Summary Statement
Student manual on electrical safety with information on recognizing, evaluating and avoiding hazards related to electricity.
January 2002
Safety Model Stage 3—Controlling Hazards: Safe Work Environment
How Do You Control Hazards?
In order to control hazards, you must first create a safe work environment, then work in a safe manner. Generally, it is best to remove the hazards altogether and create an environment that is truly safe. When OSHA regulations and the NEC are followed, safe work environments are created.
But, you never know when materials or equipment might fail. Prepare yourself for the unexpected by using safe work practices. Use as many safeguards as possible. If one fails, another may protect you from injury or death.
How Do You Create a Safe Work Environment?
A safe work environment is created by controlling contact with electrical voltages and the currents they can cause. Electrical currents need to be controlled so they do not pass through the body. In addition to preventing shocks, a safe work environment reduces the chance of fires, burns, and falls. You need to guard against contact with electrical voltages and control electrical currents in order to create a safe work environment. Make your environment safer by doing the following:
- Treat all
conductors—even “de-energized” ones—as if they
are energized until they are locked out and tagged.
- Lock out
and tag out circuits and machines.
- Prevent overloaded
wiring by using the right size and type of wire.
- Prevent exposure
to live electrical parts by isolating them.
- Prevent exposure
to live wires and parts by using insulation.
- Prevent shocking
currents from electrical systems and tools by grounding them.
- Prevent shocking
currents by using GFCI’s.
- Prevent too much current in circuits by using overcurrent protection devices.
|
At about
1:45 a.m., two journeyman electricians began replacing bulbs and
making repairs on light fixtures in a spray paint booth at an
automobile assembly plant. The job required the two electricians to climb on top of the booth and work from above. The top of the booth was filled with pipes and ducts that restricted visibility and movement. Flashlights were required. The electricians started at opposite ends of the booth. One electrician saw a flash of light, but continued to work for about 5 minutes, then climbed down for some wire. While cutting the wire, he smelled a burning odor and called to the other electrician. When no one answered, he climbed back on top of the booth. He found his co-worker in contact with a single-strand wire from one of the lights. Needle-nose wire strippers were stuck in the left side of the victim’s chest. Apparently, he had been stripping insulation from an improperly grounded 530-volt, single-strand wire when he contacted it with the stripper. In this case, the electricians knew they were working on energized circuits. The breakers in the booth’s control panel were not labeled and the lock used for lock-out/tag-out was broken. The surviving electrician stated that locating the means to de-energize a circuit often takes more time than the actual job. The electrician would be alive today if the following rules had been observed.
|
Lock out and tag out circuits and equipment
Create a safe work environment by locking out and tagging out circuits and machines. Before working on a circuit, you must turn off the power supply. Once the circuit has been shut off and
de-energized, lock out the switchgear to the circuit so the power cannot be turned back on inadvertently. Then, tag out the circuit with an easy-to-see sign or label that lets everyone know that you are working on the circuit. If you are working on or near machinery, you must lock out and tag out the machinery to prevent startup. Before you begin work, you must test the circuit to make sure it is de-energized.
![]() |
![]() |
Always test a circuit to make sure it is de-energized before working on it. | Lock-out/tag-out saves lives. |
Lock-Out/Tag-Out Checklist
Lock-out/tag-out is an essential safety procedure that protects workers from injury while working on or near electrical circuits and equipment. Lock-out involves applying a physical lock to the power source(s) of circuits and equipment after they have been shut off and de-energized. The source is then tagged out with an easy-to-read tag that alerts other workers in the area that a lock has been applied.
In addition to protecting workers from electrical hazards, lock-out/tag-out prevents contact
with operating equipment parts: blades, gears, shafts, presses, etc.
A
worker was replacing a V-belt on a dust collector blower. Before
beginning work, he shut down the unit at the local switch. However,
an operator in the control room restarted the unit using a remote
switch. The worker’s hand was caught between the pulley and
belts of the blower, resulting in cuts and a fractured finger. When performing lock-out/tag-out on machinery, you must always lock out and tag out ALL energy sources leading to the machinery. |
Also, lock-out/tag-out prevents the unexpected release of hazardous gasses, fluids, or solid matter in areas where workers are present.
An
employee was cutting into a metal pipe using a blowtorch. Diesel
fuel was mistakenly discharged into the line and was ignited by
his torch. The worker burned to death at the scene. All valves along the line should have been locked out, blanked out, and tagged out to prevent the release of fuel. Blanking is the process of inserting a metal disk into the space between two pipe flanges. The disk, or blank, is then bolted in place to prevent passage of liquids or gasses through the pipe. |
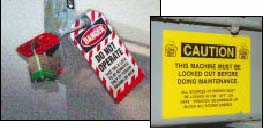
When performing lock-out/tag-out on circuits and equipment, you can use the checklist below.
- Identify
all sources of electrical energy for the equipment or circuits in
question.
- Disable backup
energy sources such as generators and batteries.
- Identify
all shut-offs for each energy source.
- Notify all
personnel that equipment and circuitry must be shut off, locked
out, and tagged out. (Simply turning a switch off is NOT enough.)
- Shut off
energy sources and lock switchgear in the OFF position. Each
worker should apply his or her individual lock. Do not give your
key to anyone.
- Test equipment
and circuitry to make sure they are de-energized. This must be done
by a qualified person.*
- Deplete stored
energy by bleeding, blocking, grounding, etc.
- Apply a tag
to alert other workers that an energy source or piece of equipment
has been locked out.
- Make sure
everyone is safe and accounted for before equipment and circuits
are unlocked
and turned back on. Note that only a qualified person may determine when it is safe to re-energize circuits.
*OSHA
defines a “qualified person” as someone who has
received mandated training on the hazards and on the construction and operation of equipment involved in a task. |
Control inadequate wiring hazards
Electrical hazards result from using the wrong size or type of wire. You must control such hazards to create a safe work environment. You must choose the right size wire for the amount of current
expected in a circuit. The wire must be able to handle the current safely. The wire’s insulation must be appropriate for the voltage and tough enough for the environment. Connections need to be reliable and protected.
Use the right size and type of wire. |
AWG—American Wire Gauge—a measure of wire size |
![]() |
Wires come in different sizes. The maximum current each size can conduct safely is shown. |
Control hazards of fixed wiring
The wiring methods and size of conductors used in a system depend on several factors:
- Intended
use of the circuit system
- Building
materials
- Size and
distribution of electrical load
- Location
of equipment (such as underground burial)
- Environmental
conditions (such as dampness)
- Presence
of corrosives
- Temperature extremes
Aluminum wire and connections should be handled with special care. Connections made with aluminum wire can loosen due to heat expansion and oxidize if they are not made properly. Loose or oxidized connections can create heat or arcing. Special clamps and terminals are necessary to make proper connections using aluminum wire. Antioxidant paste can be applied to connections to prevent oxidation.
|
![]() |
Nonmetalic sheathing helps protect wires from damage. |
Control hazards of flexible wiring
Use flexible wiring properly
Electrical cords supplement fixed wiring by providing the flexibility required for maintenance, portability, isolation from vibration, and emergency and temporary power needs.
Flexible wiring can be used for extension cords or power supply cords. Power supply cords can be removable or permanently attached to the appliance.
|
A 29-year-old
male welder was assigned to work on an outdoor concrete platform
attached to the main factory building. He wheeled a portable arc
welder onto the platform. Since there was not an electrical outlet
nearby, he used an extension cord to plug in the welder. The male
end of the cord had four prongs, and the female end was spring-loaded.
The worker plugged the male end of the cord into the outlet. He
then plugged the portable welder’s power cord into the female
end of the extension cord. At that instant, the metal case around
the power cord plug became energized, electrocuting the worker. An investigation showed that the female end of the extension cord was broken. The spring, cover plate, and part of the casing were missing from the face of the female connector. Also, the grounding prong on the welder’s power cord plug was so severely bent that it slipped outside of the connection. Therefore, the arc welder was not grounded. Normally, it would have been impossible to insert the plug incorrectly. But, since the cord’s female end was damaged, the “bad” connection was able to occur. Do not let this happen to you. Use these safe practices:
|
DO NOT use flexible wiring in situations where frequent inspection would be difficult, where damage would be likely, or where long-term electrical supply is needed. Flexible cords cannot be used as a substitute for the fixed wiring of a structure. Flexible cords must not be . . .
- run through
holes in walls, ceilings, or floors;
- run through
doorways, windows, or similar openings (unless
physically protected);
- attached
to building surfaces (except with a tension take-up
device within 6 feet of the supply end);
- hidden in
walls, ceilings, or floors; or
- hidden in conduit or other raceways.
|
Use the right extension cord
The size of wire in an extension cord must be compatible with the amount of current the cord will be expected to carry. The amount of current depends on the equipment plugged into the extension cord. Current ratings (how much current a device needs to operate) are often printed on the nameplate. If a power rating is given, it is necessary to divide the power rating in watts by the voltage to find the current rating. For example, a 1,000-watt heater plugged into a 120-volt
circuit will need almost 10 amps of current. Let’s look at another example: A 1-horsepower electric motor uses electrical energy at the rate of almost 750 watts, so it will need a minimum of about 7 amps of current on a 120-volt circuit. But, electric motors need additional current as they startup or if they stall, requiring up to 200% of the nameplate current rating. Therefore, the motor would need 14 amps.
Add to find the total current needed to operate all the appliances supplied by the cord. Choose a wire size that can handle the total current.
American
Wire Gauge (AWG)
|
|
Wire
Size
|
Handles
up to
|
#10
AWG
|
30
amps
|
#12
AWG
|
25
amps
|
#14
AWG
|
18
amps
|
#16
AWG
|
13
amps
|
Remember:
The larger the gauge number, the smaller the wire!
|
The length of the extension cord also needs to be considered when selecting the wire size. Voltage drops over the length of a cord. If a cord is too long, the voltage drop can be enough to damage equipment. Many electric motors only operate safely in a narrow range of voltages and will not work properly at voltages different than the voltage listed on the nameplate. Even though light bulbs operate (somewhat dimmer) at lowered voltages, do not assume electric motors will work correctly at less-than-required voltages. Also, when electric motors start or operate under load, they require more current. The larger the size of the wire, the longer a cord can be without causing a voltage drop that could damage tools and equipment.
|
|
|
The grounding path for extension cords must be kept intact to keep you safe. A typical extension cord grounding system has four components:
- a third wire
in the cord, called a ground wire;
- a three-prong
plug with a grounding prong on one end of the cord;
- a three-wire,
grounding-type receptacle at the other end of the cord; and
- a properly grounded outlet.
|
![]() |
Control hazards of exposed live electrical parts: isolate energized components
Electrical hazards exist when wires or other electrical parts are exposed. These hazards need to be controlled to create a safe work environment. Isolation of energized electrical parts makes them inaccessible unless tools and special effort are used. Isolation can be accomplished by placing the energized parts at least 8 feet high and out of reach, or by guarding. Guarding is a type of isolation that uses various structures—like cabinets, boxes, screens, barriers, covers, and partitions—to close-off live electrical parts.
![]() |
This
exposed electrical equipment is guarded by an 8-foot fence.
|
|
![]() |
A 20-year-old
male laborer was carrying a 20-foot piece of iron from a welding
shop to an outside storage rack. As he was turning a corner near
a bank of electrical transformers, the top end of the piece of
iron struck an uninsulated supply wire at the top of a transformer.
Although the transformers were surrounded by a 6-foot fence, they
were about 3 feet taller than the fence enclosure. Each transformer
carried 4,160 volts. When the iron hit the supply wire, the laborer was electrocuted. A forklift operator heard the iron drop to the ground at about 8:46 a.m. and found the victim 5 minutes later. He was pronounced dead on arrival at a local hospital.
|
Take the following precautions to prevent injuries from contact with live parts:
- Immediately
report exposed live parts to a supervisor or teacher. As a student,
you should never attempt to correct the condition yourself without
supervision.
- Provide guards
or barriers if live parts cannot be enclosed completely.
- Use covers,
screens, or partitions for guarding that require tools to remove
them.
- Replace covers
that have been removed from panels, motors, or fuse boxes.
- Even when
live parts are elevated to the required height (8 feet), care should
be taken when using objects (like metal rods or pipes) that can
contact these parts.
- Close unused conduit openings in boxes so that foreign objects (pencils, metal chips, conductive debris, etc.) cannot get inside and damage the circuit.
![]() |
This cover cannot be removed without special tools. |
Control hazards of exposure to live electrical wires: use proper insulation
Insulation is made of material that does not conduct electricity (usually plastic, rubber, or fiber). Insulation covers wires and prevents conductors from coming in contact with each other or any other conductor. If conductors are allowed to make contact, a short circuit is created. In a short circuit, current passes through the shorting material without passing through a load in the circuit, and the wire becomes overheated. Insulation keeps wires and other conductors from touching, which prevents electrical short circuits. Insulation prevents live wires from touching people and animals, thus protecting them from electrical shock.
A 29-year-old
male maintenance worker was found at 3:45 a.m. lying on his back
and convulsing. Beside him were an overturned cart and an electric
welding machine, both lying in a pool of water on the concrete
floor. Arcing was visible between the welding machine and the
floor. The worker was transported to the closest hospital, where
he was pronounced dead. An examination of the welding machine showed that there were exposed conductors in the machine’s cables. There were numerous cuts and scrapes in the cables’ insulation. On other parts of the machine, insulation was damaged or missing. Also, the machine did not have a ground connection. Investigators concluded that the maintenance worker was electrocuted when he tried to turn off the welding machine, which was sitting on the cart. The metal frame of the machine had become energized due to the damaged insulation. When he touched the energized frame, he completed the conducting path to ground. The current traveled through his body to ground. Since he was probably standing in water, the risk of a ground fault was even greater. You must take steps to decrease such hazards in your workplace:
|
Insulation helps protect wires from physical damage and conditions in the environment. Insulation is used on almost all wires, except some ground wires and some high-voltage transmission lines.
Insulation is used internally in tools, switches, plugs, and other electrical and electronic devices.
Special insulation is used on wires and cables that are used in harsh environments. Wires and cables that are buried in soil must have an outer covering of insulation that is flame-retardant and resistant to moisture, fungus, and corrosion.
In all situations, you must be careful not to damage insulation while installing it. Do not allow staples or other supports to damage the insulation. Bends in a cable must have an inside radius of at least 5 times the diameter of the cable so that insulation at a bend is not damaged. Extension cords come with insulation in a variety of types and colors. The insulation of extension cords is especially important. Since extension cords often receive rough handling, the insulation can be damaged. Extension cords might be used in wet places, so adequate insulation is necessary to prevent shocks. Because extension cords are often used near combustible materials (such as wood shavings and sawdust) a short in an extension cord could easily cause arcing and a fire.
Insulation on individual wires is often color-coded. In general, insulated wires used as equipment grounding conductors are either continuous green or green with yellow stripes. The grounded conductors that complete a circuit are generally covered with continuous white or gray insulation. The ungrounded conductors, or “hot” wires, may be any color other than green, white, or gray. They are usually black or red.
Conductors and cables must be marked by the manufacturer to show the following:
- maximum voltage
capacity,
- AWG size,
- insulation-type
letter, and
- the manufacturer’s name or trademark.
![]() |
Arc-fault circuit breaker. |
Control hazards of shocking currents
Ground circuits and equipment
When an electrical system is not gro unded properly, a hazard exists. This is because the parts of an electrical wiring system that a person normally touches may be energized, or live, relative to ground. Parts like switch plates, wiring boxes, conduit, cabinets, and lights need to be at 0 volts relative to ground. If the system is grounded improperly, these parts may be energized. The metal housings of equipment plugged into an outlet need to be grounded through the plug.
![]() |
Ground electrical devices. |
Grounding is connecting an electrical system to the earth with a wire. Excess or stray current travels through this wire to a grounding device (commonly called a “ground”) deep in the earth. Grounding prevents unwanted voltage on electrical components. Metal plumbing is often used as a ground. When plumbing is used as a grounding conductor, it must also be connected to a grounding device such as a conductive rod. (Rods used for grounding must be driven at least 8 feet into the earth.) Sometimes an electrical system will receive a higher voltage than it is designed to handle. These high voltages may come from a lightning strike, line surge, or contact with a higher-voltage line. Sometimes a defect occurs in a device that allows exposed metal parts to become energized. Grounding will help protect the person working on a system, the system itself, and others using tools or operating equipment connected to the system. The extra current produced by the excess voltage travels relatively safely to the earth.
Grounding creates a path for currents produced by unintended voltages on exposed parts. These currents follow the grounding path, rather than passing through the body of someone who touches the energized equipment. However, if a grounding rod takes a direct hit from a lightning strike and is buried in sandy soil, the rod should be examined to make sure it will still function properly. The heat from a lightning strike can cause the sand to turn into glass, which is an insulator. A grounding rod must be in contact with damp soil to be effective.
![]() |
![]() |
Grounding rod in the earth. | Grounding-type receptacle. |
Leakage current occurs when an electrical current escapes from its intended path. Leakages are sometimes low-current faults that can occur in all electrical equipment because of dirt, wear, damage, or moisture. A good grounding system should be able to carry off this leakage current. A ground fault occurs when current passes through the housing of an electrical device to ground. Proper grounding protects against ground faults. Ground faults are usually caused by misuse of a tool or damage to its insulation. This damage allows a bare conductor to touch metal parts or the tool housing.
When you ground a tool or electrical system, you create a low-resistance path to the earth (known as a ground connection). When done properly, this path has sufficient current-carrying capacity to eliminate voltages that may cause a dangerous shock.
Grounding does not guarantee that you will not be shocked, injured, or killed from defective equipment. However, it greatly reduces the possibility.
Equipment needs to be grounded under any of these circumstances:
- The equipment
is within 8 feet vertically and 5 feet horizontally of the floor
or walking surface.
- The equipment
is within 8 feet vertically and 5 feet horizontally of grounded
metal objects you could touch.
- The equipment
is located in a wet or damp area and is not isolated.
- The equipment is connected to a power supply by cord and plug and is not double-insulated.
The use of GFCI’s has lowered the number of electrocutions dramatically. A GFCI is a fast-acting switch that detects any difference in current between two circuit conductors. If either conductor comes in contact—either directly or through part of your body—with a ground (a situation known as a ground fault), the GFCI opens the circuit in a fraction of a second. If a current as small as 4 to 6 mA does not pass through both wires properly, but instead leaks to the ground, the GFCI is tripped. The current is shut off.
There is a more sensitive kind of GFCI called an isolation GFCI. If a circuit has an isolation GFCI, the ground fault current passes through an electronic sensing circuit in the GFCI. The electronic sensing circuit has enough resistance to limit current to as little as 2 mA, which is too low to cause a dangerous shock.
GFCI’s are usually in the form of a duplex receptacle. They are also available in portable and plug-in designs and as circuit breakers that protect an entire branch circuit. GFCI’s can operate on both two- and three-wire ground systems. For a GFCI to work properly, the neutral conductor (white wire) must (1) be continuous, (2) have low resistance, and (3) have sufficient current-carrying capacity.
![]() |
Portable GFCI. |
GFCI’s help protect you from electrical shock by continuously monitoring the circuit. However, a GFCI does not protect a person from line-to-line hazards such as touching two “hot” wires (240 volts) atthe same time or touching a “hot” and neutral wire at the same time. Also be aware that instantaneous currents can be high when a GFCI is tripped. A shock may still be felt. Your reaction to the shock could cause injury, perhaps from falling.
Test GFCI’s regularly by pressing the “test” button. If the circuit does not turn off, the GFCI is faulty and must be replaced.
A
female assistant manager of a swim club was instructed to add
a certain chemical to the pool. She went down into the pump room,
barefoot. The room was below ground level, and the floor was covered
with water. She filled a plastic drum with 35-40 gallons of water,
then plugged a mixing motor into a 120-volt wall outlet and turned
on the motor. The motor would be used to mix the water and the
chemical, then the solution would be added to the pool. While
adding the chemical to the water in the drum, she contacted the
mixing motor with her left hand. Apparently, the motor had developed
a ground fault. Because of the ground fault, the motor was energized,
and she was electrocuted. A co-worker found the victim slumped
over the drum with her face submerged in water. The co-worker
tried to move the victim but was shocked. The assistant manager
was dead on arrival at a local hospital. An investigation showed that the mixing motor was in poor condition. The grounding pin had been removed from the male end of the power cord, resulting in a faulty ground. The circuit was equipped with a GFCI, but it was not installed properly. A properly wired and functioning GFCI could have sensed the ground fault in the motor and de-energized the circuit. Take a look at what could have been done to prevent this death.
|
The NEC requires that GFCI’s be used in these high-risk situations:
- Electricity
is used near water.
- The user
of electrical equipment is grounded (by touching grounded material).
- Circuits
are providing power to portable tools or outdoor receptacles.
- Temporary wiring or extension cords are used.
![]() |
Install bonding jumpers around nonconductive material. |
Use GFCI’s to help protect people in damp areas. |
bonding—joining electrical parts to assure a conductive path |
Bond components to assure grounding path
In order to assure a continuous, reliable electrical path to ground, a bonding jumper wire is used to make sure electrical parts are connected. Some physical connections, like metal conduit coming into a box, might not make a good electrical connection because of paint
or possible corrosion. To make a good electrical connection, a bonding
jumper needs to be installed.
A metal cold water pipe that is part of a path to ground may need bonding jumpers around plastic antivibration devices, plastic water meters, or sections of plastic pipe. A bonding jumper is made of conductive material and is tightly connected to metal pipes with screws or clamps to bypass the plastic and assure a continuous grounding path. Bonding jumpers are necessary because plastic does not conduct electricity and would interrupt the path to ground.
Additionally, interior metal plumbing must be bonded to the ground for electrical service equipment in order to keep all grounds at the same potential (0 volts). Even metal air ducts should be bonded to electrical service equipment.
Control overload current hazards
When a current exceeds the current rating of equipment or wiring, a hazard exists. The wiring in the circuit, equipment, or tool cannot handle the current without heating up or even melting. Not only will the wiring or tool be damaged, but the high temperature of the conductor can also cause a fire. To prevent this from happening, an overcurrent protection device (circuit breaker or fuse) is used in a circuit. These devices open a circuit automatically if they detect current in excess of the current rating of equipment or wiring. This excess current can be caused by an overload, short circuit, or high-level ground fault.
![]() |
Use overcurrent protection devices (circuit breakers or fuses) in circuits. |
Overcurrent protection devices are designed to protect equipment and structures from fire. They do not protect you from electrical shock! Overcurrent protection devices stop the flow of current in a circuit when the amperage is too high for the circuit. A circuit breaker or fuse will not stop the relatively small amount of current that can cause injury or death. Death can result from 20 mA (.020 amps) through the chest (see Section 2). A typical residential circuit breaker or fuse will not shut off the circuit until a current of more than 20 amps is reached!
But overcurrent protection devices are not allowed in areas where they could be exposed to physical damage or in hazardous environ-ments. Overcurrent protection devices can heat up and occasionally arc or spark, which could cause a fire or an explosion in certain areas. Hazardous environments are places that contain flammable or explosive materials such as flammable gasses or vapors (Class I Hazardous Environments), finely pulverized flammable dusts (Class II Hazardous Environments), or fibers or metal filings that can catch fire easily (Class III Hazardous Environments). Hazardous environments may be found in aircraft hangars, gas stations, storage
plants for flammable liquids, grain silos, and mills where cotton fibers may be suspended in the air. Special electrical systems are required in hazardous environments.
If an overcurrent protection device opens a circuit, there may be a problem along the circuit. (In the case of circuit breakers, frequent tripping may also indicate that the breaker is defective.) When a circuit breaker trips or a fuse blows, the cause must be found.
A circuit breaker is one kind of overcurrent protection device. It is a type of automatic switch located in a circuit. A circuit breaker trips when too much current passes through it. A circuit breaker should not be used regularly to turn power on or off in a circuit, unless the breaker is designed for this purpose and marked “SWD” (stands for “switching device”).
A fuse is another type of overcurrent protection device. A fuse contains a metal conductor that has a relatively low melting point. When too much current passes through the metal in the fuse, it heats up within a fraction of a second and melts, opening the circuit. After an overload is found and corrected, a blown fuse must be replaced with a new one of appropriate amperage.
|
![]() |
|
Summary of Section 7
Control contact with electrical voltages and control electrical currents to create a safe work environment.
- Lock out and
tag out circuits and machines.
- Prevent overloaded
wiring by using the right size and type of wire.
- Prevent exposure
to live electrical parts by isolating them.
- Prevent exposure
to live wires and parts by using insulation.
- Prevent shocking
currents from electrical systems and tools by grounding them.
- Prevent shocking
currents by using GFCI’s.
- Prevent too much current in circuits by using overcurrent protection devices.