Summary Statement
The American Pipeline Contractors Association developed this guidance document about safely handling vacuum lift systems.
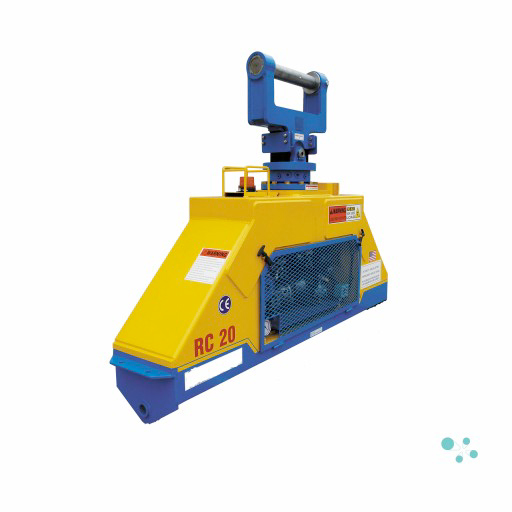
Introduction
Vacuum lifters have become widely used for lifting materials at construction sites, and during work involving pipelines, concrete road barriers projects and horizontal directional drilling (HDD).
Safety and efficiency are two of the main reasons for using vacuum lifters. Not only does this equipment allow for a reduction in the number of personnel required to move piping, it minimizes the risk or injury to ground personnel. Materials are moved safely and stacked without extra personnel in the in unloading area. Further, the use of slings, pipe hooks, pipe forks and pipe tongs are eliminated.
This fact sheet provides best practice guidelines for personnel during pre‐operation, operation and post operation of vacuum lifts. A sample “pre‐ operation” safety checklist is provided at the end of this document.
Under the Occupational safety and Health Act, employers are responsible for providing a safe and healthy workplace. In doing so, employers should ensure the following safety measures are taken.
Pre Operation:
- All personnel involved in the operation and use of vacuum lift systems are trained before use.
- A discussion between supervisory personnel and operators takes place to allow for pre‐planning of the work to be done, including operation of the vacuum lifting system. All personnel should have a thorough understanding of the job site.
- The equipment available for use at the jobsite is appropriately sized and rated for the job.
- A job safety analysis (JSA) is conducted to determine individual job responsibilities and all related safety concerns. Potential hazards must be identified and addressed.
- Operators read and understand the operator’s manual prior to equipment use. Keep the operator’s manual with the equipment at all times so it is available to the personnel operating the vacuum‐ lifting system.
- Locate all overhead lines, and maintain the designated minimum clearance distance found in OSHA’S regulations at 29 CFR 1926.1408. Always use a spotter.
- All maintenance and inspections, as indicated in the operator’s manual have been performed and are up to date. Only qualified individuals are authorized to service the equipment, including pad replacement.
- Remove damaged or defective equipment from service.
- Have a portable fire extinguisher that is fully charged and available for use. Make sure all designated personnel are trained on its proper use.
- Operators and ground personnel establish the designated method of communication before starting work.
- Personnel are supplied and trained on the appropriate personal protective equipment (PPE) as required for the task, such as hard hats, safety glasses, reflective vest, safety‐toed shoes, gloves, hearing protection and protective clothing.
- Make sure all warning labels are legible. If any are missing or illegible, replace them prior to the operation of the equipment.
- Always turn the fuel shut‐off valve to the “OFF” position before transporting or storing the unit.
- Before starting the unit:
- Securely attach the equipment to the cradle of the lifter with the specified hardware.
- Connect hydraulic hoses, adjust the rotation speed, rotate lifter, and attach the vacuum pad.
- Visually inspect the rods and keeper pins between the shoe and the vacu‐tron for any excessive wearing.
- Once the unit is started:
- Make sure all of the lifter’s safety warning devices are working properly including the operation lights and alarms.
- Visually inspect all vacuum gauges to ensure they are intact and functional.
- Visually inspect the vacuum seals at the beginning and middle of the shift and after any extended breaks.
- Make sure the wireless remote is operating properly and have spare batteries easily accessible.
- It is important to have the Emergency Hard‐wire operator nearby in case the wireless remote fails.
- Secure the wireless controller to the console or side glass with Velcro or a lanyard attached to the remote for wearing around the operator’s neck to prevent any unintentional movement of the load.
During Operation:
- Keep all unnecessary personnel out of the work area which includes the operational swing radius of the equipment and load.
- Do not exceed the specidied lifting capacity of the pad or machine. Note: Pad lift capacity may not be the same as the vacuum lifter capacity.
- Properly position the vacuum pad, engage the vacuum and lift, lower and rotate slowly. Keep loads low and lift pipes near their center.
- If at any time the vacuum lifter system malfunctions, make sure to switch the unit to the "OFF" position immediately and secure it from restarting. The job site supervisor must determine the next appropriate course of action.
Post Operation:
- Shut off the engine and secure it for storage and transport. Reference the operator's manual and follow manufacturer's guidelines for the appropriate sequence of steps.
- Transport the unit to the storage site and unhook it from the equipment used to operate the lifter.
- When applicable, utlize forklift pockets when moving the lifter to and from storage with a forklift.
Under the Occupational Safety and Health Act, employers are responsible for providing a safe and healthy workplace and workers have rights. OSHA can help answer questions or concerns from employers and workers. OSHA's On-site Consultation Program offers free and confidential advice to small and medium-sized businesses, with priority given to high-hazard worksites. For more information, contact your regional or area OSHA office, call 1-800-321-OSHA (6742), or visit www.osha.gov.
Vacuum Lifter Checklist
Submit Report to Division Equipment Coordinator
Operator Name: |
|
---|---|
Equipment Model: | |
Equipment Number: | |
Job #: |
Key: Checked box = Checked & OK X = Checked & needs attention C = Changed A = Added N = Does not apply to this equipment |
Date | |||||||||||||
---|---|---|---|---|---|---|---|---|---|---|---|---|---|
Hours/Miles | |||||||||||||
Grease Entire Machine | |||||||||||||
Inspect for Leaks | |||||||||||||
Check Hoses | |||||||||||||
Check Vacuum Pump Oil Level | |||||||||||||
Check Vacuum Filter | |||||||||||||
Check for Cracks on Suction Pad | |||||||||||||
Check Suction Pad Sealer | |||||||||||||
Drain Fuel Water Trap | |||||||||||||
Check Hydraulic Gauges | |||||||||||||
Check Control Box and Cable | |||||||||||||
Check All Bolts | |||||||||||||
Check Audible Alarm Operation | |||||||||||||
Check Visual Alarm Operation | |||||||||||||
Check Engine Oil | |||||||||||||
Check Engine Air Filter | |||||||||||||
Check Frame for Cracks |
Call the Division Equipment Coordinator if the equipment requires immediate attention.
Disclaimer
Through the OSHA and American Pipeline Contractors Association (APCA) Alliance, APCA developed this best practices document for informational puposes only. It does not necessarily reflect the official views of OSHA or the U.S. Department of Labor. 07/15
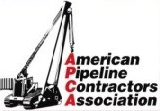
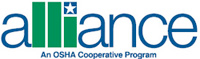