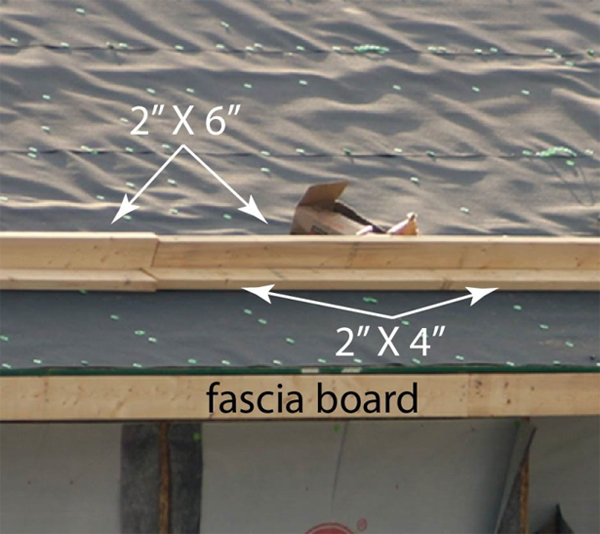
Figure 4. Typical roof construction, using 2-by-6 and 2-by-4 lumber for fall protection.
After observing these different slide guard variations, the fifth NIOSH design was
developed that focuses on providing the worker with a slide guard-guardrail option. It permits 2-
by-6 lumber to be placed into a U-channel to serve as a traditional slide guard, as shown in Figure
5.
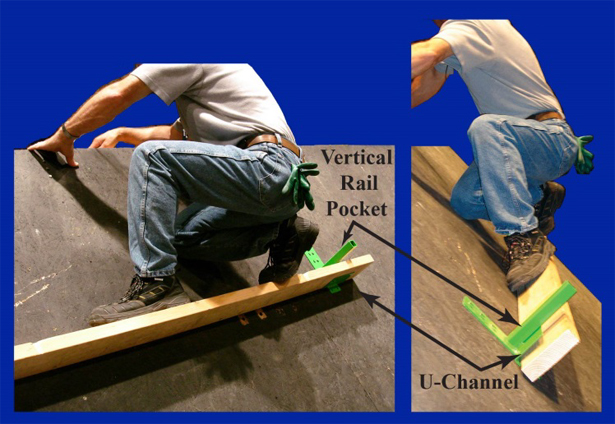
Figure 5. Two views of the slide guard base with
2-by-6
lumber inserted into the U-channel.
The slide guard base incorporates a pocket for the vertical post, which is common to all of the base designs. This allows a guardrail to be constructed, consisting of a top rail, midrail, and toeboard by inserting the vertical post with three adjustable horizontal support brackets (for 2-by-4 lumber for the top rail, mid rail, and toeboard). Adjoining slide guard bases are installed at eight-foot intervals across the roof, resulting in a slide guard that can easily be transformed into an OSHA-compliant guardrail system. If needed, a walking-working surface can be added to the configuration by installing the aforementioned roof jacks (shown in Figure 3, left). Figure 6 shows the completed 8-foot section of the combination slide guard-guardrail fixture and, a worker standing on the roof jack set-up.
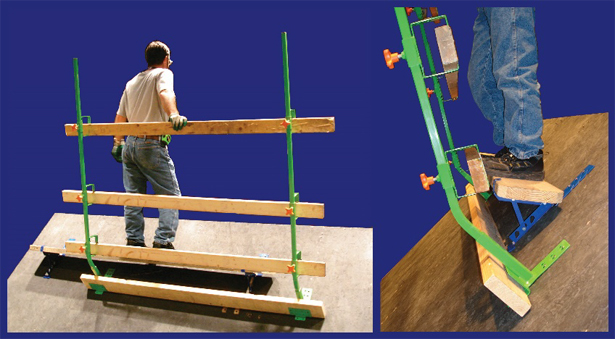
Figure 6. Two views of slide guard base set-up, equipped
with an OSHA-compliant guardrail.
Because of the popularity of slide guard usage in residential construction, OSHA decreed
in 1995 (Directive STD 3.1) that in certain specific instances, slide guards could be used to fulfill
the requirements for a fall protection system in residential construction. In 2011, OSHA
rescinded this 1995 Directive and eliminated the use of slide guards as the “sole means” of achieving an approved fall protection plan. OSHA did not eliminate the use of slide guards; the Agency requires them to be used in conjunction with the regulations of Subpart M of 29 CFR 1926 (mentioned earlier). Thus, the slide guard base of the NIOSH system is a variation to the popular slide guard, since it can accommodate the vertical pole and adjustable brackets that support the cross-lumber to quickly construct an OSHA-compliant guardrail system.
Field Evaluation of NIOSH Guardrail System
A contract was established with the West Virginia University Safety and Health Extension (WVUS&HE) to assist the NIOSH research team in conducting a field evaluation of the guardrail system at residential job sites in the Morgantown, WV area. The guardrail system consisted of all five components (original roof slope, flat, vertical, vertical offset, and slide guard options) that were developed for different fall prevention needs. The WVUS&HE, in conjunction with NIOSH, Division of Safety Research, developed a training program focusing on the installation of all five components of the guardrail system, but also on the OSHA Fall Protection requirements. The WVUS&HE coordinated with the North Central West Virginia Home Builders Association to identify residential contractors or appropriate sub-contractors that would be willing to use the guardrail system during actual working conditions.
Residential construction contractors recruited and trained
WVUS&HE recruited two residential contractors to participate in the field study to evaluate the guardrail system. Contractor 1 is a family-owned business consisting of six employees. Typically, this contractor does the majority of all the work on the home, so it is involved with the project from job-site preparation through completion of all work and turning keys over to the new owner. This contractor completes a home in three to four months. Contractor 2, which has 20 employees (one crew of 10 employees was recruited), is a framing sub-contractor that works in conjunction with a general contractor. The sub-contractor frames the entire house in about four to five days, installs the wood sheathing to the roof trusses, and installs the weatherproof underlayment material on the sheathing. They do not install shingles on the roof. That task is completed by a separate sub-contractor.
Once the workers and supervisors from both contractors agreed to participate with the field study, they received training from two WVUS&HE researchers. Prior to the training, all participants received forms that would be signed and that explained (a) the scope of the field study and (b) that the participants were agreeing to use the different components of the guardrail system. At the same time, photo release forms were also signed by each participant.
The half-day training consisted of in-class instructions on: (a) the OSHA Fall Protection Standards for Construction (Subpart M) for general knowledge, and (b) the installation of the NIOSH guardrail system using instructions prepared by the NIOSH research team. The in-class portion used photographs and video almost exclusively, and very little text materials. Half of the training session was outside and utilized hands-on practice with installing all components of the guardrail system. Figure 7 (left) shows workers from contractor 1 referring to instructions and figure 7 (right) shows workers from contractor 2 installing the original design on the roof and the vertical design along the sloped edge (“rake” edge) of the WVU mobile rooftop training trailer.
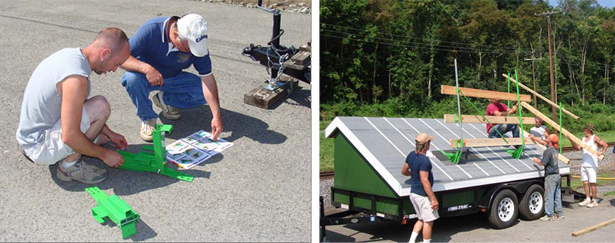
Figure 7. Left - Contractor 1 workers using the NIOSH-prepared instruction to set roof
bracket slope angle.
Right – Contactor 2 workers installing the guardrail system on the
WVU mobile rooftop training trailer.
After the hands-on practice, the trainees re-assembled in the classroom to discuss any questions they may have had about the various components of the guardrail system, as well as provide comments related to the installation practice portion. Before finishing, both contractors received multiple sets of all the different components to the guardrail system. The WVUS&HE researchers reminded both contractors to use the guardrail system whenever they determined that the guardrail was needed and could be used safely.
Part of the training session for both contractors included an evaluation of the participants’ knowledge about safety on the job. The two WVUS&HE researchers developed a pre-test and a post-test to measure the workers’ knowledge gain as a result of the training class. The test was limited to the topics covered for the OSHA Construction Fall Protection Regulations (Subpart M), and did not include the NIOSH guardrail system.
The pre-test and post-test was administered on the day of training. There was also a follow-up post-test conducted at the end of the 6-month field evaluation. Although the follow-up post-test results were obtained from contractor 1, the follow-up post-test could not be administered to contractor 2 because more than half of the crew had left.
Both contractors had a substantial increase in knowledge related to the OSHA Fall Protection requirements immediately following the training. The average scores for all workers of both contractors are shown in Table 2.
Average pre-training scores | Average posttraining scores | Average scores for 6-month follow-up | |
---|---|---|---|
Contractor 1 | 80% | 98% | 68% |
Contractor 2 | 60% | 89% | Could not collect |
Along with the testing of OSHA Subpart M knowledge, all participants who received the training were asked to provide some background on their experience related to working at elevations and the use of safety equipment. These oral responses provided the basis for free-form discussions among the participants, the WVU trainers, and occasionally the NIOSH research team who attended both training sessions. The workers’ responses indicated that all participants spent a good deal of their time working at heights, and that they were exposed to a variety of fall hazards. The workers of one contractor responded that they normally did not use fall protection systems or personal fall arrest equipment.
Comments made by the two participating contractors prior to the two training sessions indicated that fall-prevention equipment or fall-protection safety gear was not often considered during the construction activities. However, post-training discussions indicated that all of the workers and owners would consider using the NIOSH guardrail system in the future to control fall hazards. After receiving the training, comments from the owners included: “I can see using this guardrail on steep roofs. It will make the guys less tense. I think the additional time to install the guardrail will be made up in productivity.” and “I could see us using all of [the components].”
Field Evaluations
Pre-training and Post-Training Site Visits WVUS&HE conducted a baseline fall hazard job-site audit prior to the training sessions, and several times after the training had occurred. The audit was performed with the Fall-Safe audit tool (Fullen and Takacs 2004). The audit score is the percentage of potential fall hazards that were being controlled based on the OSHA Construction regulations. The audit results (shown in Table 3) did not match with the pre- and post-knowledge assessment collected prior to and after the training session (Table 2). The ease of installation and familiarity that resulted from the hands-on training resulted in contractors correctly installing the guardrail when they determined that there was an immediate danger, such as working on steep-sloped roofs or at extreme heights. However, there were some instances when the contractors may not have used the guardrail system when OSHA regulations may have required the use of fall protection. This happened primarily because of the contractors’ perception of minimal fall hazards, such as working on lower sloped roofs or at lower heights.
Average baseline (pre-training) fall hazard score | Average post-training fall hazard score | |
---|---|---|
Contractor 1 | 34% | 78% |
Contractor 2 | 19% | 52% |
The two contractors used the various guardrail system components during their normal construction activities. Positive feedback was provided by both contractors. The following photos show the various ways that different guardrail base options were used to help create a safe working environment. During the field site visits, WVU also collected data on the time to install an 8-foot guardrail section. Nine separate guardrail installations were timed to determine an average installation time. The average time to install one 8-ft section of guardrail, including all fasteners and cross-rails (i.e., top rail, mid-rail, and toeboard) was 5.8 minutes. This time included setting the angles of two bases and installing them, inserting two vertical poles, sliding three support brackets on each pole, and then sliding lumber through the support brackets and securing them in place to complete the top rail, mid-rail, and toeboard. The first section takes the longest since it has two of everything. The next 8-foot section requires the installation of just one rooftop base set to the correct angle, inserting one vertical pole, sliding on three support brackets, and inserting lumber for the top, mid, and bottom of the guardrail. After the first section, each subsequent section along the roof is much quicker. Since roofing is completed on one side, then on the other, a guardrail would be set for one half of the roof first, then the other half. For one side of a typical 20 ft by 40 ft roof (along the drip edge only; not up the slope), the time to set the guardrail along the 40 foot length might be about 25 to 30 minutes. A similar amount of time would be required for the second half of the roof.
Contractor 2 Site Visits
Figure 8 (left) shows how contractor 2 used the vertical offset base to protect the perimeter of the first floor while sheathing, and then left it in place to provide protection when the second story walls were erected (Figure 8, right).
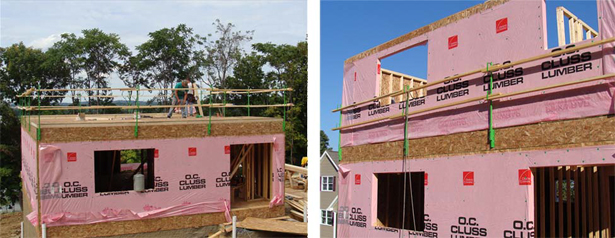
Figure 8. Left - A guardrail system is using vertical offset bases for an unguarded floor perimeter.
Right – Vertical offset system was left in place while second story walls were set.
Additional photos taken during the construction of this residence show the guardrail
system was used on sloped surfaces on the garage and on the roof. Figure 9 shows a worker
using the walking-working surface of the guardrail system while handling a piece of roofing
material. Having a flat working surface to stand on made it much easier to complete sheathing
the roof after the guardrail system had been installed along the leading edge. The garage set-up is
shown on the right of the house. The slope of both roofs is 6:12 (27°).
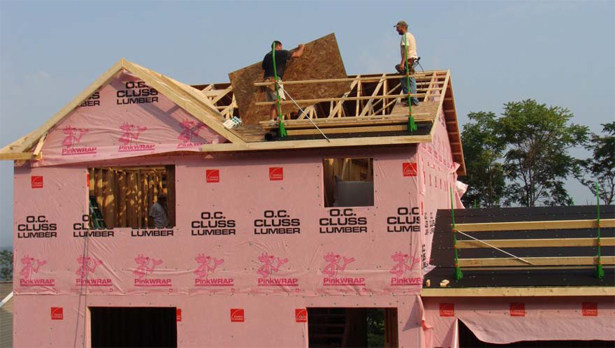
Figure 9. Guardrails were installed on the leading edge of the
roof and garage
(both 27° slope).
The next residence constructed by this contractor had a much steeper roof. Figure 10
shows that two guardrail systems were installed on a 12:12 (45°) roof slope. This provided
additional protection and the workers commented that they felt much safer with the guardrails in
place.
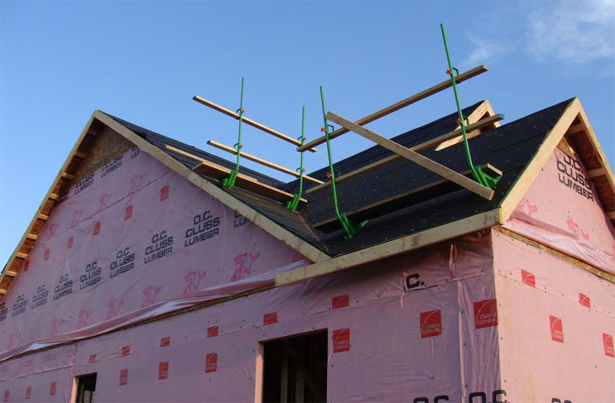
Figure 10. Two guardrail systems were installed on a 45° sloped roof.
Contractor 1 Site Visits
The smaller of the two contractors was visited second. This family-owned business was constructing a very large residence and their overall approach to the construction process was more methodical because of fewer workers who were tasked with having more responsibilities. Figure 11 shows the use of the vertical offset base for edge protection on the first floor.
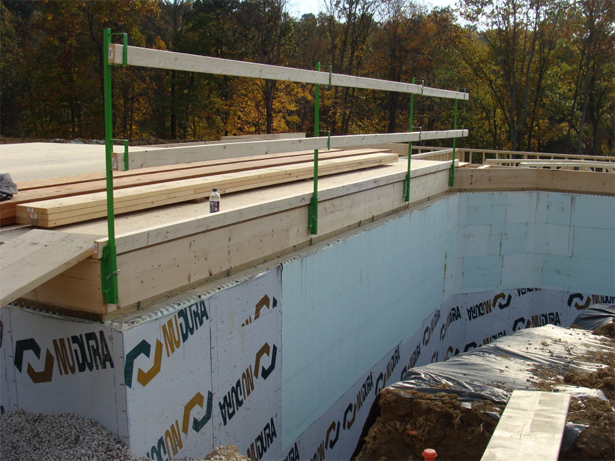
Figure 11. Vertical offset system was used for first floor guarding.
Other uses for the guardrail system included internal and external requirements. Figure
12 (left) shows the flat system being used to install a temporary hand rail for a curved staircase.
Although it was “temporary,” it was actually in place for more than six months and proved to be
quite durable. At the top of the stairs, additional flat bases were used to install a protective
guardrail for the exposed edge to the left and to the right of the staircase, prior to having the
second floor bannister installed (figure 12, right).
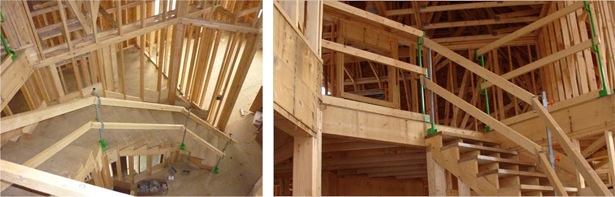
Figure 12. Left Flat base system was used to make a secure handrail on a curved staircase.
Right Flat bases were used to construct a guardrail along exposed floor edges to the left and
right of the staircase.
Figure 13 shows two guardrail systems installed on the rear roof (45° slope) of this
residence. The NIOSH system provides a walking-working surface for the workers, and “on the
spot” guardrail protection while installation of the roof sheathing and weatherproof underlayment
material were completed upslope.
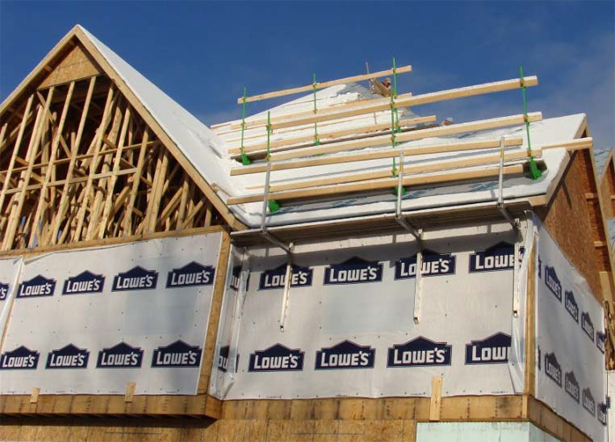
Figure 13. Two guardrails installed on a 45° sloped roof.
Figure 14 shows a NIOSH researcher demonstrating to the owner of the construction
company how the vertical offset base could be used to install a guardrail on the fascia board
ahead of any roof construction. This would permit workers to be protected while installing the
sheathing, weatherproof underlayment material, and the shingles. This set-up would be installed
only once and left in place to provide a safe work environment during all roofing activities.
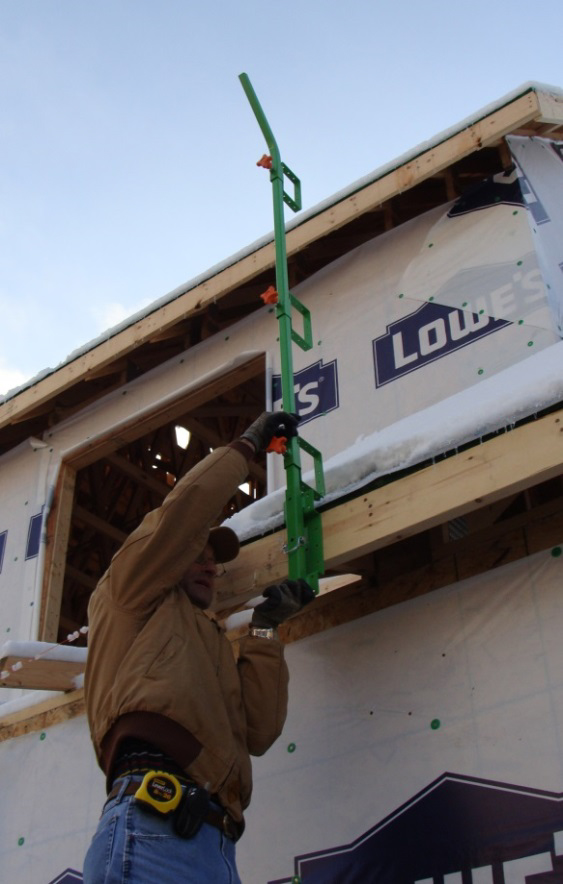
Figure 14. NIOSH researcher showing
use of offset base on fascia board. This
set-up would be installed
only once and
left in place during all roofing activities.
Commercial Product
“NIOSH has signed a…licensing agreement with Reese Wholesale (Indianapolis, Indiana) to commercialize the NIOSH-designed and patented roof bracket and safety rail system. … Product information…may be found at www.reesewholesale.com. (NIOSH eNews 2015 9).
With OSHA focusing on Subpart M through their new directive (STD-03-11-02) which rescinded the interim fall protection standards (STD 3.1 and STD 03-00-001), the emphasis will be re-focused on guardrails, netting systems, and personal fall protection. This fall prevention system may help to fill the safety gap by providing an easily installed, multifunctional guardrail system for a variety of job sites in residential, industrial, and commercial construction.
Discussion
Contractor Feedback
The NIOSH guardrail system was initially designed for use on steep-sloped roofs (6:12 through 24:12). With input from a variety of construction contractors, four new designs were developed. This enhanced system can be used on flat, vertical and sloped surfaces in residential, commercial, and industrial construction. Feedback from the workers who used the guardrail components during the field study indicated their acceptance of the system. Even though the original NIOSH steep-sloped configuration was heavier than the roofing bracket normally used (figure 3), the workers understood that the system had to be more substantial to be effective since it provided an additional fall prevention guardrail. One owner from the two participating contractors indicated that the normal roofing brackets tended to last only one building season and then were thrown away, but the components of the NIOSH system were more durable and definitely lasted longer.
An interesting aspect regarding a change to the workplace is how quickly workers adapted to it. During one site visit for the field study, after the guardrail had been installed on the roof, one of the workers shot a nail into the top rail to hang his air-powered nail gun. The research team realized that the job site was improved further because a tripping hazard had been eliminated.
Owners of both participating contractors stated that they liked the overall system and it was easy to use. The owners of contractor 1 stated that they intended to use the system on future jobs. After the completion of the field study, they have been utilizing the various components of the NIOSH guardrail system on their construction jobs over the past three years. The company owners have stated that using the guardrail system is “now part of our daily routine,” and that their workers “feel safer and work more confidently” with the guardrail in place.
Commercial Product Outcome
The licensing agreement was signed in May 2014. By August, the guardrail system was being used by three Indianapolis contractors to evaluate and provide feedback about the product (now called “The Protector”) to Reese personnel. In October, a 240-pound worker was doing repair work on a wood shake roof with a slope of 9:12 (37°). At some point, the worker slipped and slid about 20 feet downslope to The Protector guardrail installed at the eave edge of the roof. The worker was stopped by the guardrail system and prevented from falling about 18 feet onto a concrete sidewalk. This direct outcome of using The Protector system prevented a serious injury from occurring, and perhaps, depending on how the worker might have landed, even saved his life. This is definitely the most positive outcome that the research team could have expected to occur when the guardrail system was being used in the workplace.
Conclusions
Falls to a lower level are the primary cause of fatal injuries in construction. Typically, one of every three fall-related fatalities involves workers falling from roof and interior edges, or falling through roof holes or skylights. Such falls can be prevented by the use of guardrails. The NIOSH guardrail system was evaluated in a 6-month field study. The following conclusions were made regarding the training portion of the study and after those are conclusions related to the field evaluation portion.
Training Portion
- There was an initial increase in knowledge gained regarding the OSHA Fall Protection Standards.
- The “hands-on” portion of the training sessions indicated that the contractors were able to install and use the NIOSH guardrail system properly.
- The training curriculum and fall hazards presented during the hands-on portion were accepted by the contractors as applicable to the industry and their current workload.
- During the post-training fieldwork, the experience gotten from the hands-on training while installing the guardrail was applied during actual construction activities.
- The short amount of time that it took the contractors to install an 8-ft section of the guardrail (about 6 minutes) positively impacted the contractor’s decision to continue to use the guardrail system.
Field Evaluation Portion
- The collaboration between the North Central WV Home Builders Association, the two contractors, WVUS&HE, and NIOSH Division of Safety Research worked well during this project.
- The guardrail system has been accepted by both workers and owners of the two participating companies.
- Both workers and owners felt that using the system was intuitive and was easy to install and use.
- All five of the guardrail system components (original design, flat, vertical, vertical offset, and slide guard) were used by the contractors during the field study.
- Both owners felt that the system provided a safe work environment on steep-sloped roofs, especially while working at excessive heights.
- The guardrail system was designed for durability to maintain its functionality for re-use over multiple building seasons.
- The construction workers’ and owners’ knowledge of the OSHA Fall Protection regulations decreased over time, but this did not limit their ability to properly install the guardrail system.
- The construction workers and owners did not utilize the intervention system based solely on OSHA regulations. The contractors determined whether the risk was significant and that the intervention would actually assist them with the jobs that had to be completed.
- The practical nature of the NIOSH guardrail system indicates that an early investment in safety may very well prevent a costly tragedy from occurring in the future. Both contractors echoed this idea during the follow-up field evaluations.
References
Bobick, T.G. and E.A. McKenzie, Jr, (2011), Construction Guardrails – Development of a multifunctional system, Professional Safety, 56(1), 48-54, (January) .
Bureau of Labor Statistics, (2010a), Fatal occupational injuries by event or exposure and major private industry division, All U.S., 2008, (Table A-9), http://www.bls.gov/iif/oshwc/cfoi/cftb0240.pdf
Bureau of Labor Statistics, (2010b), Fatal occupational injuries, total hours worked, and rates of fatal occupational injuries by selected worker characteristics, occupations, and industries, civilian workers, 2008, http://www.bls.gov/iif/oshwc/cfoi/cfoi_rates_2008hb.pdf
Bureau of Labor Statistics, (2011a), Fatal occupational injuries by event or exposure and major private industry division, All U.S., 2009, (Table A-9), http://www.bls.gov/iif/oshwc/cfoi/cftb0249.pdf
Bureau of Labor Statistics, (2011b), Fatal occupational injuries, total hours worked, and rates of fatal occupational injuries by selected worker characteristics, occupations, and industries, civilian workers, 2009, http://www.bls.gov/iif/oshwc/cfoi/cfoi_rates_2009hb.pdf
Bureau of Labor Statistics, (2012a), Fatal occupational injuries by event or exposure and major private industry division, All U.S., 2010, (Table A-9), http://www.bls.gov/iif/oshwc/cfoi/cftb0258.pdf
Bureau of Labor Statistics, (2012b), Fatal occupational injuries, total hours worked, and rates of fatal occupational injuries by selected worker characteristics, occupations, and industries, civilian workers, 2010, http://www.bls.gov/iif/oshwc/cfoi/cfoi_rates_2010hb.pdf
Bureau of Labor Statistics, (2013a), Fatal occupational injuries by event or exposure, All U.S., 2011, (Table A-1), http://www.bls.gov/iif/oshwc/cfoi/cftb0259.pdf
Bureau of Labor Statistics, (2013b), Fatal occupational injuries by primary and secondary sources of injury for all fatal injuries and by major private industry, All U.S., 2011 (Table A- 4), http://www.bls.gov/iif/oshwc/cfoi/cftb0262.pdf
Bureau of Labor Statistics, (2013c), Fatal occupational injuries, total hours worked, and rates of fatal occupational injuries by selected worker characteristics, occupations, and industries, civilian workers, 2011, http://www.bls.gov/iif/oshwc/cfoi/cfoi_rates_2011hb.pdf
Bureau of Labor Statistics, (2014a), fatal occupational injuries by event or exposure, All U.S., 2012, (Table A-1), http://www.bls.gov/iif/oshwc/cfoi/cftb0268.pdf
Bureau of Labor Statistics (2014b), Fatal occupational injuries by primary and secondary sources of injury for all fatal injuries and by major private industry, All U.S., 2012, (Table A- 4. http://www.bls.gov/iif/oshwc/cfoi/cftb0271.pdf
Bureau of Labor Statistics (2014c), Fatal occupational injuries, total hours worked, and rates of fatal occupational injuries by selected worker characteristics, occupations, and industries, civilian workers, 2012. http://www.bls.gov/iif/oshwc/cfoi/cfoi_rates_2012hb.pdf
Fullen, M. and Takacs, B. (2004). Use of an Audit Tool for Fall Hazard Reduction on Construction Sites. Proceedings of the American Industrial Hygiene Conference and Exposition: Promoting Occupational and Environmental Health and Safety Excellence. Atlanta, GA, May 8-13, 2004. CR320. Abstract retrieved from https://www.aiha.org/aihce04/handouts.htm
NIOSH eNews (2015), r2p Corner: NIOSH-developed Roof Bracket and Safety Rail System Now Commercially Available, Feb, pg.9. http://www.cdc.gov/miosh/enews/enewsV12N10.html
OSHA Safety and Health Regulations for Construction (2014), 29 CFR 1926, Subpart M, Fall Protection. https://www.osha.gov/laws-regs/regulations/standardnumber/1926/1926SubpartM
OSHA On-line Presentation (2012), Workers’ Compensation Costs of Falls in Construction, http://www.osha.gov/doc/topics/residentialprotection/2012_fall_costs/index.html
OSHA On-line Information, (no date), Residential Construction Questions and Answers, https://www.osha.gov/doc/residential-construction/residential-construction-qa.html accessed on January 24, 2015.
Reese Wholesale website (2014) for information on The Protector Guardrail System: http://www.reesewholesale.com/safety/protector-guardrails.html or contact Susan Ragan, Director of Sales and Marketing, at 765-776-2058.
Thomas G. Bobick, Ph.D., P.E., CSP, CPE
Research Safety Engineer
NIOSH, Division of Safety Research
Morgantown, WV
Brandon C. Takacs, M.S., CSHM
Assistant Professor
West Virginia University Safety and Health Extension
Morgantown, WV
E. A. McKenzie, Jr., Ph.D., P.E.
Research Safety Engineer
NIOSH, Division of Safety Research
Mark D. Fullen, Ed.D, CSP
Associate Professor
West Virginia University Safety and Health Extension
Douglas M. Cantis
Engineering Technician
NIOSH, Division of Safety Research
Disclaimer
The findings and conclusions in this report are those of the authors and do not represent the views of NIOSH or West Virginia University. The mention of company names and products does not imply endorsement by NIOSH or WVU.