Summary Statement
Presentation on introducing safety into building design,
including examples, procurement issues, case studies, training
and liability issues.
February 10-12, 2004
14th Annual Construction Safety & Health
Conference & ExpositionRosemont, IL
February 10-12, 2004
Presentation Overview
- Introduction to Safety in Design
- Choosing the right procurement method
- Getting trade contractors involved
- Example design for safety details
- Case study of a design for safety process p Liability issues
- Liability issues
- Education and training for architects and engineers
- Take aways
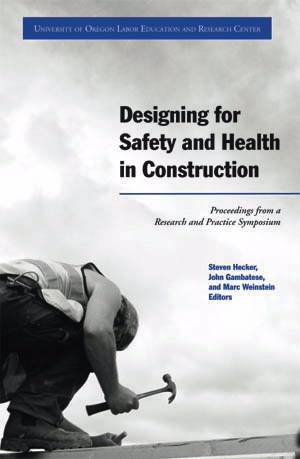
If you want further detail on the topics raised in this presentation, you might be interested in this book, available at https://millrace.uoregon.edu/uopress/index.cfm
What is Safety in Design?
- The consideration of worker safety in the design of a facility
- A focus on construction worker safety
- "Safety Constructability"
- Formal consideration of construction worker safety not a traditional aspect of design
- Design professionals traditionally focus on the safety of the "end-user", such as the building occupant, motorist, or facility operator.
What impacts a project's design?
Why has construction worker safety traditionally not been addressed in project designs?
- OSHA's placement of safety responsibility.
- Designer education and training.
- Lack of Safety in Design tools, guidelines, and procedures.
- Designer's limited role on the project team.
- Designer's traditional viewpoint on construction worker safety.
- Lack of understanding of the associated liability.
- Design influences construction means and methods
- European research: 60% of construction accidents could have been avoided or had their impact reduced by design alterations or other pre-construction measures
- Examples of designing in safety and health measures:
- Anchorage points for fall protection
- Parapet walls
- Substitution of less hazardous materials
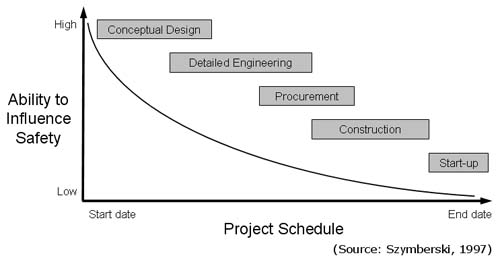
Loughborough University
Hierarchy of influences in construction accidents
Gibb et al. 2003
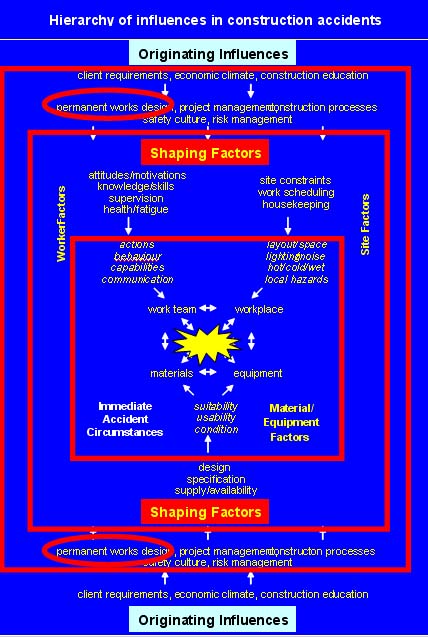
Beginnings of Change
- ASCE Policy Statement #350 on Construction Site Safety
- Subpart R - OSHA Steel Erection Rules
- EU Mobile Worksite Directive and UK Construction (Design and Management) Regulations
- Australian CHAIR process
- Construction Hazard Assessment Implication Review
(Gambatese et al., 2003, 2004)
- Study objective:
- To investigate designing for safety as a prospective intervention for improving the safety and health of construction workers.
- Viability considered to be related to:
- Feasibility and practicality of implementation
- Impact on safety and other project parameters
- Review of OSHA Standards for Construction
- Interviews with architects, engineers, attorneys, insurers, etc.
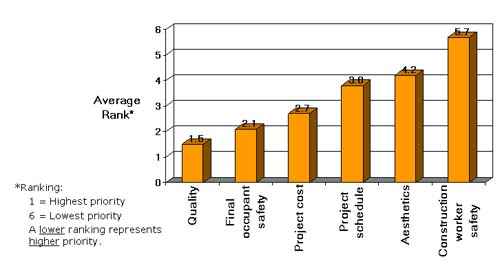
Analysis: Factors Affecting Implementation
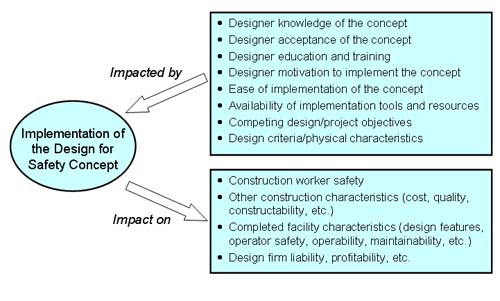
Viability of Designing for Safety
- Considered viable if:
- The factors that impact implementation on a project do not prohibit, or substantially limit, its implementation; and
- The outcomes of implementation are beneficial such that they provide sufficient motivation to implement the concept.
- Barriers:
- None cannot be overcome
- Impacts:
- Improved safety through reduced worker exposure to safety hazards
- Improved quality and productivity
- Lower cost over project lifecycle
- Designing for safety is a viable intervention.
- An obligation to provide for the safety of anyone impacted by their designs
1. A change in designer mindset toward safety.
2. A motivational force to promote designing for safety.
3. Designers knowledgeable of the concept.
4. Incorporation of construction safety knowledge in the design phase.
5. Designers knowledgeable about specific design for safety modifications.
6. Design for safety tools and guidelines available for use and reference.
7. Mitigation of designer liability exposure.
Choosing the Right Procurement Method
Design/Bid/Build and CM/GC Project Organizations
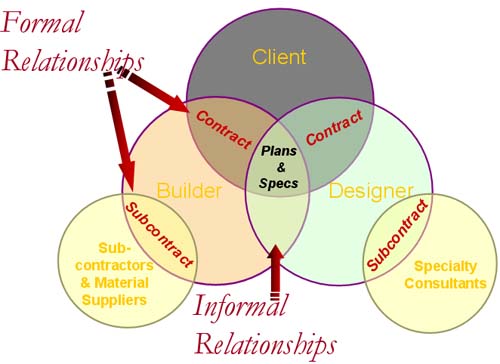
Design/Build Delivery Project Organization
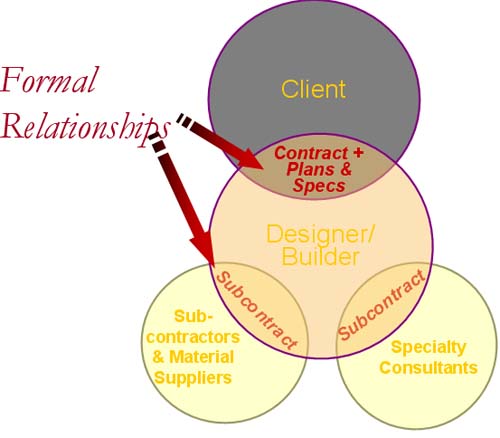
Design/Bid/Build Delivery Model
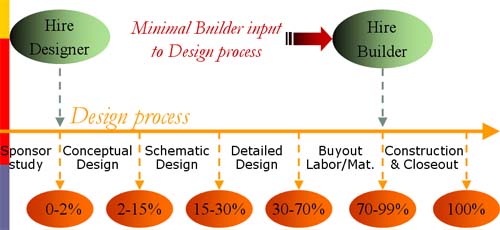
Design/Build Delivery Model
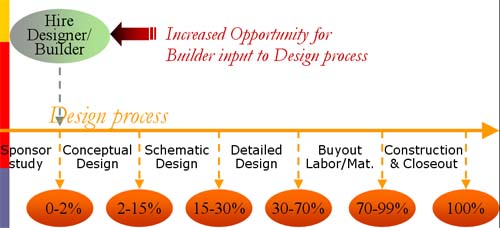
CM/GC Delivery Model

Integrating Construction Knowledge to Enhance Safety in Design (SID)
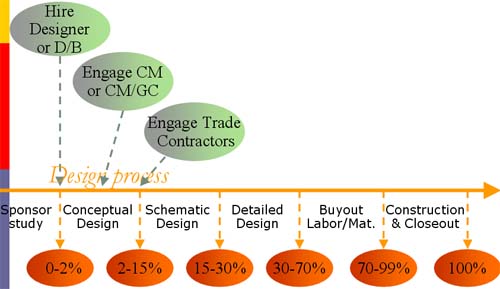
SiD is possible, even within "traditional" project delivery
- Procurement Process exists to Implement Project Delivery Strategy
- RFPs & Contract Language are Tools
- Pre-construction Services Contracts can overcome "traditional" Project Delivery Structure limitations using:
- CM or CM/GC
- Trade Contractors
Why...
- Trade contractors and their employees have unique expertise in construction and retrofit
- Benefits all parties involved through...
- Reduced redesign after "Issued For Construction"
- Reduced construction rework
- Improvement or elimination of potential exposures
- Formal documentation of comments and recommendations
- Ultimately a safer, more cost effective n project
- CM Role
- Constructability Evaluation
- Schedule
- Hazards introduced or mitigated
- Estimating
- Facilitating Trade Contractor Involvement
- Execution of Design
- Constructability Evaluation
What are the Best Practices? A CM Perspective
- Let owners know that you can bring construction knowledge & experience to the Design Phase
- Explore ways to collaborate with Trade Contractors
- Pay attention to relationships between & within the organizations on the project
Design for Safety Examples
- Design in tie-off points for attaching lanyards and other fall protection devices.
- Design floor perimeter beams and beams above floor openings to support lanyards.
- Design lanyard connection points along the beams.
- Note on the contract drawings which beams are designed to support lanyards, how many lanyards, and at what locations along the beams.
- Design permanent guardrails to be installed around skylights.
- Design domed, rather than flat, skylights with shatterproof glass or strengthening wires.
- Design the skylight to be installed on a raised curb.
- Design upper story windows to be at least 1.07 m (42 in.) above the floor level.
- The window sills act as guardrails during construction.
- Similarly, design roof parapets at 1.07 m (42 in.) high to eliminate the need for additional guardrails.
- Design project components such that they can be prefabricated and installed as assemblies rather than as individual pieces.
Case study of a Design for Safety process
- Intel D1D fab project, Hillsboro, Oregon
- Life Cycle Safety (LCS) : Safety-in- Design process
- $1.5 billion factory with nearly $700 million in construction
- Approximately 1 million gross square feet
- Design-bid-build strategy with a fast-track project delivery (12-month construction schedule)
- Peak labor 2400 craft workers, in excess of 4 million labor hours, 70 trade contractors
- Heavy structural concrete & steel for vibration
- Intense mechanical/electrical/process piping
- Schedule – First concrete to first equipment set in 9 months.
- Cost – Lowest Net Present Cost (initial cost, maintenance costs, and retrofit-ability).
- Scope – Capable of handling 2 technology development cycles and 5 high volume manufacturing cycles.
- Reliability – 99.7% uptime.
- Improved Safety in Design
- Design for the Environment (reduce energy use and water use).
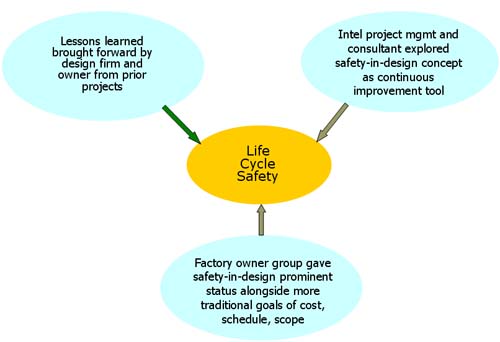
LCS Task Force structure
Vision for Safety in Design
Getting the Right People at the Right Time will result in:
- Reduced
- Incidents and injuries
- Changes in design
- Costs associated with late changes
- Rework
- Schedule duration
- Coordination issues associated with late changes
- Increased
- Upfront costs but decreased overall project costs
- Streamlining of project execution and communication
- Improved design
- Increase collaboration on all other areas of the project
Barriers to Safety in Design
How do we
- Get the right people involved at the right time?
- Capture their input?
- Address the paradigm that Safety in Design costs money.
- Influence the behaviors of the designers, constructors, and end users providing input?
- Motivate those managing the design and scope to include input at the right time?
- Not overburden the design delivery so we can maintain the project schedule?
The Life Cycle
Typical Project Delivery Model
- When is the constructor typically involved?
- Sometimes during design reviews
- Mostly after the design is complete
- Too Late!
- Need the Right Input at the Right Time!
- So When is the Right Time?
- Who are the Right People?
- What is the Right Input?
- Evaluate major building concepts
- Major structural decisions effect hoisting and overall project sequence, pacing and congestion.
- Determine building layouts
- Conduct Value Engineering
- Huge Opportunity!
- Designer (A/E)
- Develop options from owner requirements
- Technical experts, code requirements
- Owner Representatives
- Engineering, Operations, Maintenance, EHS
- Provide input on operation and maintenance issues
- Contractor
- Provide input on how facility would be constructed
- Reviewed impacts to schedule, sequencing, cost, logistics
- Trade Contractors
- Provide input on constructability and safety issues impacting their specific trade
Programming Phase - LCS
- Option Evaluations
- Life Cycle Safety was evaluated along with other goals:
- Cost, energy, emissions, etc.
- Relative risk of various options were evaluated against the Plan of Record (POR) or against one another
- Safety in Design Checklist used helped identify potential Risks
- Life Cycle Safety was evaluated along with other goals:
- Previous fabs built with basement below subfab or with trenches below subfab
- Plan of record (POR) has trenches
- LCS evaluation shows above grade basement (i.e. second subfab) reduces far more risks than POR or taller subfab
- LCS findings weighed against other goals
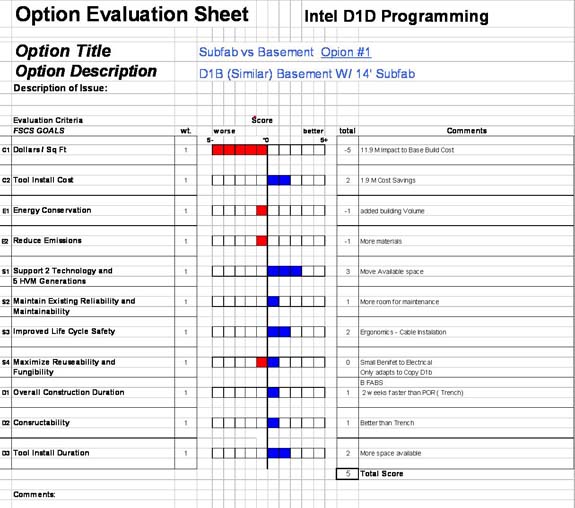
Design Phase - The Right Time
- Basic Design Delivery steps can include
- Schematic, Design Development, Construction Documents
- Design Team begins to fully engage and begin detailed design
- Equipment sizing, selection, and layout
- Detailed routing and coordination
- Design Changes and Value Engineering
- Multiple design reviews internal and external
- Issue the design packages for construction
- Designer identifies scope of design and package content
- Contractor primarily responsible for construction and retrofit
- Owner (Sustaining) primarily responsible for Operations and Maintenance
- Safety-in-design checklist
- Identified potential risks and mitigation
- Comments captured on review form
- Define/clarify "walkable" and "non-walkable" surfaces.
- Improved accessibility of racks and equipment for cleaning and maintenance.
- Need for sufficient space to stage, store, assemble and transport materials.
- Full basement concept vs. trenches for utilities.
- Floor coatings impact on ability to perform work in the building.
- Coordinating routing of utilities to reduce negative effects on other systems and eliminate "head-knockers."
- Incorporate tie-off anchorage points into base build.
- Location and configuration of equipment to reduce obstruction and fall hazards.
- Ceilings in interstitial space designed to be walkable and allow worker access.
- Floor finishes underneath raised metal floors designed to be smooth and easy to crawl across.
Benefits to the Project
- Shared ownership of resulting design
- Great relationship building
- Design it once
- A Design that is Safer to Construct, Operate and Maintain over the entire Life Cycle of the facility!
- Programming
- Focus Groups
- Safety features or issues in previous Fabs
- Suggestions for improvement for safety/efficiency
- 6 Focus Groups: 196 Comments
- Focus Groups
- Design Development
- LCS Package Review Sessions
- 22 Design Packages: 58 LCS Reviews
- 789 Comments
- LCS Package Review Sessions
Trade Contractor & Operations: LCS Comments
- 75% Safety Related (Directly or Indirectly)
- Post-construction Exit Focus Groups
- 29 focus groups
- 34 contractors representing 91% of hours worked on project
- Participants actually worked on the project in the field
- 465 Comments
- 71% Related to Design
- 47% Related to Construction
- 52% Design comments related to Structural/Architectural
- LCS supports integration of safety into project execution – not just Design!
Dealing with the Barriers
Addressing Liability Issues
-
American Institute of Architects
- Rule 2.105 requires that architects take action when their employer or their client makes decisions that will adversely affect the safety to the public of the finished product.
- National Society of Professional Engineers (NSPE):
- "Hold paramount the safety, health and welfare of the public in the performance of their professional duties ."
Court decisions have gone both ways on designer liability
Mallow v. Tucker 245 Cal. App. 2d 700; 54 Cal. Rptr. 174; 1966
- Worker's death caused by jackhammering into an underground power line.
- Alleges that the Architect was negligent in failing to warn through the preparations of plans and specifications.
- The architect was found negligent in preparing plans and specifications for construction.
Frampton v. Dauphin 436 Pa. Super. 486; 648 A.2d 326; 1994
- Does an architect hired to prepare construction drawings have a duty to warn construction workers of the presence of an existing overhead power line?
- Different from the Mallow case
- Hazard was observable by contractor, subcontractor, and workers
Supreme Court of Iowa 231 N.W.2d 907; 1975
- Alleges the Architect was negligent in preparing plans and specifications.
- Architect claims:
- He cannot be held liable for a claim until completion of project (obligation only to end user)
- Obligation for safety precautions and programs during construction rests solely on the contractor
- Iowa Supreme Court: Architect's duty to exercise reasonable care does not lie suspended in construction.
Education and Training of Architects and Engineers
University Engineering and Construction Curricula
- How much of a 4-year, Bachelor of Science degree curriculum covers construction worker safety?
- 1. It depends...
- What does it depend on?
- Engineering or construction program?
- Type of accreditation?
- Other factors?
Clues to the amount/type of safety content covered...(?)
-
U.K.: Most civil engineering programs cover safety (Al-Mufti, 1999)
- Primarily covered throughout curriculum rather than in a separate course.
- Canada: Inclusion of safety in engineering programs mandated by Canadian Engineering Accreditation Board (Christian, 1999)
- U.S. construction programs: Some programs are very proactive, while others are not (Coble, et al., 1998)
Study of Safety Content in Curricula
-
Research activities:
- Review of accreditation requirements of civil engineering and construction programs.
- Survey of civil engineering and construction programs.
- Paper published:
- Gambatese, J.A. (2003). "Safety Emphasis in University Engineering and Construction Programs." International e-Journal of Construction , special issue titled "Construction Safety Education and Training – A Global Perspective", May 14, 2003.
ABET Civil Engineering Program Accreditation
- Safety not included in ABET Civil Engineering criteria
-
Of the 36 responding departments:
- 10 have construction programs (28%).
- None offer a separate safety course.
ABET Construction Program Accreditation
" The program must demonstrate the graduates have: proficiency in mathematics through differential and integral calculus, probability and statistics, general chemistry, and calculus-based physics; proficiency in engineering design in a construction engineering specialty field; an understanding of legal and professional practice issues related to the construction industry; an understanding of construction processes, communications, methods, materials, systems, equipment, planning, scheduling, safety , cost analysis, and cost control; an understanding of management topics such as economics, business, accounting, law, statistics, ethics, leadership, decision and optimization methods, process analysis and design, engineering economics, engineering management, safety , and cost engineering."
Construction Program Accreditation
- American Council for Construction Education (ACCE)
- 4-year program requirements:
- At least one semester credit (1.5 quarter credits) must be devoted to safety.
- Can be covered in either a single course or in multiple courses.
- Safety content must include:
- Safe practices;
- Mandatory procedures, training, records, and maintenance; and
- Compliance, inspection, and penalties.
Survey of Construction Programs
- Similar responses from ABET and ACCE programs
- Of the 20 programs:
- 18 offer a course devoted to safety (90%).
- Safety course is typically 3 semester credits and at the Junior or Senior level.
- All require safety course be taken.
- Most common teaching materials: OSHA Standards for Construction (29 CFR 1926).
- 16 cover safety in other courses (80%).
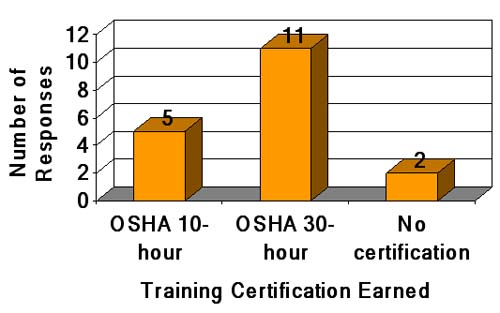
Barriers limiting extent of safety coverage in university curricula?
-
Accreditation:
- Extensive requirements
- Design focus (engineering programs)
- Resources:
- Faculty: number and expertise
- Operating budgets
- Industry Advisory Boards
- Others?
- Changes needed in curricula drivers:
- Accreditation
- Resources
- Industry Advisory Boards
-
In-class needs:
- Course materials
- Case studies
- Simulation tools
Take Aways
- Safety in Design is a Culture of Collaboration for Shared Ownership and Outcome.
- Life Cycle Safety can:
-
Reduce overall project costs through:
- Reduced redesign and rework in the field
- Earlier Planning for Efficiencies
-
Streamline Project Delivery/Execution through:
- More complete design packages
- Fewer field clarifications/changes
- Owner's representatives bought into the design
- Safer Project and Facility through:
- Construction and Commissioning
- Maintenance and Operations
- Retrofits
-
Reduce overall project costs through:
Summary
- Designers can play a role in making construction sites safer.
- Keys to designing for safety:
- Collaboration between all project team members
- Input from people who build
- Designers knowledgeable of:
- Design for safety concept
- Construction site safety
- Construction practices
- Safe designs
- Design for safety tools and guidelines available for use and reference
- Mitigation of A/E liability exposure
Collaboration in Design to Promote Safety
https://millrace.uoregon.edu/ uopress/index.cfm