Protecting Construction Workers in Confined Spaces: Small Entity Compliance Guide
Summary Statement
This guide is intended to help small businesses comply with
OSHA's Confined Spaces standard. It addresses the most common
compliance issues that employers will face and provides
sufficient detail to serve as a useful compliance guide.
September 2015
Table of Contents
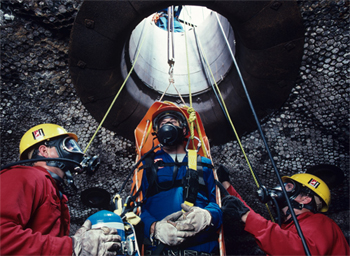
CHAPTER 1 Confined Spaces and Permit Spaces
CHAPTER 2 Work Covered by the Standard
CHAPTER 3 Employer Responsibilities
CHAPTER 4 Overview of the Standard
CHAPTER 5 Identifying Permit Spaces (Section 1203(a))
CHAPTER 6 Content of Permit Space Program (Sections 1204-1206)
CHAPTER 7 Reclassifying a Permit Space as a Non-Permit Space (Section 1203(g))
CHAPTER 8 Alternate Procedures for Certain Permit Spaces — Section 1203(e))
CHAPTER 9 Entrants, Attendants, and Entry Supervisors (Sections 1208-1210)
CHAPTER 10 Worker Training (Section 1207)
CHAPTER 11 Rescue and Emergency Services (Section 1211)
CHAPTER 12 Sewer System Entry
CHAPTER 13 Additional Information
APPENDIX A Example of a Permit-Required Confined Space Program
APPENDIX B Sample Entry Permit
Workers’ Rights
OSHA Assistance, Services and Programs
NIOSH Health Hazard Evaluation Program
OSHA Regional Offices
How to Contact OSHA
Introduction
1. The special dangers of confined spaces.
A confined space is a space whose configuration and/or contents may present special dangers not found in normal work areas. Confined spaces may be poorly ventilated and, as a result, contain insufficient oxygen or hazardous levels of toxic gases. Working in a tight space can prevent a worker from keeping a safe distance from mechanical and electrical hazards in the space. Fumes from a flammable liquid that is used in a poorly ventilated area can reach explosive levels. Such hazards endanger both the workers in the confined space and others who become exposed to the hazards when they attempt to rescue injured workers. In a number of cases, rescue workers have themselves died or been injured because they did not have the training and equipment necessary to conduct the rescue safely.
Because confined spaces are potentially dangerous, employers must evaluate all confined spaces in which their employees work to determine whether hazards exist or whether the work to be done in the space can create hazards. If a confined space contains an actual or potential hazard that can cause death, injury or acute illness, incapacitation, entrapment, or otherwise interfere with a worker’s ability to leave the space in an emergency, it is a permit-required confined space, or permit space. Employers must take certain precautions whenever workers enter a permit space. These include (1) specifying the precautions to be taken to protect the workers in the space; (2) training the workers who are covered by the standard to give them the knowledge to protect themselves and others; and (3) planning how to rescue injured workers promptly and safely.
2. The purpose and limits of this guide.
This guide is intended to help small businesses comply with the Confined Spaces standard. It addresses the most common compliance issues that employers will face and provides sufficient detail to serve as a useful compliance guide. It does not, however, describe all provisions of the standard or alter the compliance responsibilities set forth in the standard, which is published at 29 CFR §§ 1926.1200-1213. The reader must refer to the standard itself, which is available on OSHA’s website and in the Code of Federal Regulations, to determine all of the steps that must be taken to comply with the standard.
CHAPTER 1
Confined Spaces and Permit Spaces
The distinction between confined spaces and permit spaces is crucial to understanding what the standard requires. Briefly, a permit space is a confined space containing a serious hazard or hazards. Employers must evaluate all confined spaces to determine whether they are permit spaces but must take steps to protect workers only if a space is classified as a permit space.
What is a “confined space?”
A confined space is a space that:
(1) Is large enough and so arranged that an employee can bodily enter it;
(2) Has limited or restricted means for entry and exit; and
(3) Is not designed for continuous employee occupancy.
A space has a limited or restricted means of exit if a person could not readily escape from the space in an emergency. Any of the following factors indicate that a work space has a limited or restricted means of exit:
- The need to use a ladder or movable stairs, or stairs that are narrow or twisted;
- A door that is difficult to open or a doorway that is too small to exit while walking upright;
- Obstructions such as pipes, conduits, ducts, or materials that a worker would need to crawl over or under or squeeze around;.
- The need to travel a long distance to a point of safety.
A space is not designed for continuous employee occupancy if it is not designed with features such as ventilation, lighting, and sufficient room to work and move about that are needed if people are to occupy it continuously.
Confined spaces that may be found on construction sites include, but are not limited to:
- Manholes (such as sewer, storm drain, electrical, communication, or other utility)
- Sewers
- Storm drains
- Water mains
- Lift stations
- Tanks (such as fuel, chemical, water or other liquid, solid or gas)
- Pits (such as elevator, escalator pump, valve or other equipment)
- Bins
- Boilers
- Incinerators
- Scrubbers
- Concrete pier columns
- Transformer vaults
- Heating, ventilation, and airconditioning (HVAC) ducts
- Precast concrete and other pre-formed manhole units
- Drilled shafts
- Enclosed beams
- Vessels
- Digesters
- Cesspools
- Silos
- Air receivers
- Sludge gates
- Air preheaters
- Transformers
- Turbines
- Chillers
- Bag houses
- Mixers/reactors
- Crawl spaces
- Attics
- Basements (before steps are installed).
What is a “permit space?”
A permit-required confined space (permit space) is a confined space that:
(1) Contains or has the potential to contain a hazardous atmosphere;
(2) Contains a material that has the potential for engulfing an entrant;
(3) Has an internal configuration such that an entrant could be trapped or asphyxiated by inwardly converging walls or by a floor which slopes downward and tapers to a smaller cross section; or
(4) Contains any other recognized serious safety or health hazard.
As mentioned above, employers must take steps to protect workers only if they work in a permit space. In addition, they must take effective steps to prevent workers they control from entering the space unless the workers are authorized to enter. Chapter 5 describes how to decide whether a confined space meets any of the four criteria for a permit space.
CHAPTER 2
Work Covered by the Standard
The Confined Spaces standard applies to construction work performed in confined spaces, except for certain construction activities that are subject to confined space provisions in other OSHA construction standards. The activities excluded from this standard are:
- Diving – regulated by 29 CFR Part 1926 subpart Y.
- Excavations – regulated by 29 CFR Part 1926 subpart P.
- Underground Construction, Caissons, Cofferdams and Compressed Air – regulated by 29 CFR Part 1926 subpart S.
Note, however, that employers engaged in these activities must comply with this standard if their workers are exposed to confined space hazards that are not addressed by the standards listed above. For example, the Excavation standard (subpart P) protects workers in a trench (a type of confined space) against the hazards associated with the trench itself. However, the Excavation standard would not protect workers inside a sewer line that is installed in an open trench from confined space hazards associated with the sewer line. The employer must comply with the Excavation standard to protect workers in the trench and with the Confined Spaces standard to protect workers in the sewer line.
Employers engaged in the following activities in confined spaces must also comply with other applicable OSHA standards, such as:
- Process Safety Management: 29 CFR § 1926.64.
- Hazardous Waste Operations: 29 CFR § 1926.65.
- Welding and Cutting: 29 CFR § 1926 Subpart J.
CHAPTER 3
Employer Responsibilities
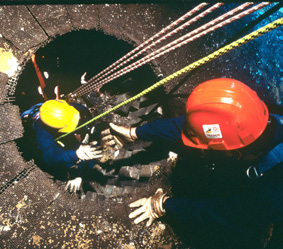
Photo: NIOSH
All employers engaged in construction work must (1) identify any confined spaces in which their workers will be working, and (2) determine whether any such spaces are permit spaces. When workers work in permit spaces, they must be protected against the hazards in those spaces. To ensure such protection, the Confined Spaces standard imposes duties on “entry employers,” “host employers,” and “controlling contractors.” If an employer knows that a permit space is present at its worksite, it must inform its workers of the location and danger posed by each space. It may do this by making sure that warning signs are posted. In addition, where an employer’s workers have no work to do in the space, that employer must ensure that its workers stay out. One way to do this is for employers to make sure that workers recognize permit space warning signs and understand their significance.
Important Definitions
An entry employer is an employer who decides that an employee it directs will enter a permit space. There may be more than one entry employer if the employees of multiple employers must enter the space. Each entry employer is responsible for complying with all provisions in the Confined Spaces standard except those specifically imposed on the controlling contractor and host employer.
A controlling contractor is the employer with overall responsibility for construction at the worksite. The controlling contractor is responsible for coordinating entry operations when there is more than one entry employer and when other activities on the site could foreseeably result in a hazard in the permit space. In addition, controlling contractors must provide any information they have about any permit space hazards and precautions previously used in the space.
A host employer is the employer that owns or manages the property where the construction work is taking place. Where the host employer has information about permit space hazards on the site, it must share that information with the controlling contractor, who is then responsible for sharing it with the other employers on the site.
In no case will there be more than one host employer. If the owner of the property on which the construction activity occurs has contracted with another employer to manage the property and provided any relevant information it has about permit spaces on the property to the managing entity, the managing entity is the host employer. Absent such a contract and exchange of information, the owner of the property is the host employer. If the controlling contractor owns or manages the property, it is both the controlling contractor and the host employer.
The following table summarizes the responsibilities of the various categories of employer.
Category of Employer | Employer Responsibilities |
---|---|
All Employers |
|
Entry Employers |
|
Controlling Contractors |
|
Host Employers |
|
CHAPTER 4
Overview of the Standard
This chapter contains an overview of the Confined Spaces standard’s requirements and identifies the chapters of this guide where more detailed information on specific topics can be found.
Employers must take the following steps to protect workers against confined space hazards.
- Have a competent person identify all confined spaces in which its employees may work.
- If confined spaces are present, the employer must have the competent person determine whether the confined spaces are “permit spaces.”
- If the workplace contains a permit space, the entry employer must protect its workers against the hazards in the permit space.
- The entry employer must train workers who work in a permit space.
- The entry employer must plan to rescue entrants who cannot exit the space under their own power.
A competent person is “one who is capable of identifying existing and predictable hazards in the surroundings or working conditions which are unsanitary, hazardous, or dangerous to employees, and who has the authority to take prompt corrective measures to eliminate them.” The competent person need not be an employee of any particular employer. The various contractors on a site may use a single individual to perform the duties required of a competent person.
A permit space has one or more of the following characteristics:
(1) contains or has the potential to contain a hazardous atmosphere;
(2) contains a material that has the potential for engulfing an entrant;
(3) has an internal configuration such that an entrant could be trapped or asphyxiated by inwardly converging walls or by a floor which slopes downward and tapers to a smaller cross section; or
(4) contains any other recognized serious safety or health hazard.
Chapter 5 describes how to determine whether a confined space is a permit space.
The protection that is required depends on the type and severity of the hazards present in the permit space. The following table lists the three categories of permit spaces for which different levels of protection are specified.
Characteristics of Space | Protective Action |
---|---|
Permit spaces that do not qualify for one of the following two exceptions. | If the employer’s workers will enter the space, develop and follow a written permit-required confined space program, or permit space program. The permit space program specifies, among other things, how the employer will (1) regulate worker entry into permit spaces; and (2) control permit space hazards. Chapter 6 describes the features that a permit space program must contain. All employers must inform their workers about the locations and dangers of each permit space (e.g., post signs), and take additional steps to ensure that workers do not enter permit spaces if they are not authorized to do so. |
Exception 1: Spaces that contain only physical (nonatmospheric) hazards. | If the physical hazards are eliminated or isolated so that they no longer present a hazard, the space may be reclassified as a non-permit space, with no further precautions required. See Chapter 7. |
Exception 2: Spaces containing an atmospheric hazard that can be controlled by continuous forced air ventilation. | As long as the atmospheric hazard is controlled by continuous forced air ventilation and any physical hazards are eliminated or isolated, the alternate procedures listed in Chapter 8 may be used instead of full permit space procedures, although the space is still classified as a permit space. |
Employers must identify (1) the worker(s) authorized to enter the space; (2) an attendant who must remain outside the space and monitor the workers within; and (3) an entry supervisor with overall responsibility for seeing that the program is followed. The duties of these workers are discussed in Chapter 9. All workers covered by the permit space program, including entrants, attendants, entry supervisors, and rescue workers, must be trained to have the knowledge and skills needed to recognize confined space hazards and protect themselves and their co-workers against permit space hazards. Chapter 10 describes the nature and extent of the training these workers must receive.
The entry employer must ensure that a worker who becomes sick or injured in a permit space can be rescued in a safe and timely manner. Its permit space program must specify whether the employer plans to use its own workers, a rescue team of another on-site employer, or an outside rescue service if the need for a rescue arises. The requirements for rescue and emergency services are addressed in Chapter 11.
CHAPTER 5
Identifying Permit Spaces
(Section 1203(a))
Identification of permit spaces is critical because it determines whether precautions are required before employees enter the space. Failure to take those precautions can result in death or serious injury to workers.
As discussed in Chapter 4, each employer engaged in construction work must ensure that a competent person identifies all confined spaces in which its workers may work on its worksite and evaluates each confined space to determine whether it is a permit-required confined space (permit space). The competent person must answer the following four questions to determine whether a confined space is a permit space. If the answer to one or more of the questions is “yes,” the space is a permit space.
- Does the space contain or have the potential to contain a hazardous atmosphere?
- Oxygen deficiency (concentration less than 19.5 percent) or excess (concentration above 23.5 percent).
- Concentration of any flammable gas, vapor, or mist in excess of 10 percent of its lower explosive limit:
- Airborne combustible dust at a concentration equal to or greater than its lower explosive limit.
- Atmospheric concentration of any substance that can cause death, incapacitation, impairment of ability to selfrescue, injury or acute illness.
Most deaths and injuries in confined spaces result from atmospheric hazards. Such hazards include insufficient oxygen and toxic or flammable chemicals. The competent person must evaluate, including testing as necessary, whether the following hazards are or may be present, before workers enter the space:
In evaluating atmospheric hazards, the competent person must consider (1) the hazards present in the space before any workers enter; and (2) whether the work that will be performed can introduce toxic, flammable, or combustible air contaminants or lead to an excess or deficiency of oxygen. To perform the second part of this evaluation, the competent person must be familiar with the work to be done in the space and the potential for that work to introduce atmospheric hazards. For example, a confined space that is safe when entered can become deadly if inert gas welding inside the space leads to the inert gas displacing oxygen in the worker’s breathing zone.
TOXIC CHEMICALS REGULATED BY OSHA: Subparts D and Z of Part 1926 list chemicals for which OSHA has established airborne permissible exposure limits (PELs). The presence in a confined space of a substance listed in Subpart D or TOXIC CHEMICALS REGULATED BY OSHA: Subparts D and Z of Part 1926 list chemicals for which OSHA has established airborne permissible exposure limits (PELs). The presence in a confined space of a substance listed in Subpart D or Subpart Z in a concentration exceeding a PEL does not necessarily require the space to be classified as a permit space. The space must only be classified as a permit space if the concentration of that substance can cause death, incapacitation, impairment of ability to self-rescue, injury, or acute illness. However, worker exposure exceeding a PEL would violate Subpart D or Z even if it does not violate the Confined Spaces standard.
The competent person must also evaluate chemicals for which no PEL is set by OSHA. For example, if a product’s label or the product manufacturer’s safety data sheet warns that a product is harmful if inhaled and should not be used without adequate ventilation, the competent person must evaluate whether use of that product in a confined space requires the space to be classified as a permit space.
OXYGEN-DEFICIENT SPACES: Asphyxiation due to insufficient oxygen is one of the leading causes of death during construction work in confined spaces. An oxygen-deficient atmosphere endangers both the workers assigned to enter the space and others who may attempt a rescue without proper equipment and training. Therefore, in evaluating a confined space to determine whether it is a permit space, particular consideration should be given to whether it contains or has the potential to contain an oxygen concentration of less than 19.5 percent. Any space that is to be entered after being isolated from the atmosphere for a period of time could be oxygen-deficient, and the oxygen concentration should be measured to determine whether the space must be classified as a permit space. Direct reading instruments that measure the concentration of oxygen in the air are available for this purpose. Such instruments must be properly calibrated and used to give reliable results.
- Does the space contain a material with the potential to engulf an entrant?
- Does the space have an internal configuration such that an entrant could be trapped by inwardly converging walls or by a floor that slopes downward and tapers to a smaller cross section?
An area of a confined space with a small cross section can develop a hazardous atmosphere if ventilation is inadequate. In addition, a space of this configuration could prevent an injured worker from escaping the space and add to the difficulty of rescuing the worker.
- Does the space contain any other recognized serious safety or health hazard(s) that pose an immediate danger to a worker’s life or health or would impair the worker’s ability to escape from the space in the event of injury?
Hazards that the competent person should consider include fire and explosion hazards, the presence of mechanical, electrical, hydraulic and pneumatic energy, temperature extremes, radiation, noise, corrosive chemicals, and biological hazards (such as venomous animals or insects).
If a workplace contains a permit space or spaces, the employer must inform workers in the vicinity of the location of the danger posed by each space. This can be done by posting warning signs like that to the right at each possible point of entry, or by other equally effective means.
In addition to posting warning signs, an employer who learns about a permit space must also notify its employees’ authorized representative and the controlling contractor of the location and danger of the space. The controlling contractor must then notify other employers on the site, whose activities could create a hazard in the permit space, of the presence and location of such spaces and the hazards associated with them before workers enter the space.
An employer whose workers will not be authorized to enter a permit space must take steps in addition to posting the warnings above, to prevent workers from entering the space. An employer might accomplish this by providing effective training on, and enforcement of, a work rule against entry.
If an employer’s workers will enter a permit space, the employer must develop a written permit space program, and entry is only permitted under the terms of the program. (Chapters 7 and 8, respectively, describe exceptions to the permit space program requirement for spaces where all physical hazards are eliminated or isolated and where any atmospheric hazards have been controlled by continuous forced air ventilation). That employer, who is an “entry employer” under the standard, must keep any unauthorized persons from entering the permit space, and remove any unauthorized persons who do enter the space.
Engulfment means the surrounding and effective capture of a person by a liquid or finely divided (flowable) solid substance that can be aspirated to cause death by filling or plugging the respiratory system or that can exert enough force on the body to cause death by strangulation, constriction, or crushing, or the substance suffocates the individual. The competent person must consider whether any liquid or flowable solid (such as sand) could enter the space. Any pipe or manhole in an operating water or sewer system in which a worker works is a confined space that could potentially engulf an entrant and must be treated as a permit space.
CHAPTER 6
Content of Permit Space Program
(Sections 1204-1206)
The permit space program must establish a system for preparing, using, and canceling entry permits, which are written or printed documents that allow and control entry into permit spaces. A permit space program must:
- Implement measures to prevent unauthorized entry;
- Identify and evaluate permit space hazards before allowing employee entry;
- Provide for the atmospheric conditions in the permit space to be tested before entry operations and for the space to be monitored during entry;
- Require appropriate testing for the following atmospheric hazards in this sequence: oxygen, combustible gases or vapors, and toxic gases or vapors;
- Establish and implement the means, procedures and practices to eliminate or control hazards necessary for safe permit space entry operations;
- Identify employee job duties;
- Provide and maintain, at no cost to the employee, personal protective equipment and any other equipment necessary for safe entry, and require employees to use the equipment properly;
- Ensure that at least one attendant is stationed outside the permit space during entry operations;
- Implement the procedures that any attendant who is required to monitor multiple spaces will follow during an emergency in one or more of those spaces;
- Coordinate entry operations (in consultation with the controlling contractor) when employees of more than one employer are working in the permit space; and
- Establish procedures for summoning rescue and emergency services and preventing unauthorized personnel from attempting rescue.
The employer must review the program and correct any deficiencies whenever it learns that the program may not be protecting employees adequately. Circumstances requiring such review include an injury or near-miss during entry, unauthorized entry, detection of a new hazard or a condition prohibited by the permit, or an employee complaint about the program’s effectiveness. In addition, the employer must annually review the program using the cancelled permits, and revise the program as necessary to ensure that employees are protected.
An example of a permit space program can be found in Appendix A of this guide.
With the exceptions discussed in Chapters 7 and 8, the permit space program must provide that entry is only permitted pursuant to a written entry permit. The permit must include:
- Name of the permit space to be entered, authorized entrant(s), current attendants, and current entry supervisors;
- Purpose of entry;
- Date and authorized duration of entry;
- Means of detecting an increase in atmospheric hazard levels;
- Name and signature of supervisor who authorizes entry;
- Known hazards in the space;
- Measures to be taken to isolate permit spaces and to eliminate or control space hazards;
- Acceptable entry conditions;
- Test results, date and time of test(s), and tester’s initials or signature;
- Name and telephone numbers of rescue and emergency services and means to be used to contact them;
- Communication procedures and equipment to maintain contact during entry;
- Special equipment and procedures, including personal protective equipment and alarm systems;
- Any other information needed to ensure employee safety; and
- Additional permits, such as for hot work, that have been issued authorizing work in the permit space.
The permit must be posted at the entrance to the space or be otherwise made available to authorized entrants and their authorized representatives at the time of entry. Appendix B of this guide contains a sample entry permit that includes the information required by the standard.
Canceling Entry Permits
The employer must make sure that the entry supervisor cancels entry permits when an assignment is completed or when new conditions exist. Once a permit is cancelled, entry under it is no longer permitted. New conditions must be noted on the canceled permit and used in revising the permit space program. The employer must keep all canceled entry permits for at least one year.
Suspending Entry Permits
An entry supervisor may suspend an entry permit instead of cancelling it if a temporary condition has occurred in or near the space that, once corrected, is not expected to reoccur. The permit may be reinstated and entry may occur under the permit if the entry supervisor has determined that the conditions in the space match the allowable conditions listed on the permit.
CHAPTER 7
Reclassifying a Permit Space as a Non-Permit Space (Section 1203(g))
A permit space that contains only physical hazards may be reclassified as a non-permit space if (1) the physical hazards are eliminated or isolated without entering the space; or (2) the physical hazards are eliminated or isolated by entering the space using permit space procedures. Physical hazards include all hazards that are not atmospheric hazards, including: explosives (other than explosive atmospheres); mechanical, electrical, hydraulic and pneumatic energy; radiation; temperature extremes; engulfment; noise; inwardly converging surfaces; and chemicals that can cause death or serious physical harm through skin or eye contact (rather than through inhalation).
Example: A confined space contains electrical machinery that presents mechanical and/or electric shock hazards. If the hazards presented by the machinery are eliminated by deenergizing and locking out the machinery at an electrical panel outside the space, the space can be reclassified as a non-permit space as long as the equipment remains deenergized and locked out. If it is necessary to enter the space to deenergize and lock out the machinery, the entry must be conducted pursuant to a full permit program. However, once the machinery is deenergized and locked out, the space may then be reclassified as a non-permit space.
Whenever a permit space is reclassified as a non-permit space, the entry employer must document the basis for determining that all hazards in the permit space have been eliminated, through a certification that contains the date, the location of the space, and the signature of the person making the determination. The certification must be made available to each worker entering the space or to that worker’s authorized representative.
If any hazards arise within a permit space that has been reclassified as a non-permit space, each worker in the space must exit the space. The entry employer must then reevaluate the space and determine how to proceed. If the new hazards are physical hazards that can be eliminated or isolated, the employer can reclassify the space as a non-permit space after that has been accomplished. If the new hazard is an atmospheric hazard that can be made safe for entry by continuous forced air ventilation, the employer can proceed in accordance with the procedures discussed in Chapter 8. In all other situations, further entry can only be made pursuant to a full permit space program.
CHAPTER 8
Alternate Procedures for Certain Permit Spaces — Section 1203(e))
Unlike a space that contains only physical hazards, a space containing an atmospheric hazard cannot be reclassified as a non-permit space. However, if the atmospheric hazard in a permit space can be controlled by forced air ventilation, the employer may use less stringent procedures instead of full permit space procedures when workers enter the space. The alternate procedures may be used if the employer can show that:
- All physical hazards are eliminated or isolated;
- The only hazard is an actual or potential hazardous atmosphere that can be and is made safe for entry using continuous forced air ventilation; and
- In the event the ventilation system stops working, entrants can exit the space safely.
An employer who uses the alternate procedures must document the reasons, and the supporting data, for concluding that these criteria are met. The documentation must be made available to each worker who enters the space or to that worker’s authorized representative.
The alternate procedures are as follows:
Entry and Exit
- Any conditions making it unsafe to remove an entrance cover must be eliminated before the cover is removed.
- When entrance covers are removed, the opening must be immediately guarded by a railing, temporary cover, or other temporary barrier that will prevent an accidental fall through the opening and that will protect each employee working in the space from foreign objects entering the space.
- Before a worker enters the space, the internal atmosphere must be tested, with calibrated direct-reading instruments, for oxygen content, for flammable gases and vapors, and for potential toxic air contaminants, in that order. The testing must demonstrate that the atmosphere in the space is not hazardous. Any worker who enters the space, or that worker’s authorized representative, must be provided an opportunity to observe the pre-entry testing.
- The employer must verify that the space is safe for entry and that the pre-entry measures discussed above have been taken, through a written certification that contains the date, the location of the space, and the signature of the person providing the certification. The certification must be made before entry and must be made available to each worker entering the space or to that worker’s authorized representative.
- The employer must provide workers with a safe method of entering and exiting the space. Any hoisting system that is used must either (1) be designed and manufactured for personnel hoisting; or (2) be approved for personnel hoisting by a registered professional engineer prior to use.
Ventilation Requirements
- Continuous forced air ventilation must be used. (Exhaust ventilation is not an acceptable substitute for forced air ventilation.)
- If the forced air ventilation stops for any reason, the entrant(s) must immediately leave the space.
- The forced air ventilation must be directed to ventilate the immediate areas where each entrant is or will be located within the space and must continue until all employees have left the space.
- The air supply for the forced air ventilation must be from a clean source and must not increase the hazards in the space.
During Entry
- The atmosphere within the space must be monitored to ensure that the forced air ventilation is preventing the accumulation of a hazardous atmosphere. Monitoring must be conducted continuously unless the entry employer can demonstrate that equipment for continuous monitoring is not commercially available or that periodic monitoring is sufficient to ensure that the atmosphere remains nonhazardous. Employers must provide any worker who enters the space, or that worker’s authorized representative, with an opportunity to observe the testing required by this paragraph.
- If a hazard is detected during entry: (A) Employers must make sure each worker leaves the space immediately; (B) The space must be evaluated to determine how the hazard developed; and (C) The employer must implement measures to protect workers from the hazard before any subsequent entry takes place.
The following table compares the requirements for spaces where permits are required and for spaces where alternate procedures are permitted.
Precautions Required | Permit-Required Space | Alternate Procedures Space |
---|---|---|
Written Permit Space Program Meeting Requirements of Sections 1926.1204-1206 | Yes | No |
Worker Training Meeting Section 1926.1207 | Yes | Yes |
Duties of Authorized Attendants (Section 1926.1208), Attendants (Section 1926.1209), and Entry Supervisors (Section 1926.1210) | Yes | No |
Rescue and Emergency Services (Section 1926.1211) | Yes | No |
Information exchange between controlling contractor and entry employer(s) (Section 1926.1203(h)) | Yes | Yes |
Permit Space Warning Signs and Entry Restrictions (Sections 1926.1203(b) and (c)) | Yes | Yes |
CHAPTER 9
Entrants, Attendants, and Entry Supervisors (Sections 1208-1210)
Three categories of workers have specific duties whenever work is performed in a permit space: authorized entrants; attendants, and entry supervisors. The entry employer is responsible for ensuring that these workers carry out those duties.
- An authorized entrant is a worker who is authorized by the entry supervisor to enter a permit space.
- An attendant is an individual stationed outside one or more permit spaces who monitors conditions within the space(s) and prevents unauthorized entry.
- An entry supervisor is a qualified person (such as the employer, foreman, or crew chief) responsible for overseeing entry operations. An entry supervisor also may serve as an attendant or as an authorized entrant, as long as that person is trained and equipped as required by this standard for each role he or she fills. The duties of entry supervisor may be passed from one individual to another during the course of an entry operation.
Authorized entrants must:
- Know space hazards, including information on the means of exposure such as inhalation or skin contact, and symptoms of the exposure;
- Use appropriate personal protective equipment properly;
- Stay in communication with attendants as necessary to enable the attendants to monitor the entrant’s status and alert the entrant to evacuate when necessary;
- Exit from the permit space as soon as possible when:
(1) Ordered by the attendant or entry supervisor;
(2) He or she recognizes the warning signs or symptoms of exposure;
(3) A prohibited condition exists; or
(4) An automatic alarm is activated. - Alert the attendant when a prohibited condition exists or when warning signs or symptoms of exposure exist.
The attendant must:
- Remain outside the permit space during entry operations unless relieved by another authorized attendant;
- Perform non-entry rescues when specified by the employer’s rescue procedure;
- Know existing and potential hazards, including information on the mode of exposure, and signs or symptoms, and consequences, and possible behavioral effects of exposure;
- Maintain communication with and keep an accurate account of those workers entering the permit space;
- Assess conditions inside and outside the space and order evacuation of the permit space when:
(1) A prohibited condition exists;
(2) A worker shows behavioral effects of hazard exposure;
(3) A situation exists outside the confined space that could endanger entrants; or
(4) The attendant cannot effectively and safely perform required duties. - Summon rescue and other services during an emergency;
- Ensure that unauthorized people stay away from permit spaces or exit immediately if they have entered the permit space;
- Inform authorized entrants and the entry supervisor if any unauthorized person enters the permit space; and
- Perform no other duties that interfere with the attendant’s primary duties.
Entry supervisors must:
- Know space hazards including information on the mode of exposure, signs or symptoms and consequences;
- Verify that specified entry conditions are satisfied, including permits, tests, procedures and equipment before allowing entry;
- Terminate entry and cancel or suspend permits when entry operations are completed or if a condition that is not allowed under the permit arises;
- Verify that rescue services are available and that the means for summoning them are operable;
- Take appropriate measures to remove unauthorized entrants; and
- Ensure that entry operations remain consistent with the entry permit and that acceptable entry conditions are maintained.
CHAPTER 10
Worker Training (Section 1207)
Before any worker works in a permit space, the entry employer must train authorized entrants, attendants, entry supervisors, and other employees with duties under the standard (such as persons who test and monitor the atmosphere in a permit space) to understand the hazards in the permit space and the methods used to protect against those hazards. If a worker is not authorized to perform entry rescues, the training must include the dangers of attempting such rescues. All training must be provided at no cost to workers. After the training, the employer must ensure that the workers have the understanding, knowledge and skills necessary to safely perform their assigned duties.
The required training must be provided:
- In both a language and vocabulary that the worker can understand;
- Before the worker is first assigned duties under this standard and before there is a change in the worker’s assigned duties;
- Whenever there is a change in permit space entry operations that presents a new hazard about which the worker has not previously been trained;
- Whenever the worker’s actions show inadequacies in the worker’s knowledge or use of entry procedures.
As discussed below in chapter 11, rescue personnel must also be trained to perform their duties.
The employer must keep a record showing that the required worker training has been completed. The record must contain the worker’s name, the trainer’s signature or initials and the dates of the training. The employer must make the record available for inspection by workers and their authorized representatives.
CHAPTER 11
Rescue and Emergency Services (Section 1211)
Effective emergency planning is vital to ensure that any entrant who becomes sick or is injured in a permit space can be evacuated quickly and safely. The entry employer’s permit space program must therefore include procedures for entrants to be rescued in a timely manner by qualified personnel.
Role of the attendant: Whenever an entrant is in a permit space, there must be an attendant outside the space who must maintain communication with all entrants and keep track of their condition. If one or more entrants suffers an injury or illness and is unable to exit the space without help, the attendant must initiate a rescue.
Non-entry rescue: It is preferable if the entrant(s) can be rescued without others entering the space to avoid having additional personnel exposed to the hazard that caused the injury or illness. Therefore, the employer’s rescue procedures must provide for non-entry rescue using retrieval equipment unless the retrieval equipment would increase the overall risk of entry or would not contribute to the rescue of the entrant, such as when obstructions can snag the retrieval line or the line can become entangled with air lines or electric cords. The attendant must be prepared to perform non-entry rescues when required by the employer’s rescue procedures.
When the rescue procedures provide for non-entry rescue, each entrant must wear a chest or full body harness, with a retrieval line attached at the D-ring in the center of the back or another point which positions the entrant so that he or she is small enough to be pulled out of the space. The other end of the retrieval line must be attached to a mechanical device or a fixed point outside the permit space. A mechanical device must be available to retrieve someone from vertical type permit spaces more than five feet deep.
Wristlets or anklets may be used instead of a chest or full body harness only if the employer can demonstrate that use of a chest or full body harness if infeasible or would create a greater hazard and that the use of wristlets or anklets is the safest and most effective alternative.
When non-entry rescue is selected, the entry employer must also confirm, before entry begins, that emergency assistance would be available if the non-entry rescue fails. Emergency assistance would usually be provided by a local fire department or similar service.
Entry rescue: Non-entry rescue might not be feasible. If so, the only way to rescue the entrant is for others to enter the permit space.
For entry rescue, the employer may plan to use an on-site rescue team (consisting of its own or another contractor’s employees) or an off-site team, such as a local fire department or other rescue service. In either case, the employer must make sure that the rescue service is able to respond in time to enable the injured worker to receive needed medical attention in light of the hazards present in the permit space by contacting the rescue service prior to entry and informing them of the nature of the space and the hazards involved. In some cases, this may require a standby rescue team, such as when the entrant is working in an atmosphere that is immediately dangerous to life or health and is wearing an airline respirator or a self-contained breathing apparatus.
Whenever entry rescue takes place, an attendant must be stationed outside the permit space so that additional help can be summoned if needed. If the original attendant is to enter the space as part of the rescue team, a new attendant must be in position before the first attendant enters the space.
Rescue and emergency services: The employer of the members of the designated rescue team (whether entry or non-entry) must ensure that the team members have received the training required for authorized entrants and have also been trained to perform their assigned rescue duties. That employer must provide the rescue team members with personal protective and rescue equipment, including respirators, and must train them on how to use it. All rescuers must be trained in first aid and CPR. At a minimum, one rescue team member must be currently certified in first aid and CPR. Employers must ensure that the team practices or performs rescue exercises at least yearly and that rescue services are provided access to permit spaces so they can practice rescue operations. Rescuers also must be informed of the hazards of the permit space before they enter the space. The rescue service must agree to notify the employer in the event the service becomes unavailable, and the employer must provide the service with access to the permit space so the service can develop an appropriate rescue plan and practice rescue as necessary.
If the entry employer designates an off-site rescue service, it must determine that the service has the ability and equipment to carry out a rescue in the particular permit space or type of permit space in which the entrant is working. It must contact the rescue service and make sure that it will be able to respond in a timely manner whenever an entrant is in the permit space.
CHAPTER 12
Sewer System Entry
Sewer systems present one of the most common and dangerous type of confined space. Numerous workers have suffered fatal and other serious injuries from confined space hazards in sewer manholes, pipes, and lift stations. This section is designed to help inform employers engaged in sewer work of what they must do to protect their workers.
Sewer entry differs in three vital respects from other permit entries; first, there rarely exists any way to completely isolate the space (a section of a continuous system) to be entered; second, because isolation of the space is not complete, the atmosphere may suddenly and unpredictably become lethally hazardous (toxic, flammable or explosive) from causes beyond the control of the entrant or employer; and third, material flowing through the sewer system may engulf entrants. However, experienced sewer workers are especially knowledgeable about entry and work in their permit spaces because of their frequent entries. Unlike other employments where permit space entry is a rare and exceptional event, sewer workers’ usual work environment is a permit space.
OSHA believes that if employers reinforce and follow the four procedures below that the risks of sewer work can be controlled and employees protected from the many unpredictable hazards of sewers.
(1) Adherence to procedure. Designate as entrants only employees who are thoroughly trained in the employer’s sewer entry procedures and who demonstrate that they follow these entry procedures exactly as prescribed when performing sewer entries.
(2) Atmospheric monitoring. Train entrants in the use of, and equip entrants with, atmospheric monitoring equipment which sounds an audible alarm, in addition to its visual readout. Sewer conditions to be monitored will often include oxygen concentration less than 19.5 percent or above 23.5 percent; flammable gas or vapor at 10 percent or more of the lower flammable limit (LFL); or hydrogen sulfide or carbon monoxide at or above 10 ppm or 35 ppm, respectively, measured as an 8-hour time-weighted average. Atmospheric monitoring equipment needs to be calibrated according to the manufacturer’s instructions. The oxygen sensor/broad range sensor is best suited for initial use in situations where the actual or potential contaminants have not been identified, because broad range sensors, unlike substance-specific sensors, enable employers to obtain an overall reading of the hydrocarbons (flammables) present in the space. However, such sensors only indicate that a hazardous threshold of a class of chemicals has been exceeded. They do not measure the levels of contamination of specific substances. Therefore, substance-specific devices, which measure the actual levels of specific substances, are best suited for use where actual or potential contaminants have been identified. The measurements obtained with substance-specific devices are of vital importance to the employer when decisions are made concerning the measures necessary to protect entrants (such as ventilation or personal protective equipment) and the setting and attainment of appropriate entry conditions. However, the sewer environment may suddenly and unpredictably change, and the substance-specific devices may not detect the potentially lethal atmospheric hazards which may enter the sewer environment.
Although OSHA considers the information and guidance provided above to be appropriate and useful in most sewer entry situations, the agency emphasizes that each employer must consider the unique circumstances, including the predictability of the atmosphere, of the sewer permit spaces in the employer’s workplace in preparing for entry. Only the employer can decide, based upon his or her knowledge of, and experience with permit spaces in sewer systems, what the best type of monitoring equipment may be for any specific entry operation.
The entrant must use the selected monitoring equipment in sewer line work to monitor the atmosphere in the entrant’s environment, and in advance of the entrant’s direction of movement, to warn the entrant of any deterioration in atmospheric conditions. Where several entrants are working together in the same immediate location, one instrument, used by the lead entrant, is acceptable.
(3) Surge flow and flooding. Develop and maintain liaison, to the extent possible, between the sewer crew and the local weather bureau and the fire and emergency services in the area so that sewer work may be delayed or interrupted and entrants withdrawn whenever sewer lines might be suddenly flooded by rain or fire suppression activities, or whenever flammable or other hazardous materials are released into sewers during emergencies due to industrial or transportation accidents. In addition, train workers in the use of, and make sure that they use, an early-warning system placed sufficiently far upstream of the work area to provide crews with enough notice of a surge to exit the space safely.
(4) Special equipment. Entry into large bore sewers may require the use of special equipment. Such equipment might include such items as self-contained breathing apparatus (SCBA) with at least a 10-minute air supply (or other NIOSHapproved self-rescuer), and waterproof flashlights, and may also include boats and rafts, radios and rope stand-offs for pulling around bends and corners as needed.
CHAPTER 13
Additional Information
Where other information can be found.
OSHA’s website contains other information that will help employers comply with the standard (www.osha.gov/ confinedspaces), including fact sheets and FAQs developed for the construction rule. The standard for construction work is similar to the standard regulating confined spaces in general industry (29 CFR § 1910.146), and information on OSHA’s website addressing the General Industry standard will therefore be useful in complying with the Construction standard. In particular, OSHA’s Confined Spaces Advisor for the General Industry standard (www.dol.gov/elaws/confined.htm) offers a computer-based, step-by-step guide to compliance as well as explanations of key terms used in the standard. The website also lists publications that can be ordered from the OSHA Publications Office.
Consultation services.
OSHA’s On-site Consultation Program offers free and confidential safety and health compliance assistance to small and medium-sized businesses in all states across the country, with priority given to high-hazard worksites. On-site Consultation services are separate from enforcement and do not result in penalties or citations. Consultants from state agencies and universities work with employers to identify workplace hazards, provide advice on compliance with OSHA standards, and help establish and improve their safety and health management systems. To find the OSHA On-site Consultation Program office nearest you, go to: www.osha.gov/ dcsp/smallbusiness/consult_directory.html.
State plans.
There are 26 states and 2 U.S. territories that have their own OSHA-approved occupational safety and health programs called state plans. The following 22 states or territories operate state plans that cover both private sector and state and local government employers: Alaska, Arizona, California, Hawaii, Indiana, Iowa, Kentucky, Maryland, Michigan, Minnesota, Nevada, New Mexico, North Carolina, Oregon, Puerto Rico, South Carolina, Tennessee, Utah, Vermont, Virginia, Washington and Wyoming. Five additional states and one U.S. territory operate state plans that cover private sector workers only: Connecticut, Illinois, Maine, New Jersey, New York, and the Virgin Islands.
State plans have and enforce their own occupational safety and health standards that are required to be at least as effective as OSHA’s, but may have different or additional provisions. Therefore, state plans must adopt a standard for confined spaces in construction that is at least as effective as OSHA’s standard. If you are operating a business in one of the abovelisted states, you should contact your state plan to determine whether any additional requirements apply. A list of the state plans and more information is available at: www.osha.gov/ dcsp/osp.
APPENDIX A
Example of a Permit-Required Confined Space Program
Workplace. Sewer entry.
Potential hazards. The employees could be exposed to the following:
Engulfment.
Presence of toxic gases. Equal to or more than 10 ppm hydrogen sulfide measured as an 8-hour time-weighted average, and equal to or more than 35 ppm carbon monoxide measured as an 8-hour time-weighted average. If the presence of other toxic contaminants is suspected, specific monitoring programs will be developed.
Presence of explosive/flammable gases. Equal to or greater than 10% of the lower flammable limit (LFL).
Oxygen deficiency. A concentration of oxygen in the atmosphere equal to or less than 19.5% by volume.
A. Entry Without Permit/Attendant
Certification. Confined spaces may be entered without the need for a written permit or an attendant provided that the space can be maintained in a safe condition for entry by mechanical ventilation alone, as provided in §1926.1203(e). All spaces must be considered permit-required confined spaces until the pre-entry procedures demonstrate otherwise. Any employee required or permitted to pre-check or enter an enclosed/confined space must have successfully completed, at a minimum, the training as required by the following sections of these procedures. A written copy of operating and rescue procedures as required by these procedures must be at the work site for the duration of the job. The Confined Space Pre-Entry Check List must be completed by the LEAD WORKER before entry into a confined space. This list verifies completion of the items listed below. This checklist must be kept at the job site for the duration of the job. If circumstances dictate an interruption in the work, the permit space must be re-evaluated and a new checklist must be completed.
Control of atmospheric and engulfment hazards.
Pumps and lines. All pumps and lines which may reasonably cause contaminants to flow into the space must be disconnected, blinded and locked out, or effectively isolated by other means to prevent development of dangerous air contamination or engulfment. Not all laterals to sewers or storm drains require blocking. However, where experience or knowledge of industrial use indicates that there is a reasonable potential for contamination of air or engulfment into an occupied sewer, then all affected laterals must be blocked. If blocking and/or isolation requires entry into the space the provisions for entry into a permit-required confined space must be implemented.
Surveillance. The surrounding area must be surveyed to avoid hazards such as drifting vapors from the tanks, piping, or sewers.
Testing. The atmosphere within the space will be tested to determine whether dangerous air contamination and/ or oxygen deficiency exists. Detector tubes, alarm-only gas monitors and explosion meters are examples of monitoring equipment that may be used to test permit space atmospheres. Testing must be performed by the LEAD WORKER who has successfully completed the Gas Detector training for the monitor he or she will use. The minimum parameters to be tested are oxygen deficiency, LFL, and hydrogen sulfide and carbon monoxide concentrations. A written record of the pre-entry test results must be made and kept at the work site for the duration of the job. The supervisor will certify in writing, based upon the results of the preentry testing, that all hazards have been eliminated. Affected employees must be able to review the testing results. The most hazardous conditions must govern when work is being performed in two adjoining, connecting spaces.
Entry Procedures. If there are no non-atmospheric hazards present and if the pre-entry tests show there is no dangerous air contamination and/or oxygen deficiency within the space and there is no reason to believe that any is likely to develop, entry into and work within may proceed. Continuous monitoring of the atmosphere in the immediate vicinity of the workers within the space must be accomplished. The workers will immediately leave the permit space when any of the gas monitor alarm set points are reached as defined. Workers will not return to the area until a SUPERVISOR who has completed the gas detector training has used a direct reading gas detector to evaluate the situation and has determined that it is safe to enter.
Rescue. Arrangements for rescue services are not required where there is no attendant. See the rescue portion of section B., below, for instructions regarding rescue planning where an entry permit is required.
B. Entry Permit Required
Confined Space Entry Permit. All spaces must be considered permit-required confined spaces until the preentry procedures demonstrate otherwise. Any employee required or permitted to pre-check or enter a permit-required confined space must have successfully completed, at a minimum, the training as required by the following sections of these procedures. A written copy of operating and rescue procedures as required by these procedures must be at the work site for the duration of the job. The Confined Space Entry Permit must be completed before approval can be given to enter a permit-required confined space. This permit verifies completion of the items listed below. This permit must be kept at the job site for the duration of the job. If circumstances cause an interruption in the work or a change in the alarm conditions for which entry was approved, a new Confined Space Entry Permit must be completed.
Control of atmospheric and engulfment hazards.
Surveillance. The surrounding area must be surveyed to avoid hazards such as drifting vapors from tanks, piping or sewers.
Testing. The confined space atmosphere must be tested prior to entry to determine whether dangerous air contamination and/or oxygen deficiency exists. A direct reading gas monitor must be used. Initial testing must be performed by the SUPERVISOR who has successfully completed the gas detector training for the monitor he will use. The minimum parameters to be tested are oxygen deficiency, LFL, hydrogen sulfide concentration and carbon monoxide concentration. A written record of the preentry test results must be made and kept at the work site for the duration of the job. Affected employees and their representatives must be able to review the results. The most hazardous conditions must govern when work is being performed in two adjoining, connected spaces.
Space Ventilation. Mechanical ventilation systems, where applicable, must be set at 100% outside air. Where possible, open additional manholes to increase air circulation. Use portable blowers to augment natural circulation if needed. After a suitable ventilating period, repeat the testing. Entry may not begin until testing has demonstrated that the hazardous atmosphere has been eliminated.
Early-warning system. Whenever the possibility of engulfment is present at the work site, an employee must be stationed far enough upstream with a two-way radio to alert entrants at the first sign of an approaching flood hazard, or an alarm activated by remote detector(s) placed to detect an approaching flood hazard must be used, so the entrants have time to exit the space safely.
Entry Procedures. The following procedure must be observed under any of the following conditions: (1) Testing demonstrates the existence of dangerous or deficient conditions and additional ventilation cannot reduce concentrations to safe levels; (2) The atmosphere tests as safe but unsafe conditions can reasonably be expected to develop; (3) It is not feasible to provide for ready exit from spaces equipped with automatic fire suppression systems and it is not practical or safe to deactivate such systems; or (4) An emergency exists and it is not feasible to wait for preentry procedures to take effect.
All personnel must be trained. A self-contained breathing apparatus must be worn by any person entering the space. At least one worker must stand by the outside of the space ready to give assistance in case of emergency. The standby worker must have a self-contained breathing apparatus available for immediate use. There must be at least one additional worker within sight or call of the standby worker. Continuous powered communications must be maintained between the worker within the confined space and standby personnel.
If at any time there is any questionable action or nonmovement by the worker inside, a verbal check will be made. If there is no response, the worker will be moved immediately. Exception: If the worker is disabled due to falling or impact, he/she must not be removed from the confined space unless there is immediate danger to his/her life. Local emergency services must be notified immediately. The standby worker may only enter the confined space in case of an emergency (wearing the self-contained breathing apparatus) and only after being relieved by another worker. A safety belt or harness with an attached lifeline must be used by all workers entering the space with the free end of the line secured outside the entry opening. The standby worker must attempt to remove a disabled worker via his lifeline before entering the space.
When practical, these spaces must be entered through side openings—those within 3 1/2 feet (1.07 m) of the bottom. When entry must be through a top opening, the safety belt must be of the harness type that suspends a person upright and a hoisting device or similar apparatus must be available for lifting workers out of the space.
In any situation where their use may endanger the worker, use of a hoisting device or safety belt and attached lifeline may be discontinued. (See the rescue section below.)
When dangerous air contamination is attributable to flammable and/or explosive substances, lighting and electrical equipment must be Class 1, Division 1 rated as per National Electrical Code and no ignition sources must be introduced into the area.
Continuous gas monitoring must be performed during all confined space operations. The minimum parameters to be monitored are oxygen deficiency, LFL, hydrogen sulfide concentration and carbon monoxide concentration. If alarm conditions change adversely, entry personnel must exit the confined space and a new confined space permit issued.
Rescue. Use of harnesses, lifelines, and a winch outside the space is the preferred method of rescue. Entrants and attendants will be trained in proper use of harnesses and rescue equipment. If harnesses and lifelines may not be used due to the configuration of the space, or could expose workers to greater hazards than entry rescue, call the local emergency services (or other rescue service) and evaluate them for entry rescue capability, informing them of the nature and exact location of the space and the anticipated hazards within. Where immediate hazards to injured personnel are present, workers at the site must implement emergency procedures to fit the situation.
APPENDIX B
Sample Entry Permit
Entry Permit Pseudo Construction Co. |
||
---|---|---|
General Information | ||
Identity (e.g., location) of the space: 1500 K Street, northwest corner. | ||
Purpose of entry: Replace communication cable in sewer line. | ||
Duration of entry: First entry on January 22, 2007; complete work and terminate entry operations on January 26, 2007. | ||
Identify the physical hazards in the space: (1) Engulfment -- sewer water. (2) Electrical -- communication cables. |
||
Describe the methods for isolating or controlling the physical hazards, or used to protect authorized entrants: (1) Engulfment -- Disconnect and lockout all sewer-system overflow pumps, and disconnect, blind, and lockout, all water lines within 100 feet of the work area, including lateral lines. (2) Electrical -- de-energize, tag, and ground all communication cables in work area. Use heavy duty, insulated work gloves for handling cables and conduits. |
||
Identify the atmospheric hazards in the space (e.g., oxygen deficiency, flammable/explosive gases/vapors, others (including toxic particulates, gases, and vapors)): (1) Oxygen deficiency -- possibility that oxygen level may be less than 19.5%. (2) Flammable/explosive gases/vapors -- methane may be present. (3) Other -- hydrogen sulfide and/or carbon monoxide may be present. |
||
Describe the methods for isolating or controlling the atmospheric hazards, or used to protect authorized entrants: Space ventilation—mechanical ventilation systems set at 100% outside air. Where possible, open additional manholes to increase air circulation. Use portable blowers to augment natural ventilation if needed. Repeat atmospheric testing after ventilating the space for 10 minutes. |
||
Describe the determination made to show that if the ventilation system stops working, atmospheric hazards will remain at safe levels long enough for entrants to recognize the problem and safely exit the space: Fully ventilated the unoccupied space and got non-detect readings for methane and hydrogen sulfide. After securing the mechanical ventilation system, ports, and portable blowers, found that both methane and hydrogen sulfide reached maximum limits in two hours, which is well outside the 60-minute period used to monitor and record atmospherichazard values in the space. |
||
Planned Conditions | ||
Safe conditions and/or monitoring determined for physical hazards: (1) Water levels—pooling water level inside PRCS not to exceed 2 inches; survey PRCS every hour to assess pooling water level and seeping water from piping and sewer. (2) Electrical—visually confirm every hour that electrical cables remain disconnected and tagged. (3) Early-warning system―when alarm sounds, evacuate authorized employees immediately. |
||
Safe levels of atmospheric hazards: | ||
Hazard | Minimum limit | Maximum limit |
Oxygen | 19.50% | 23.00% |
Flammable gas/vapors (specify): (1) Methane |
0% LFL | 10% LFL |
Others (specify): (1) Hydrogen sulfide (2) Carbon monoxide |
0 ppm 0 ppm |
20 ppm 35 ppm |
Atmospheric-testing/-monitoring results: (see attachment) | ||
Personnel | ||
Current Entry Supervisor: Name: S. Smith |
Name: J. Jones |
Name: ___________ |
Signature/initial: /s/ | Signature/initial: /s/ | Signature/initial: |
Current Attendants: Name: J. James |
Name: B. Bills |
Name: ___________ |
Authorized entrants: Refer to daily tracking roster for names of authorized entrants. | ||
Identity of the rescue service: (Check one) x Non-entry rescue. Identity of the non-entry rescue service: the attendant ___ Entry rescue. Identity of the entry rescue service: |
||
Identity of the emergency service: Washington, DC Fire and Rescue Service, Station 1. Each attendant and entry supervisor has cell phone pre-programmed with DC Fire and Rescue Service emergency hotline number (e.g., 202-123-4567). | ||
Name and signature/initials of the entry supervisor who first verified this entry permit and authorized initial entry into this PRCS: | ||
Equipment | ||
Methods of communication between attendants and authorized entrants: Attendant and authorized entrants will use Type X walkie-talkies. | ||
Equipment Needed: (1) Lighting equipment: two explosion-proof and waterproof lights with 50-ft. extension cords. |
||
Other Information | ||
Information not documented elsewhere on this permit (see § 1926.1206(o): (1) Describe any condition making it unsafe to remove an entrance cover, and how the condition was eliminated: Determined that the entrance cover was vented, which eliminated the potential for hazardous pressure conditions to exist in the space. (2) Describe any actions taken to guard holes and openings into the space from falling individuals and objects: A portable guardrail system was erected around the entry point, in addition to placing warning cones to divert pedestrian traffic around the space. (3) Describe the method used for entering and exiting the space: a 16-foot fixed ladder. Additional information: |
||
Entry Permit Cancellation | ||
Reason for cancellation: Completed work in PRCS. | ||
Name and signature/initials of the individual who cancelled the entry permit: Name: J. Jones |
Workers' Rights
Workers have the right to:
- Working conditions that do not pose a risk of serious harm.
- Receive information and training (in a language and vocabulary the worker understands) about workplace hazards, methods to prevent them, and the OSHA standards that apply to their workplace.
- Review records of work-related injuries and illnesses.
- File a complaint asking OSHA to inspect their workplace if they believe there is a serious hazard or that their employer is not following OSHA’s rules. OSHA will keep all identities confidential.
- Exercise their rights under the law without retaliation, including reporting an injury or raising health and safety concerns with their employer or OSHA. If a worker has been retaliated against for using their rights, they must file a complaint with OSHA as soon as possible, but no later than 30 days.
For more information, see OSHA’s Workers page.
OSHA Assistance, Services and Programs
OSHA has a great deal of information to assist employers in complying with their responsibilities under OSHA law. Several OSHA programs and services can help employers identify and correct job hazards, as well as improve their injury and illness prevention program.
Establishing an Injury and Illness Prevention Program
The key to a safe and healthful work environment is a comprehensive injury and illness prevention program.
Injury and illness prevention programs are systems that can substantially reduce the number and severity of workplace injuries and illnesses, while reducing costs to employers.
Thousands of employers across the United States already manage safety using injury and illness prevention programs, and OSHA believes that all employers can and should do the same. Thirty-four states have requirements or voluntary guidelines for workplace injury and illness prevention programs. Most successful injury and illness prevention programs are based on a common set of key elements. These include management leadership, worker participation, hazard identification, hazard prevention and control, education and training, and program evaluation and improvement. Visit OSHA’s Injury and Illness Prevention Programs web page at www.osha.gov/dsg/topics/ safetyhealth for more information.
Compliance Assistance Specialists
OSHA has compliance assistance specialists throughout the nation located in most OSHA offices. Compliance assistance specialists can provide information to employers and workers about OSHA standards, short educational programs on specific hazards or OSHA rights and responsibilities, and information on additional compliance assistance resources. For more details, visit www.osha.gov/dcsp/compliance_assistance/cas.html or call 1-800-321-OSHA (6742) to contact your local OSHA office.
Free On-site Safety and Health Consultation Services for Small Business
OSHA’s On-site Consultation Program offers free and confidential advice to small and medium-sized businesses in all states across the country, with priority given to highhazard worksites. Each year, responding to requests from small employers looking to create or improve their safety and health management programs, OSHA’s On-site Consultation Program conducts over 29,000 visits to small business worksites covering over 1.5 million workers across the nation.
On-site consultation services are separate from enforcement and do not result in penalties or citations. Consultants from state agencies or universities work with employers to identify workplace hazards, provide advice on compliance with OSHA standards, and assist in establishing safety and health management programs.
For more information, to find the local On-site Consultation office in your state, or to request a brochure on Consultation Services, visit www.osha.gov/consultation, or call 1-800-321-OSHA (6742).
Under the consultation program, certain exemplary employers may request participation in OSHA’s Safety and Health Achievement Recognition Program (SHARP). Eligibility for participation includes, but is not limited to, receiving a fullservice, comprehensive consultation visit, correcting all identified hazards and developing an effective safety and health management program. Worksites that receive SHARP recognition are exempt from programmed inspections during the period that the SHARP certification is valid.
Cooperative Programs
OSHA offers cooperative programs under which businesses, labor groups and other organizations can work cooperatively with OSHA. To find out more about any of the following programs, visit www.osha.gov/cooperativeprograms.
Strategic Partnerships and Alliances
The OSHA Strategic Partnerships (OSP) provide the opportunity for OSHA to partner with employers, workers, professional or trade associations, labor organizations, and/or other interested stakeholders. OSHA Partnerships are formalized through unique agreements designed to encourage, assist, and recognize partner efforts to eliminate serious hazards and achieve model workplace safety and health practices. Through the Alliance Program, OSHA works with groups committed to worker safety and health to prevent workplace fatalities, injuries and illnesses by developing compliance assistance tools and resources to share with workers and employers, and educate workers and employers about their rights and responsibilities.
Voluntary Protection Programs (VPP)
The VPP recognize employers and workers in private industry and federal agencies who have implemented effective safety and health management programs and maintain injury and illness rates below the national average for their respective industries. In VPP, management, labor, and OSHA work cooperatively and proactively to prevent fatalities, injuries, and illnesses through a system focused on: hazard prevention and control, worksite analysis, training, and management commitment and worker involvement.
Occupational Safety and Health Training
The OSHA Training Institute partners with 27 OSHA Training Institute Education Centers at 42 locations throughout the United States to deliver courses on OSHA standards and occupational safety and health topics to thousands of students a year. For more information on training courses, visit www.osha.gov/otiec.
OSHA Educational Materials
OSHA has many types of educational materials in English, Spanish, Vietnamese and other languages available in print or online. These include:
- Brochures/booklets;
- Fact Sheets;
- Guidance documents that provide detailed examinations of specific safety and health issues;
- Online Safety and Health Topics pages;
- Posters;
- Small, laminated QuickCards™ that provide brief safety and health information; and
- QuickTakes, OSHA’s free, twice-monthly online newsletter with the latest news about OSHA initiatives and products to assist employers and workers in finding and preventing workplace hazards. To sign up for QuickTakes visit www. osha.gov/quicktakes.
To view materials available online or for a listing of free publications, visit www.osha.gov/publications. You can also call 1-800-321-OSHA (6742) to order publications.
Select OSHA publications are available in e-Book format. OSHA e-Books are designed to increase readability on smartphones, tablets and other mobile devices. For access, go to www. osha.gov/ebooks.
OSHA’s web site also has information on job hazards and injury and illness prevention for employers and workers. To learn more about OSHA’s safety and health resources online, visit www.osha.gov or www.osha.gov/html/a-z-index.html.
NIOSH Health Hazard Evaluation Program
Getting Help with Health Hazards
The National Institute for Occupational Safety and Health (NIOSH) is a federal agency that conducts scientific and medical research on workers’ safety and health. At no cost to employers or workers, NIOSH can help identify health hazards and recommend ways to reduce or eliminate those hazards in the workplace through its Health Hazard Evaluation (HHE) Program.
Workers, union representatives and employers can request a NIOSH HHE. An HHE is often requested when there is a higher than expected rate of a disease or injury in a group of workers. These situations may be the result of an unknown cause, a new hazard, or a mixture of sources. To request a NIOSH Health Hazard Evaluation go to www.cdc.gov/niosh/hhe/request.html. To find out more, in English or Spanish, about the Health Hazard Evaluation Program:
E-mail HHERequestHelp@cdc.gov or call 800-CDC-INFO (800-232-4636).
OSHA Regional Offices
Region I
Boston Regional Office
(CT*, ME*, MA, NH, RI, VT*)
JFK Federal Building, Room E340
Boston, MA 02203
(617) 565-9860
(617) 565-9827 Fax
Region II
New York Regional Office
(NJ*, NY*, PR*, VI*)
201 Varick Street, Room 670
New York, NY 10014
(212) 337-2378
(212) 337-2371 Fax
Region III
Philadelphia Regional Office
(DE, DC, MD*, PA, VA*, WV)
The Curtis Center
170 S. Independence Mall West Suite 740
West Philadelphia, PA 19106-3309
(215) 861-4900
(215) 861-4904 Fax
Region IV
Atlanta Regional Office
(AL, FL, GA, KY*, MS, NC*, SC*, TN*)
61 Forsyth Street, SW, Room
6T50
Atlanta, GA 30303
(678) 237-0400
(678) 237-0447 Fax
Region V
Chicago Regional Office
(IL*, IN*, MI*, MN*, OH, WI)
230 South Dearborn Street Room
3244
Chicago, IL 60604
(312) 353-2220
(312) 353-7774 Fax
Region VI
Dallas Regional Office
(AR, LA, NM*, OK, TX)
525 Griffin Street, Room 602
Dallas, TX 75202
(972) 850-4145
(972) 850-4149
Fax (972) 850-4150 FSO Fax
Region VII
Kansas City
Regional Office
(IA*, KS, MO, NE)
Two Pershing Square Building
2300 Main Street, Suite 1010
Kansas City, MO 64108-2416
(816) 283-8745
(816) 283-0547 Fax
Region VIII
Denver Regional Office
(CO, MT, ND, SD, UT*, WY*)
Cesar Chavez Memorial Building
1244 Speer Boulevard, Suite 551
Denver, CO 80204
(720) 264-6550
(720) 264-6585 Fax
Region IX
San Francisco Regional Office
(AZ*, CA*, HI*, NV*, and American Samoa, Guam and the Northern Mariana Islands)
90 7th Street, Suite 18100
San Francisco, CA 94103
(415) 625-2547
(415) 625-2534 Fax
Region X
Seattle Regional Office (AK*, ID, OR*, WA*)
300 Fifth Avenue, Suite 1280
Seattle, WA 98104
(206) 757-6700
(206) 757-6705 Fax
* These states and territories operate their own OSHA-approved job safety and health plans and cover state and local government employees as well as private sector employees. The Connecticut, Illinois, Maine, New Jersey, New York and Virgin Islands programs cover public employees only. (Private sector workers in these states are covered by Federal OSHA). States with approved programs must have standards that are identical to, or at least as effective as, the Federal OSHA standards.
Note: To get contact information for OSHA area offices, OSHAapproved state plans and OSHA consultation projects, please visit us online at www.osha.gov or call us at 1-800-321-OSHA (6742).
For questions or to get information or advice, to report an emergency, fatality, inpatient hospitalization, amputation, or loss of an eye, or to file a confidential complaint, contact your nearest OSHA office, visit www. osha.gov or call OSHA at 1-800-321-OSHA (6742), TTY 1-877-889-5627.
For assistance, contact us. We are OSHA. We can help.
www.osha.gov (800) 321-OSHA (6742)
U.S. Department of Labor
Occupational Safety and Health Act of 1970
“To assure safe and healthful working conditions for working men and women; by authorizing enforcement of the standards developed under the Act; by assisting and encouraging the States in their efforts to assure safe and healthful working conditions; by providing for research, information, education, and training in the field of occupational safety and health.” Material contained in this publication is in the public domain and may be reproduced, fully or partially, without permission. Source credit is requested but not required.
This information will be made available to sensory-impaired individuals upon request. Voice phone: (202) 693-1999; teletypewriter (TTY) number: 1-877-889-5627.
OSHA 3825-09 2015