Summary Statement
Presentation on basic machine guarding including associated hazards.
Pre-Industrial revolution
- Waterwheel was source of injuries
- Injuries taken as matter of course since infrequent
- Regarded as victim’s own fault
Industrial Revolution
- Steam engine and electric motors invented
- Increased use of power driven machinery
- Workers caught by projecting set screws on line shafting
- Crushed flat by belts and pulleys
- Chewed inch by inch in gears and screw conveyors
Public Reaction
- Workers felt unguarded machines partly employers fault
- Newspapers printed details of gory cases
- Labor unions fought for guarding of hazardous machinery
Massachusetts 1877
- First law requiring guarding of hazardous machinery
- Outrage over young girls getting fingers cut off or mangled in adjacent gears of textile machines
- By 1900 most industrialized states had laws requiring machine guarding
Massachusetts Study 1939
- Studied injuries from 1933-1938
- Woodworking machines highest source of all machine injuries with 18.5%
- Saws 53% of those injuries (circular saws #1)
1949 Illinois
- 4,908 injuries due to machines requiring worker compensation in manufacturing or 21.7 % of total
- Little attention placed on safe placing of machines, emergency stops, and safe arrangement of machine controls
Safety Codes
- Safety Code for Mechanical Power Transmission Apparatus published in the 1940’s by American Standards Association
- Very similar to OSHA 1910.219 std.
- Required forethought guarding vs. afterthought guarding for machine manufacturers
Machine Hazards
- Motions
Rotating: in-running nip points, spindles, shaft ends, couplings
Reciprocating: back-and-forth, up-and-down
Transverse: movement in a straight, continuous line
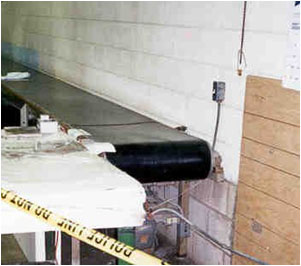
- Operations
Cutting: bandsaws, drills, milling machines, lathes
Punching: punch presses, notchers
Shearing: mechanical, pneumatic, or hydraulic shears
Bending: press brakes, tube benders, plate rolls
Principles of Machine Guarding
- Safe Distance - 7’ rule of belts, etc.
- Guards - employees can’t get in hazardous area through the use of barriers.
- Table 0-10 for guard opening design
- Devices - Presence sensing mats, pullbacks, light curtains, restrains
Table O-10
Distance of opening from the point of operation hazard (in inches) | Maximum width of opening (in inches) |
1/2 to 1 1/2 | ¼ |
1 1/2 to 2 1/2 | 3/8 |
2 1/2 to 3 ½ | ½ |
3 1/2 to 5 ½ | 5/8 |
5 1/2 to 6 ½ | ¾ |
6 1/2 to 7 ½ | 7/8 |
7 1/2 to 12 ½ | 1 ¼ |
12 1/2 to 15 ½ | 1 ½ |
15 1/2 to 17 ½ | 1 7/8 |
17 1/2 to 31 ½ | 2 1/8 |
Types of Machine Safeguards
- Barriers and guards
- Mechanical or electronic devices that restrict contact, such as presence-sensing, restraining, or tripping devices, two-hand controls, or gates.
- Feeding and ejection methods that eliminate part handling in the hazard zone.
Definitions
- Point of Operation - work such as bending, punching, cutting on the material – P.O.O
- Nip point - location where machine pieces come together such as belts and a pulley, two in-running rollers, etc.
SIGCASE
- $140,00
- Unguarded mandrel winder carriage
- Unguarded rotating shaft amputated worker arm when sleeve caught on a collar bolt
Wire or filament is wound around a rotating mandrel.
Guarding Most Cited
- Unguarded nip points, rotating parts
- No P.O.O. Guarding
- Tongue grinder ¼”
- Work Rest 1/8”
- Unguarded pulleys
- Unguarded Vertical Belts
- Chain and sprocket not guarded
- Lower blade guard radial arm saw
- No punch press inspection records
- Unguarded horizontal belts
Shafts
- Hazard - caught in
- Unguarded rotating shafts can easily snagged clothing or hair
- Fixed Guards used
In-running Nip Points
- Belts and Pulleys
- Chains and Sprockets
- Gears
- In-running rollers
- Fixed Guards used the most
AMPUTATE LEP
- CSHO will review OSHA 200 and 300 logs for all amputation injuries or hazards
- Limited to hazards associated with power presses, press brakes, saws, shears, slitters, and slicers, but may be expanded
- Inspections began March 26, 2002
- CPL 2-1.35
- CSHO will also evaluate employee exposures during the following:
- Regular operation of machine
- Setup/threading/preparation for operation of machine
- Clearing jamups or upset conditions
- Making adjustments while machine is operating
- Cleaning of machine
- Oiling/greasing of machine /machine parts
- Scheduled/unscheduled maintenance
- Lockout/tagout considerations
Punch Presses
- Point of Operation guarding required on front, back, sides
- Prevent Double trips - double trip took both hands of a worker in 1997
- Inspection, records, employee training
Horizontal Molding Presses
- Hazard is getting caught in horizontal ram
- Interlocked doors used
- Lockout for repairs
Press Brakes
- Employee reaches in to get stuck material
- Pullbacks, light curtains
- 12 inches safe distance per ANSI
- Opening too large
- 1984 - Eight fingers lost on hydraulic brake in IL
Shears
- Most come with guards
- Table O-10 distance must be used
- Guards bent back on this shear
Slicers
- Commonly used to slice meat and food
- Use rotary blade
- Guillotine cutters used in other industries
- Most injuries occur in restaurants and grocery stores
Circular Saws
- Lower blade guard required
- Clean saw and blade to prevent guard from sticking
- Aurora 1998 - 100+ stitches from saw
Vertical Bandsaw
- Adjustable guard to height of product
- Many injuries by guiding product into POO
- Handling cold slippery products will increase chances of slipping into POO
Horizontal Bandsaw
- Unused portion of blade need to be guarded
- No oversized blades used
Radial Arm Saw
- Lower blade awareness device
- Retracts to original position
- Does not extend past plane of table
- Anti-kick back device
Table Saws
- Top guard
- Magnetic restart
- Spreader
- Push sticks
- Anti-kick device
Chop Saw
- Lower blade awareness device
- Speed marked on saw
- Clean saw blades to prevent varnish/sap buildup
Food Mixers
- Requires cleaning of food
- Rotating blades
- Hand Amputation in 2002
Conveyors
- Emergency stops placed
- ANSI B20.1
- In-running nip points guarded by fixed guards
- This elevator section unguarded
Calendars and Rubber Mills
- Emergency trips placed so operator breaks emergency stop cable
- Less than a second to get pulled in
Take-up Coils/Reels
- Often slow moving
- Several amputations due getting caught in nip point
- Interlock guards or barriers used
- Unguarded fabrictake-up roll nip point
Fans
- Hazard - rotating blades
- Use wire mesh guard
Printing Press
- Fixed guard prevent entry to moving nip point when cleaning rolls
- Interlocked Guards for ink addition
Packaging Machines
- Multiple pinch points
- Employee reach in to clear jams
- Fixed guards or light curtains
- Lockout is needed
- 1999 - Aurora amputation
Drill Press
- Hair or clothing get caught in rotating shaft
- Automatic ones can guard against pinch point via 1/4 opening or presence sensing devices
Belt Sanders
- Hazard is nip point
- Use fixed guard
Bench Grinders
- Tongue Guard - 1/4”
- Work rest - 1/8”
- Blotters used
- Ring test
- Spindle speed
- Side nut guarded
Surface Grinder
- Half moon guard over wheel
- No feeding by hand
- Proper wheel speed
Lathes
- Eye protection glasses with side-shields.
- Use Guard over chuck
- No loose sleeves, long hair, or jewelry
- Work is securely clamped in the chuck. Start the lathe at low speed and increase the speed gradually.
- Removing the chuck key immediately after use.
Mixer/Blenders
- Fixed guard needed
- Worker reaches in to clean or clear jam and it restarts
- Must lockout
- 1995 - arm amputation was $1M loss
Auctioned or Used Machines
- Often missing guards
- Employer must guard even if not designed with them
- Consult ANSI standard applicable
Training
- A description and identification of the hazards associated with the machine(s).
- A description of the safeguards and their functions and use.
- Instruction on how, and under what circumstances safeguards may be removed, and by whom.
- Instruction on what to do if a safeguard is missing, damaged, or inadequate
Summary
- If a four year could get hurt with a machine, an adult will eventually get hurt too.
Quiz
- Tongues on grinders must be adjusted to ___________ inches from the wheel.
- List the guards required on a table saw. ______________ _____________ ______________
- If you were working 3 inches from the point operation, the guard opening would be ___________ inches maximum.
- Belts and pulleys under __________ feet would need guarding.
Resources
- Here is the OSHA eTool site. http://www.osha.gov/SLTC/etools/machineguarding/index.html
- http://www.orosha.org/subjects/machine_guarding.html has a video from Oregon OSHA on the topic.
- Every state has free consultation available to small employers.
Further
- This was prepared as a collaborative effort of several friends as a preliminary aid for anyone covering basic machine guarding.
- These are just some of the issues. A comprehensive job hazard analysis should be conducted for any task where someone can get hurt.
- This is not an official OSHA publication. Those will be on the OSHA.gov website.
- Newquist.john@dol.gov is my email if you see any errors.
- 312-353-5977 is my contact phone number.
- I want to thank Ron Stephens, Sharon H. Merri M. Misette K, Jim W. and Aaron P. for all their assistance in answering questions and providing insight to the many hazards in this sector.