Not An Accident: Preventable Deaths 2015
Summary Statement
This report is released to mark Workers’ Memorial Week, a remembrance of those who have lost their lives at work. The event is observed nationwide – and around the world – by surviving family members as well as health
and safety activists in workplaces and communities. It coincides with the anniversary of the U.S. Occupational Safety and Health Act, which took effect on April 28, 1971.
April 2015
Table of Contents
Documenting Preventable Deaths
- Dying on the job
- Faces of U.S. Fatalities
- 54,000 Deaths, 2 Prosecutions
- Proven Prevention Strategies
- Erik Deighton
- John Edd Dunnivant
- Fabian Martinez
- LaDonte McCruder
- Agnes Ann McKithen Carter
- Joel Metz
- Juan Carlos Reyes
Making Work Safer: Local COSH Initiatives
Executive Summary
Time and again, it's not an accident.
- When LaDonte McCruder, a 31-year old worker from Birmingham, Alabama dies in an unprotected
construction trench, it’s not an accident. Trench cave-ins are a well-known and documented construction
hazard – and OSHA requires specific protections to prevent these disasters. - When Erik Deighton, a 23-year old auto parts worker from Shelby Township, Michigan is crushed inside a stamping machine, it’s not an accident. Current standards require machine guards and other safety mechanisms to prevent exactly this sort of tragedy from taking place.
- When Juan Carlos Reyes, a 35-year old construction worker from Brownsville, Texas dies after falling four stories on a building site, it’s not an accident. When employers provide a proper fall protection program, workers can eliminate falls, or reduce the chance of fatal impact if they occur. Reyes had no such chance.
An accident is an unpredictable event, difficult if not impossible to prevent – like when a meteor lands in your living room. Workplace deaths, unfortunately, are much less rare than meteors. They are also much more predictable. Decades of research and practice in workplace safety and health have identified the most common workplace hazards – and proven strategies for prevention.
If employers were to implement these strategies more consistently and effectively, thousands of workers who have died on the job would be alive today.
THIS YEAR'S PREVENTABLE DEATHS REPORT INCLUDES
DOCUMENTING PREVENTABLE DEATHS
On April 28th, 2015, in observance of Workers’ Memorial Day, National COSH will release the U.S. Worker Fatality Database. The most comprehensive effort to date to gather specific information about workplace deaths, it will cover some 1,500 fatalities, about one-third of all workers who died on the job in 2014. The database is a collaborative, community-based research effort, developed in response to a lack of publicly available information from governmental sources.
INFOGRAPHIC: DYING ON THE JOB
In 2013, 4,585 workers died due to unsafe working conditions, according to the most recent data available from the U.S. Bureau of Labor Statistics (BLS).
Epidemiological studies estimate that an additional 50,000 people die each year from long-term exposure to workplace hazards such as asbestos, silica and benzene. These deaths are also preventable. Engineering controls and product substitution can significantly reduce worker exposure to hazardous materials.
Hispanic workers are at greater risk of death on the job than other workers, showing a nine percent increase in sudden workplace fatalities between 2012 and 2013. Fatality rates decreased for African-American, Asian and white workers during the same time period. Temporary or contract workers are also significantly at risk, with 749 deaths from sudden events in 2013, sixteen percent of the U.S. total.
INFOGRAPHIC: FACES OF U.S. FATALITIES
This feature demonstrates the number and rate of on-the-job fatalities for different industries, according to preliminary BLS data for 2013. It also identifies specific workers who lost their lives in each industry. As in previous years, agriculture, fishing and forestry remains the most dangerous sector of the U.S. economy, with a death rate of 23.2 workers for every 100,000 employees.
INFOGRAPHIC: 54,000 DEATHS. TWO PROSECUTIONS
The tens of thousands of U.S. workers who die from workplace-related causes are frequently victims of recklessness, negligence and worse on the part of their employers. But there were just two prosecutions for workplace deaths in 2014.
Randall Miller, a film director, was indicted in Georgia for involuntary manslaughter for the death of camera assistant Sarah Jones. He pled guilty in March 2015 and was sentenced to a two-year prison term; his attorney expects him to be out of prison after a year.
Don Blankenship, former CEO of Massey Energy, was indicted by a federal grand jury in West Virginia for conspiracy to violate mine safety laws, following a 2010 tragedy that claimed the lives of 29 miners in Upper Big Branch. Blankenship is scheduled to go to trial in July 2015.
The Philadelphia Area Project on Occupational Safety and Health (PhilaPOSH) has established a Criminal Prosecution committee, to encourage greater employer accountability for severe violations of workplace safety laws. National COSH is in consultation with national prosecutors associations to identify guidelines for prosecuting criminal violations in the workplace.
INFOGRAPHIC: PROVEN APPROACHES TO PREVENTION
We identify here the most common events leading to sudden death in the workplace, along with tested and proven strategies for preventing these incidents. Engineering controls, up-to-date equipment, better training and removing identifiable hazards can save lives – every day – in U.S. workplaces.
CASE STUDIES
Stories of seven workers whose lives were cut short in 2014. Black, white and Hispanic, ranging in age from 21 to 57, they represent thousands more who could be alive today if their employers had followed proper safety protocols.
NATIONAL COSH POLICY PLATFORM
An agenda for reform in workplace safety and health, as well as hazard-specific improvements. Our goal is to improve working conditions across industry sectors, for union and non-union workers, including permanent employees and those with temporary status.
INFOGRAPHIC: MAKING WORK SAFER
A summary of the research, training and organizing carried out by local COSH groups across the United States. A growing network of labor, community and workplace activists is focused on assisting workers in exercising their right to a safe workplace.
INFORMATION FOR THIS REPORT WAS GATHERED FROM A VARIETY OF SOURCES, INCLUDING:
- U.S. Bureau of Labor Statistics, Census of Fatal Occupational Injuries (CFOI)
- U.S. Occupational Safety and Health Administration (OSHA)
- Local and national news organizations
- Local and regional COSH groups, labor unions and partner organizations.
Documenting Preventable Deaths: New U.S. Worker Fatality Database Available on April 28th, 2015
On April 28th 2015, in observance of Workers’ Memorial Day, National COSH will release the U.S. Worker Fatality Database, a catalog of publicly available information about workplace fatalities in the United States in 2014. The database is a joint effort between National COSH, the AFL-CIO, the Center for Construction Research and Training, Fe Y Justicia, Global Worker Watch, United Support and Memorial for Workplace Fatalities (USMWF), the Massachusetts Coalition for Occupational Safety and Health (MassCOSH) and Celeste Monforton, DrPH and MPH, George Washington University.
The U.S. Worker Fatality Database is the most comprehensive listing ever created about women and men who have lost their lives on the job in the United States. It combines government reports, news accounts and information provided by families. It features specific data – including name of the deceased, employer, circumstances of death, and links to news reports – about some 1,500 deaths on the job in 2014.
Although this is the largest gathering of public information on workplace fatalities ever attempted in the United States, this initial effort is likely to cover less than one-third of all traumatic workplace fatalities in 2014. The total death count, as measured by the U.S. Bureau of Labor Statistics (BLS) has averaged over 4,500 deaths per year in each of the last several years.
The U.S. Worker Fatality Database is a collaborative and community-based research effort, driven by the lack of
information currently available from governmental sources. During the last several years, a growing number of
surviving family members, joined by labor and community activists, have expanded Workers’ Memorial Day to an
entire week of activities remembering lost loved ones and focusing attention on how we can prevent additional
fatalities.
As activists around the country seek information about workers killed in their state, region or locality, we find that important details are available in some cases but not others, with no logical explanation for the inconsistencies. Why should it be so hard for the public to know who was killed on the job and the basic facts of what happened?
National COSH identified this problem in 2012, calling for a national collection of workplace fatalities to be available in the public domain. At present, the largest collection of information about workplace fatalities is the annual Census of Fatal Occupational Injuries (CFOI), collected by the Bureau of Labor Statistics. The agency releases an annual report based on federal, state and independent data sources. The CFOI generally features an accounting of workplace fatalities from a calendar year two years prior to final release of the report. (The final CFOI released in the spring of 2015, for example, will cover fatalities in calendar year 2013.) The CFOI includes summary data only, with specific information about the names of workers and employers typically withheld as confidential.
The U.S. Mine Safety and Health Administration, by contrast, has a long-standing policy of posting workplace fatalities on their website within days of being notified about a fatality. The report typically includes the name of the worker who died, his or her employer and a short description of the incident. The U.S. Fire Administration, a division of the Department of Homeland Security, also publishes information about on-duty career and volunteer firefighter fatalities. These public postings help us remember those who have died, and also provide crucial information that can help protect others who are exposed to ongoing occupational hazards.
With release of the U.S. Worker Fatality Database in 2015, we will have accounted for about one-third of the workers who died on the job in 2014 from traumatic causes. At present, unfortunately, there is no tracking system for the greater number of workers each year – estimated at more than 50,000 – who succumb to work-related illnesses from exposure to long-term occupational hazards.
National COSH and our partner organizations will continue to push for release of additional public information about thousands of others who died and remain anonymous. We know from experience that getting this information out in the public is one of the most important ways to reduce future fatalities. The names and photos of workers who have lost their lives remind all of us about the need for greater prevention efforts and accountability in the workplace.
Infographics
DYING ON THE JOB
FACES OF WORKPLACE FATALITIES
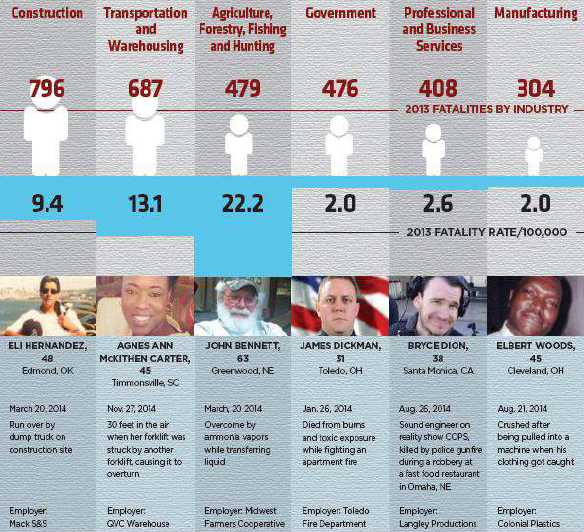
Fatalities and fatality rates based on preliminary data for 2013, U.S. Bureau of Labor Statistics
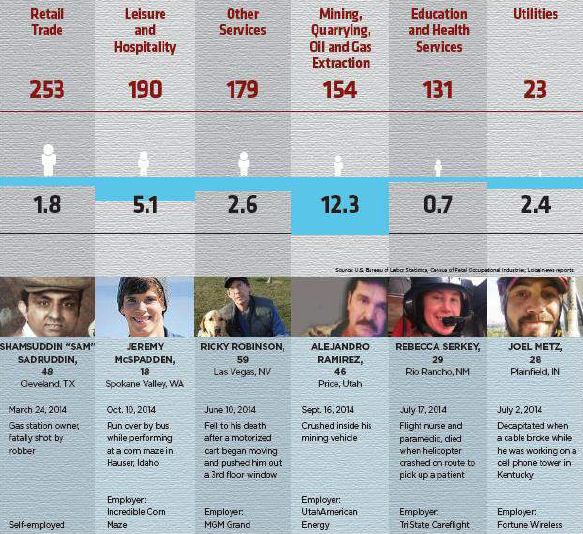
Fatalities and fatality rates based on preliminary data for 2013, U.S. Bureau of Labor Statistics
54,000 DEATHS, 2 PROSECUTIONS
More than 54,000 deaths from workplace injuries and illnesses. 2 Prosecitions of company executives in 2014, for actions that led to death in the workplace.
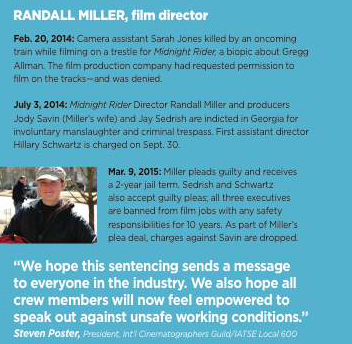
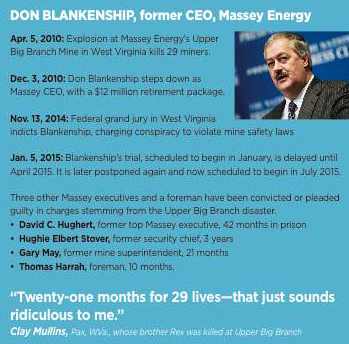
PROVEN APPROACHES TO PREVENTION
For each of these workplace hazards, there are tested and proven engineering controls, safety procedures and training protocols which can reduce exposure to dangerous conditions and lower the risk of illness, injury and death.
Workplace Hazard | Prevention Strategy | FLAWED SAFETY PROGRAMS AND DISINCENTIVES TO REPORT INJURIES |
|
---|---|
TRANSPORTATION INCIDENTS |
|
CONTACT WITH OBJECTS AND EQUIPMENT |
|
FALLS TO A LOWER LEVEL |
|
WORKPLACE VIOLENCE |
|
EXPOSURE TO HARMFUL SUBSTANCES AND ENVIRONMENTS |
|
FIRES AND EXPLOSIONS |
|
Case Studies
ERIK DEIGHTON, 23. Auto parts worker, MichiganJOHN EDD DUNNIVANT, 57. Autoworker, Georgia
FABIAN MARTINEZ, 21. Oilfield worker, New Mexico
LADONTE MCCRUDER, 31. Plumber, Alabama
AGNES ANN MCKITHEN CARTER, 45.Warehouse worker, South Carolina
JOEL METZ, 28. Tower climber, Indiana
JUAN CARLOS REYES, 35. Construction worker, Texas
ERIK DEIGHTON, 23
AUTO PARTS WORKER, SHELBY TOWNSHIP, MICHIGAN
CRUSHED TO DEATH IN A STAMPING MACHINE
Erik Deighton worked a 12-hour shift starting at midnights at Colonial Plastics, a factory in Shelby Township, Michigan that supplies parts to auto, aerospace and appliance manufacturers. At about 6 a.m. on March 5, 2014, Deighton was operating a stamping machine when it became jammed. He was trying to clear the obstruction when “the machine cycled to stamp a part and crushed the victim,” according to a news release from the Shelby Township Police Department.
Deighton’s tragic death was “truly an accident,” Township Police Captain Steven Stanbury told Plastics News.
Stanbury’s comment reflects the fact that in most cases, local law enforcement agencies are not trained to recognize work-related safety issues – including preventable tragedies that are not “accidents” in any meaningful sense of the word.
In this case, Capt. Stanbury’s actual description of the event shows it was entirely preventable. The stamping press, officers said, was “a large machine with doors on two sides.”
“So even though the guy was leaning through an open door,” said Stanbury, “the machine thought both doors were closed and that’s why the guy on the other side couldn’t see him [the victim] and was able to start the machine or cycle it.”
A stamping press, slamming down tons of metal with brute force, can be incredibly dangerous. Accepted industry practice requires this equipment to be designed so that it cannot operate when a worker is inside or anywhere near the dangerous parts of the machine. If Colonial Plastics had invested in modern machine guarding technology, along with other safety precautions, the incident could not have taken place as described – and Erik Deighton would probably still be alive.
Michigan OSHA, after investigating the incident, charged Colonial Plastics with seven serious health and safety violations. The agency proposed a $20,850 penalty, which was eventually reduced to $8,400. Among other failings, the company didn’t provide proper training, lockout procedures or machine guarding.
Responding to an account of the incident at The Pump Handle, a leading blog on health and safety issues, Lauren Deighton posted a moving tribute to Erik:
“He was my brother, and one of the kindest, deepest souls on Earth. He was so creative. He drew, read, and sang at the top of his lungs. He was my mom and dad’s only son, and she worked so hard to make sure he graduated high school and was on the path to success. He got this job after having a misguided period in his youth where he, like other boys, was rowdy and challenged authority.”
“However, he finally was on the right track and working hard at a job that made decent money, which he was so proud of. He worked midnights, 12 hours straight, 5 to 6 days a week, and the factory he worked at was understaffed. His death was most certainly preventable. And now I and my family have to live out the rest of our lives without him. And truly, he was the only one who insisted upon making life joyful. I won’t ever forget him and I won’t ever forgive this.”
JOHN EDD DUNNIVANT, 57
AUTO WORKER, WEST POINT, GEORGIA. GRANDFATHER OF 12
CRUSHED TO DEATH IN AUTO PLANT
John Edd Dunnivant had worked at the KIA Motors West Point, Georgia plant since it
opened in 2009, giving over his days to the manufacture of Sorenta and Santa Fe
sport utility vehicles and Optima sedans. Little did he know that he would also give
his life.
The tragedy unfolded on the morning of Tuesday, October 7th, 2014. “According to
early incident reports written by first responders,” reports The LaGrange Daily News:
“Dunnivant was working in the metal stamping section of the plant when some
stacked metal framework stamping plates shifted, slid and fell on Dunnivant.”
It took two hours for a crane to arrive and pull the heavy metal plates off of him. Troup County Coroner Jeffrey Cook
found that Dunnivant died of asphyxiation. "His breath was cut off," Cook told The Columbus Ledger-Enquirer. "It's
called compression asphyxia due to the weight that was on him."
An OSHA investigation is still ongoing. Dunnivant is survived by his wife, a daughter, two stepchildren, and twelve
grandchildren.
BLS data shows that 312 workers died in the manufacturing industry in 2013.
Dunnivant’s death was the first inside the Kia plant since it began operations in 2009, but it is not the first fatality linked to the operations of the 2,200 acre, $1 billion facility, which now employs more than 3,000 people.
- Ollie Tate, a construction worker for subcontractor Superior Rigging & Erecting Co., was killed in January 2008, when a beam fell on his head while the Kia plant was under construction. OSHA found three serious health and safety violations and fined Superior Rigging $13,200 for failure to properly secure steel beams.
- Teresa Pickard worked on the welding line at Sewon America, a LaGrange, Georgia plant that makes chassis, body and trim parts for the West Point Kia plant. She died of an on-the-job heart attack in May 2013 after reports of excessive heat in the facility.
These deaths, like most workplace fatalities, are preventable. Steel beams, plates and other heavy equipment can be secured to prevent shifting, falling and other events that can endanger the lives of workers. Proper cooling, ventilation, rest breaks and regular access to fresh water can reduce the risk of heat exposure. Employees are safer on the job when they have a voice to advocate for improvements in their own working conditions. A Stanford Law School study of the mining industry, for instance, shows that fatalities and traumatic injuries decreased with unionization.
Both the West Point Kia plant and its Sewon supplier are non-union facilities. Prospective workers sued Kia in 2011, saying that applicants with union backgrounds had been systematically rejected for employment at the plant.
FABIAN MARTINEZ, 21
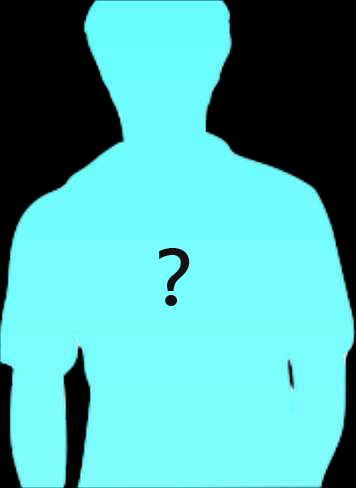
OIL FIELD WORKER, HOBBS, NEW MEXICO
PINNED BY A PIPE AND POISONED BY HYDROGEN SULFIDE IN A NEW MEXICO OILFIELD
It’s “among the most dangerous” industries in America, says the governor of North Dakota. Wall Street Journal reporter Alexandra Berzon documents 38 oil-field deaths from October through February of this year. “Nationwide, 663 workers in oil field-related industries were reported killed in the drilling and fracking boom from 2007 to 2012,” says the Houston Chronicle.
Workers in this industry are exposed to great risks to keep our homes and businesses supplied with reliable energy, yet they often seem invisible. Such is the case with Fabian Martinez of Hobbs, New Mexico, who died on July 30, 2014. He was working in an oilfield pit in nearby Artesia, cutting pipe and capping lines, when there was an explosion. His three co-workers managed to escape, but Fabian was pinned by the pipe, and succumbed to hydrogen sulfide gas.
OSHA’s “Hazard Alert” on hydrogen sulfide says the “three best practices to help prevent injury and death are: active monitoring for hydrogen-sulfide gas; good planning; and training programs for workers.”
Indeed, TV reporters found that Fabian’s employer “held a series of safety meetings”... the day after he died.
You will find no obituary for Fabian. No memorial. No remembrances on Facebook. After the initial reports of the accident on local New Mexico TV and in the press, there was no follow-up.
OSHA did pursue an investigation, finding Fabian’s employer – Diversified Oil Field Services – guilty of eight serious safety violations, fining the company $28,000.
Such fines, however, are not sufficient to rein in the hazards common in this deadly industry. The recent drop in oil prices has prompted widespread cost cutting, says the Journal, leading to “grueling 12-hour shifts for as many as 20 days in a row.”
According to the Chronicle, since OSHA is only required to investigate accidents that are fatal and/or require hospitalization, many unsafe practices continue until irrevocable tragedies occur.
The Chronicle article points out that in the hierarchy of oilfield work, it is the youngest workers that get assigned the most dangerous jobs. Fabian Martinez was 21 – too young to be exposed to such hazards, too young to make his mark on the world, and too young to die.
LADONTE MCCRUTER, 30
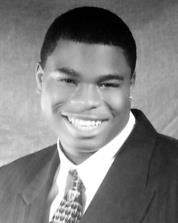
DAY LABORER, BIRMINGHAM, ALABAMA
WORKING IN AN UNPROTECTED TRENCH, SUFFOCATED WHEN IT COLLAPSED
LaDonte McCruter was a day laborer, known for his plumbing skills, described by those who
knew him as a “kind man with a quick smile.”
He died all too quickly on August 31, 2014, when working in a 12-foot trench at a
construction site in Birmingham, Alabama. McCruter, hired as a temporary worker by a
subcontractor, was working to connect the plumbing for a new home to a main city sewer
line. He was buried when the trench around him collapsed, leaving him covered in dirt and
unable to breathe. Rescuers spent six hours trying to save his life. But there was “too much
dirt to move and too little time,” according to a report from WCIV-TV.
Excavation is one of the most hazardous operations in the construction industry, claiming an average of two lives a
month, reports OSHA. Unstable walls can cave in suddenly, posing great risk to workers. OSHA safety regulations
require specific protections for any trench or excavation site deeper than five feet: either sloping of trench walls,
shoring up the trench with aluminum hydraulics or other supports, or shielding workers with a protective trench
box.
McCruter’s employers ignored these rules – and he lost his life as a result. Joshua Dailey, the subcontractor who
hired McCruter as a day laborer, was charged with willful and serious safety violations following an OSHA
investigation. Bates Construction, the prime contractor that hired Dailey, was charged with a serious violation.
The agency recommended fines of $53,800, and had harsh words for both companies. "Mr. McCruter's employers
knew they were placing him in mortal danger by not using cave-in protection,” said Ramona Morris, director of
OSHA's Birmingham Area Office in a March 5, 2015 press release. "His family is grieving the death of a loved one
because his employer willfully failed to protect him from this known hazard."
Temporary workers like McCruter are often assigned to work in hazardous conditions with little or no training.
“Temporary Work, Lasting Harm,” a 2013 investigation by ProPublica, analyzed millions of workers’ compensation
claims in five states and found that “tempts face a significantly greater risk of getting injured on the job than
permanent employees.”
The U.S. Bureau of Labor Statistics began tracking fatalities involving temporary or contract workers in 2011. In
2013, 749 temp workers died on the job, representing sixteen percent of all fatalities, an increase from 715
temp worker deaths reported in 2012.
AGNES ANN MCKITHEN CARTER, 45
WAREHOUSE WORKER, FLORENCE, SOUTH CAROLINA
DIES ON THANKSGIVING DAY WHEN HER FORKLIFT OVERTURNS
Agnes Ann McKithen Carter, a 45-year old warehouse worker, was assigned to work on Thanksgiving Day so that QVC could get a jump on pre-Black Friday sales. The company’s Florence, South Carolina facility is a busy place, shipping 1,000 packages an hour and 1.7 million in a year.
The popular home shopping network’s facility employs 900 people. McKithen Carter is no longer one of them. She was 30 feet in the air on her forklift, reaching for something overhead, when it was struck by another forklift.
According to a report by WPDE-TV in South Carolina, McKithen Carter's forklift overturned in the incident, which caused her to fall despite the fact she was wearing a safety harness.
She died later that day at the hospital.
The news reached her husband, Charles Carter, Jr., as he was preparing dinner for their first Thanksgiving together. The couple had only been married for eight months. “Never expected this,” Carter told WPDE.
“Like I said when she left that morning, it was our first Thanksgiving. You know and I'm sitting here looking at the clock and 2:45 never came. Not for us to start our first Thanksgiving. Never came. What did come was tragedy, heartbreak, disappointment.”
In addition to her husband, McKithen Carter is survived by her four children; her parents James and Ruth; her two grandchildren; six remaining sisters; five brothers; two godchildren; and one of her grandparents.
Florence County Coroner Keith von Lutcken and the South Carolina Occupational Safety and Health Administration (OSHA) are investigating the tragedy.
Transportation and warehousing are among the most dangerous industries in the United States, with a fatality rate of 14 deaths for every 100,000 workers in 2013 – 733 deaths overall. One hundred people die each year while operating forklifts, according to federal OSHA. “Forklift turnovers,” the agency says, “account for a significant percentage of these fatalities.”
JOEL METZ, 28
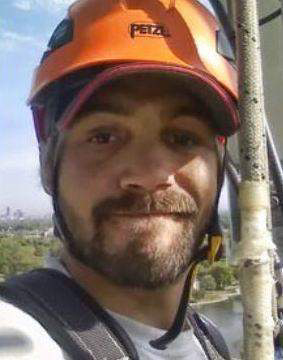
TOWER CLIMBER, INDIANAPOLIS, INDIANA
FATHER OF THREE, DECAPITATED BY A CABLE WHILE WORKING 240 FEET ABOVE GROUND
On July 2, 2014, Joel Metz and three co-workers were suspended hundreds of feet in the air, installing new antennae on a Verizon cell phone tower.
Suddenly, they heard a loud pop – the sound of a cable breaking on the winch assembly being used to haul new equipment onto the tower. Whipping through the air, the cable decapitated Metz and sliced off his arm.
Metz died instantly, but his body was left hanging in his safety harness for nearly eight hours before a rescue crew was able to bring him down. At the age of 28, he left behind a fiancé and three sons who were aged 5, 7, and 8 at the time of their father’s death.
Although he was working on a Verizon cell phone tower, Metz was employed by a company called Fortune Wireless when he was killed. Following Metz’ death, an OSHA investigation found three serious health and safety violations and proposed fines of $14,700 against Fortune Wireless.
Thirteen tower climbers died on the job in 2013, and fifteen more were killed in 2014, out of an estimated workforce of 10,000 people. For 2013, that’s a rate of 130 deaths per 100,000 workers – nearly 42 times the average fatality rate for U.S. workers that same year. By comparison, the overall construction industry had a fatality rate of 9.7 workers per 100,000 workers in 2013. Working on cell phone towers is 13 times more dangerous than a typical construction job.
CUTTING CORNERS TO MEET GROWING DEMAND: There are now more active cell phones in the United States than people, and growing demand for service has led to an explosion in tower construction and maintenance. The work is rarely done by major carriers like Verizon, ATT or Sprint, but instead contracted and sub-contracted to operators who do not observe basic safety precautions.
Despite high demand for their work, tower climbers are typically paid just $10 to $11 an hour, according to a 2012 investigative report by ProPublica and Frontline, “yet subcontracting companies demand they pay for their own safety gear, deducting money from their paychecks.” Forcing workers to pay for their own protective gear is, in fact, prohibited under U.S. law. The OSH Act requires employers to provide and pay for equipment needed to keep workers safe on the job.
“We found that in accident after accident, deadly missteps often resulted because climbers were shoddily equipped or received little training before being sent up hundreds of feet,” reported ProPublica. “To satisfy demands from carriers or large contractors, tower hands sometimes worked overnight or in dangerous conditions.”
Wally Reardon, a former climber who now heads the Workers at Heights Safety & Health Initiative, (WHSHI) told The Pump Handle that “layers of contractors” in the industry are a serious problem, clouding which company has ultimate responsibility for providing proper safety, training and equipment.
“More communication tower workers were killed in 2013 than in the previous two years combined, “ stated U.S. OSHA in a February, 2014 press release. “Every one of those deaths was preventable.” More than 75 percent of cell climber deaths, according to WHSHI, result from “free climbing,” when workers are on a job site without proper fall protection. A worker who is securely tied to the structure he or she is climbing cannot fall to the ground. Sadly, according to Workers at Heights, “one of the most popular ways for employers to speedup the pace of work is to ignore – or encourage – foremen and other employers who free climb.”
JUAN CARLOS REYES, 35
CONSTRUCTION WORKER, BROWNSVILLE, TEXAS
FATHER OF THREE DIES AFTER FALLING FOUR STORIES AT A CONSTRUCTION SITE
Saturday, May 24, 2014 was Juan Carlos Reyes' last, fatal, day at work. The 35-yearold construction worker was found “unresponsive and not breathing” after he fell four stories at the site of a Marriott Hotel under construction in Harlingen, Texas.
According to a report from KGBT-TV in Harlingen, Reyes was trying to put wire spools inside the fourth floor of the building under construction, when the platform he was standing on became unstable.
Reyes, who lived in Brownsville, Texas was pronounced dead at the scene. He is survived his wife, Teresa Layton Reyes, and three children: Arely Suzette, Giovana Yamilet, and Juan Carlos, Jr.
Following the tragedy, OSHA's Corpus Christie, Texas, office investigated and found that Reyes' employer – Angel AAA Electric – had committed six violations, five “serious” and one “willful.” The agency recommended $36,400 in fines for failure to ensure that the scaffolding Reyes fell from was erected by a qualified person and for failure to put a fall arrest system in place.
“Falls to a lower level” are one of the most common causes of worker fatalities in the United States, accounting for 574 deaths in 2013, or 13 percent of the total. It is also a hazard that can be addressed with a well-known and effective prevention strategy. Had Reyes been protected by a fall prevention program – which should include secure ladders and scaffolds, guard rails, safety harnesses and proper training – he would still be alive.
Hispanic workers are particularly vulnerable to risks in the workplace. According to data from the U.S. Bureau of Labor Statistics, 817 Hispanic or Latino workers died on the job in 2013, the highest figure recorded since 2008. On-the-job deaths for Hispanic or Latino workers increased by nine percent from 2012, while fatalities decreased for white, African American and Asian workers.
Construction work is one of the most dangerous industries in the United States, with a fatality rate of 9.7 deaths for every 100,000 workers in 2013.
Construction sites and other workplaces in Texas are under the jurisdiction of federal OSHA, but U.S. OSHA had just ninety-eight inspectors in fiscal year 2014 to cover the entire state of Texas: 268,580 square miles, more than 10 million workers and over 500,000 employers. The AFL-CIO estimates it would take this team of less than 100 people approximately 136 years to perform just one inspection of every workplace in Texas. These inspections would be in addition to responding to workplace-related injuries, illnesses, and deaths like the tragic – and preventable – loss of Juan Carlos Reyes.
NATIONAL COSH POLICY PLATFORM
Our policy platform calls for systemic reforms in workplace safety and health, as well as hazard-specific improvements that will enhance worker health and safety protections not only under OSHA, but through other policy reforms as well. In particular, employers can and should do more to carry out their legal responsibility to provide a safe and healthy workplace; companies that fail to do so must be held accountable.
The National COSH policy platform will benefit a diverse population of workers: from low wage unorganized workers to union workers, from blue-collar workers to professionals, from temporary to permanent workers, and from young to seasoned workers.
POLICIES AFFECTING ALL WORKERS
EFFECTIVE STATE OSHA ENFORCEMENT
Federal OSHA and worker advocates should hold state OSHA programs to strict standards to ensure that
their enforcement efforts are at least as effective as federal OSHA, as required by the federal OSH Act. Many
of these programs have failed to live up to this promise and must be held accountable.
SERIOUS PROTECTIONS FOR WHISTLEBLOWERS
Several Government Accountability Office (GAO) audits have found that OSHA’s Whistleblower Protection program has failed to achieve its goal. OSHA must take action to ensure that workers who speak up for job safety and health are protected from retaliation. State legislatures should also pass strong whistleblower laws that provide additional protections for workers.
ADOPT LONG OVERDUE PROTECTIONS FROM SILICA DUST
A proposed rule on limiting worker exposure to deadly silica dust has languished for years in the standardsetting process. This standard should be adopted to ensure that no more workers die of silica-related disease.
ENHANCE PENALTIES FOR VIOLATIONS OF OSH LAWS
Currently, the OSH Act allows only civil penalties, and they are so low as to make them an ineffective deterrent to unsafe working conditions. Under the OSH Act, even criminally negligent behavior by employers can only result in a misdemeanor prosecution. Penalties and administrative procedures must be strengthened to ensure that employers are adequately penalized for putting workers in harm’s way. State and federal prosecutors should aggressively pursue criminal indictments when evidence shows willful intent by employers whose actions – or inaction – caused death or serious injury to workers. State legislatures and the U.S. Congress should create a legal framework to hold corporations and executives accountable for criminal violations of health and safety laws, and eliminate barriers to successful prosecutions.
REDUCE OR ELIMINATE WIDESPREAD USE OF TOXIC CHEMICALS
Advance legislation to establish a comprehensive chemicals policy grounded in the fundamental principles of precaution, substituting safer alternatives and right-to-know. This will help ensure protection of workers, their families and communities and natural ecosystems.
PROVIDE PUBLIC ACCESS TO NATIONAL WORKER FATALITY DATA
Each death on the job is a horrible tragedy, but one that is preventable. A first step in preventing future fatalities is to understand the causes and circumstances surrounding previous ones. The U.S. Department of Labor should compile a complete listing of workplace fatality cases, with all relevant information, including names of workers on a publicly available website.
PROTECT AGAINST WORKPLACE VIOLENCE
Nearly two million American workers report having been victims of workplace violence each year. Workplace Violence Prevention Programs should be required in every worksite, including written protocols, training and protections to safeguard against, prepare for and reduce the risk of workplace violence.
RESPONSIBLE CONTRACTORS ON PUBLIC WORKS PROJECTS
Federal agencies and state and local governments should adopt policies for the awarding of contracts for public works projects to ensure that only responsible employers with effective safety and health programs are awarded contracts.
ENHANCE AND PROTECT BENEFITS UNDER STATE WORKERS’ COMPENSATION LAWS
The U.S. Workers’ Compensation system must return to its original mission: providing medical care and income support to workers injured on the job. After years of unjustified attacks by corporate special interests, payments have been arbitrarily slashed, workers are discouraged or denied benefits, and less than half of all injured workers are receiving Workers' Compensation in any form. A state-by-state and national policy framework is required to insure prompt and certain payment to injured workers and their families. Decisions about medical care must be determined by workers and their health care providers, without interference from employers or insurance companies.
CLIMATE CHANGE
Climate change will have profound implications for the occupational health and safety of many workers and the variety of potential hazards are staggering. The Centers for Disease Control (CDC) must incorporate occupational health and safety issues in its assessment of potential burdens of disease and other outcomes resulting from the impacts of short and long-range climate projections.
POLICIES AFFECTING THE MOST VULNERABLE WORKERS
EQUAL HEALTH AND SAFETY PROTECTIONS FOR ALL WORKERS
No matter their age, race, religion or immigrant status, all workers have the right to a safe and healthy workplace. As the data and case studies presented above show, immigrant and minority workers, contingent/temporary workers and young workers are particularly vulnerable to serious workplace hazards. Protecting all workers equally will take new initiatives:
In addition, Congress must pass meaningful immigration reform to bring undocumented workers out of the shadows and ensure they can exercise their rights to a safe and healthy workplace.
OCCUPATION-SPECIFIC POLICIES
SAFE PATIENT HANDLING
A major source of injury to healthcare and personal care workers is musculoskeletal disorders (MSDs) such patient handling with safer methods using equipment to lift, transfer and reposition health care patients and residents.
MAKING WORK SAFER
Local COSH groups advocate, research, train, and organize so workers can exercise their right to a safe and healthy workplace. Below, recent activities across the country aimed at improving health and safety conditions in U.S. workplaces.
Central NY Occupational Health Clinic: Issues "Low Wage Work in Syracuse" report, finding that hazardous conditions and exposures are commonplace among low-wage workers. Injured workers, the study finds, have difficulty accessing healh care through workers' compensation.
ConnectiCOSH: Co-sponsors a conference on workplace assault and violence with Connecticut AFL-CIO in Jan, 2015. Response was overwhelming and a second program is added in April 2015. Working with U.S. Sen. Chris Murphy, urging OSHA to issue standard on workplace violence.
Houston Area COSH: provides health and safety training to more than 300 workers, focused on preventing and reporting workplace hazards. Also provides training on hazards of silica dust, and sends two workers to Washington DC to testify at OSHA hearings on a new silica standard.
Knoxville Area WMD Committee: Explores public policy reforms to ensure that only high-road contractors with good safety records and strong injury and illness prevention programs are awarded contracts for public works projects.
MassCOSH: Wins new legislation in 2014 providing Massachusetts state employees with health and safety protections as good or better than federal OSHA standards. Teens Lead@Work, innovative peer education program, trains 500+ young workers in prevention of workplace violence in 5 major cities.
Mid-State Education and Service Foundation: Working with Workers Center of Central New York and Worker Justice Center, forms a committee of immigrant dairy farmworkers to address health and safety in agriculture. Focus includes education, workers’ comp, and OSHA inspections.
NENYCOSH: Partners with unions and Trial Lawyers Association to defend the Scaffold Law, which offers important protections to NY state construction workers.
NHCOSH: Offers specialized training to emergency responders and workers who respond to hazardous material emregencies and clean up hazardous waste sites. Works in collaboration with The New England Consortium (TNEC).
NJWEC: Issues 2014 report "Danger in the Dark," showing that stae of NJ has failed to make emergency response plans available to the public. This puts workers and communities at risk in case of a chemical plant or oil train fire, explosion or other unplanned release of toxic substances.
NYCOSH: Launches "New York Healthy Nail Salons Coalition" in cooporation with Adhikaar, an organization representing salon workers. Campaign aims to enforce existing safety laws and win better protections for industry workers. NYCOSH also responds to Ebola crisis with bilingual fact sheets, and advocates for better preparedness by city, state and private sector.
PhilPOSH: Establishes "Criminal Prosecution" Committee, following weak citations and low fines issued by OSHA after the death of a PA tempworker on his first day on the job. Working to hold employers accountable in fatality cases with evidence of willful intent.
RICOSH: Offers "Danger in Combustible Dusts" training to help workers recognize and respond to hazards of fine particles that can create an explosion hazard, especially in confined areas. Works to develop climate change planks directly related to worker health and safety.
SoCalCOSH: Wins tougher regulations at CAL/OSHA, improving the Heat Illness Prevention Standard for workers exposed to extreme heat. Advocates for California SafeCare Standard to address workplace violence, and organizes to support improved safety for airport workers at LAX and ironworkers in LA construction industry.
SoFLCOSH: Launches new worker health and safety training program to assist low-wage workers, including, immigrants, minorities, temps and young workers.
WesternMassCOSH: Helps create Pioneer Valley Worker Center for low-wage and immigrant workers in Western Mass, especially those involved in planting harvest and processing for the area's growing local food movement.
WNYCOSH: Wins new funding for training and advocacy at Western New York Workers Center, focusing on worker organizing, wage theft, and safer working conditions.
WisCOSH: Advocates for stricter limits on exposure to silica at OSHA hearing in Washington, DC. Workers are exposed to the hazardous dust at Wisconsin foundries.
Worksafe: Wins passage of landmark bill for temporary workers in California, holding primary employers accountable for wage theft and safety violations by staffing and temp agencies. Also wins legislation speeding up abatement of serious workplace hazards, and offering better, more timely information to workers exposed to toxic chemicals.
Wyoming COSH: Calls for tougher penalties for companies with serious and willful violations fo health and safety laws, including higher fines if a worker dies on the job.
PRODUCED BY: National COSH
April 2015
Written by: Roger Kerson, Mary Vogel, Peter Dooley, Jessica Martinez, David Isaacson
OUR MISSION
COSH Network.orgThe National Council for Occupational Safety and Health is dedicated to promoting safe and healthy working conditions for all working people, through education, training, organizing and advocacy. Our belief that almost all
work-related injuries and illnesses are preventable motivates us to encourage workers to take action to protect
their safety and health, promote protection from retaliation under job safety laws, and provide quality
information and training about hazards on the job and workers’ rights.
WORKERS' MEMORIAL WEEK: APRIL 25 TO MAY 2, 2015
This report is released to mark Workers’ Memorial Week, a remembrance of those who have lost their lives at work. The event is observed nationwide – and around the world – by surviving family members as well as health and safety activists in workplaces and communities. It coincides with the anniversary of the U.S. Occupational Safety and Health Act, which took effect on April 28, 1971.