Kentucky FACE Report: Construction Laborer Killed in Trench Collapse while Taking Grade Measurements
-
Fatality Assessment and Control Evaluation (FACE) Program Reports
The National Institute for Occupational Safety and Health’s (NIOSH) Fatality Assessment and Control Evaluation (FACE) Program and State FACE Programs study fatal workplace injuries and prepare reports with recommendations to prevent similar injuries. The following are links to all of the items in this collection:
Documents
- Kentucky FACE Report: Commercial Roofer Falls 30 Feet Through a Skylight While Installing Roof Insulation
- Fatal Occupational Injuries in Massachusetts 2008-2013
- Fatality Assessment & Control Evaluation (FACE) Program
- Washington FACE Report: Glazier Foreman Falls From Stepladder
- Preventing Construction Falls Toolkit
- Hazard Alert: Pedestrian Workers Killed by Forklifts
- Keep Employees in Motor Vehicles Safe
- New York FACE Brochure
- Washington FACE Report: Construction Laborer Falls When Ladder Breaks
- Washington FACE Report: Pipelayer Dies when Trench Wall Collapses
- Washington FACE Report: Carpenter Falls 60 Feet from Bridge Concrete Form
- Washington FACE Report: Foreman and Laborer Fall when Aerial Lift Struck by Vehicle
- Washington FACE Report: Framer Falls 18 Feet while Sheathing Roof
- New York FACE Report: Mechanic Electrocuted when a Mobile Light Tower Contacted Powerline
- New York FACE Report: Two Construction Workers Fatally Crushed when Cement Formwork Collapsed
- Kentucky FACE Report: Construction Laborer Killed in Trench Collapse while Taking Grade Measurements
- California FACE Report: A Heating, Ventilaton and Air Conditioning (HVAC) Contractor Dies when He Falls through a Skylight
- Massachusetts FACE Report: Carpenter Fatally Injured after Falling from an Extension Ladder
- Massachusetts FACE Report: Laborer Fatally Injured after Falling from a Home under Construction
- Oregon FACE Report: Worker Falls When Ladder Slips
- Michigan FACE Information Sheet: Look for Mobile Equipment Blind Spots
- Oregon FACE Report: Collapsed roof trusses kill carpenter foreman
- Washington FACE Report: Roofer Falls 19 Feet from Roof
- Hazard Alert: Plan. Provide. Train. Prevent Fall Injuries & Deaths
- Kentucky FACE Report: 19-Year-Old Construction Laborer Crushed in Trench Collapse While Laying Sewage Pipe
- Kentucky FACE Report: Construction Flagger Struck and Killed in Two-Lane Highway Work Zone
- Kentucky FACE Report:Temporary Electrician Helper Steps into Unguarded Elevator Shaft and Dies
- Fatality Narrative: Roofing Contractor Falls 25 Feet From Church Roof
- Kentucky FACE Report: Construction Siding Subcontractor Installer Killed when Oversized Scaffolding Platform Destabilized and Telescopic Forklift Overturned
- NIOSH FACE Report - Maintenance Worker Struck by Forklift Carriage—Tennessee
- Kentucky Hazard Alert: Roofing and Construction Workers Killed Due to High Winds
- Poster: Secure it to move it!
- Oregon FACE Report: Crane Operator Killed By Falling Steel Beam
- New Jersey FACE Report: Mechanic Dies After Being Crushed Under Electrical Cabinet
- New Jersey FACE Report: Plant Manager Crushed to Death Under Fallen Pile of Steel Beams
- NIOSH FACE Report: Hispanic worker falls from residential roof
- Oregon FACE Report: Construction worker died after falling 20-25 feet from a pump-jack scaffold
- FACE Fact Sheet: Prevent Construction Falls from Roofs, Ladders, and Scaffolds
- Construction Fatality Narrative: Roofer Falls 18 Feet from Wet House Roof
- Construction Worker Killed when Trench Collapsed, Oregon
- A Tree Trimmer is Electrocuted While Trimming a Palm Tree
- A Tree Feller Dies When Struck By a Tree Limb While Felling a Fire-Damaged Tree
- Concrete Finisher Electrocuted When Bull Float Contacted an Energized Power Line
- Warehouse Worker Crushed by Forks of Laser Guided Vehicle
Summary Statement
On Wednesday, May 4, 2016 a 22-year-old male construction laborer was assisting an excavator operator who was digging a 13.4 ft. section of a trench along a two-lane roadway . At approximately 9:30 am, the victim entered the trench, which was lacking proper cave-in protection, by running down into it to take grade measurements as instructed by the excavator operator. As the victim was taking measurements, the excavator operator notice d the soil shifting on the vertical trench wall, and yelled for the victim to get out. The victim tried to jump out of the trench to escape but was buried beneath the collapsing soil.
December 8, 2017
Report No. 16KY017
Release Date: 1/17/2016
CASE SUMMARY
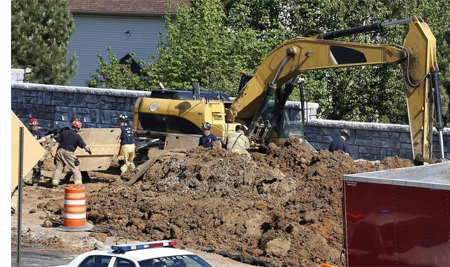
On Wednesday, May 4, 2016 a 22-year-old male construction laborer (victim) was assisting an excavator operator who was digging a 13.4 ft. section of a trench along a two-lane roadway. At approximately 9:30 am, the victim entered the trench, which was lacking proper cave-in protection, by running down into it, to take grade measurements as instructed by the excavator operator. As the victim was taking measurements, the excavator operator noticed the soil shifting on the vertical trench wall, and yelled for the victim to get out. The victim tried to jump out of the trench to escape but was buried beneath the collapsing soil.
Recommendations for prevention:
- Alternative methods for measuring trench grade and depth (that do not require an employee to enter the trench) should be utilized.
- Employers and site managers should ensure employees working in trenches five feet or more in depth are protected from cave-ins by adequate protection systems.
- Employers should ensure a competent person conducts soil testing and daily inspections of excavations, adjacent areas, and protective systems.
- Daily toolbox talks should be conducted which emphasize safety topics related to upcoming job tasks prior to allowing work to begin on the job site.
- Employers should intervene when unsafe acts on the jobsite are witnessed.
- Safe means of ingress and egress should be provided in all excavations prior to entry.
EMPLOYER
The construction company had been in business since 1992 and specialized in highway, street, and bridge construction, and also offered pipe laying services. The company was employed by the on-site general contractor to install sewer drainage pipe along a road. At the time of the incident, the company had 200 employees. The crew involved in this incident consisted of 10 construction employees and a superintendent.
SAFETY AND TRAINING PROGRAMS
The employer administered written safety programs to employees and provided evidence of extensive employee and manager safety training; refresher training was required on an annual basis. Documentation indicated that all employees received trench construction training. Hazard recognition training was administered to all employees; the most recent training on 2/23/16 was signed by the victim. Company policy required that site managers regularly provide daily toolbox talks that cover specific hazards associated with current daily job tasks; the pre-shift meeting on the day of the incident did not specifically address trench safety.
The company also provided a digital tool to educate on proper classification of soil in order to choose the appropriate trench protective system. Using the width, length, depth, and trench excavation time duration, the digital tool determines the amount of soil (tons) that could potentially cave in on workers and provides safety measures to be taken to protect workers from a collapse. The tool was available but not used on this particular job site.
VICTIM
The victim was a 22-year-old high school graduate and married father of three. He had been employed with the company since 3/18/14. His most recent training was 2/23/16.
INCIDENT SCENE
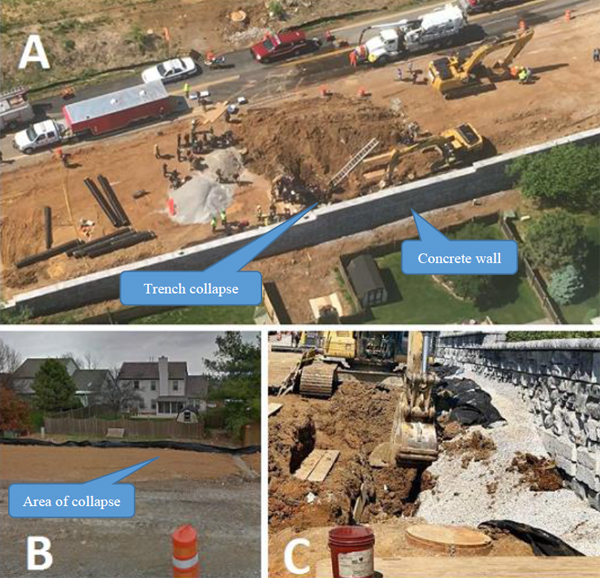
Figure 1. A) Aerial view of incident scene, B) photo of trench collapse location 4 months prior to incident,
C) section of trench that collapsed on victim; concrete wall.
The incident took place along a two-lane highway construction site where the two-lane highway was being widened. Running parallel at a distance of 45-50 feet from the road was a concrete wall that had been recently erected to separate the widened road from an adjacent residential neighborhood (Figure 1A). In preparation for a sewage pipeline to be laid, a trench measuring approximately 13.4 feet deep was being excavated parallel to the concrete wall (Figure 1C). The distance between the section of the trench that collapsed and the concrete wall was estimated to be approximately 4-5 feet.
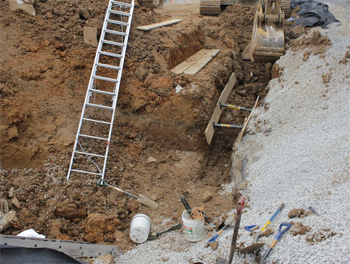
Figure 2. View looking down at the trench containing a mixture of
class B and C soils on the right side of the trench near the concrete
wall. Class B soil is observed on the opposite side of the trench.
The soil along the concrete wall facing the side of the trench was a mixture of class B and class C soil, along with #57 gravel backfilled along the wall foundation (figure 2). The soil surrounding the base of the concrete wall had previously been disturbed during the wall’s construction. The spoil pile was placed on the road-facing side of the trench at the required 2 foot minimum distance, however, this was still unsafe due to the pile’s size and the lack of a trench protection system.
WEATHER
May 4, 2016, had temperatures ranging from 54 to 63 degrees Fahrenheit. The temperature was approximately 57°F with cloudy skies at the time of the incident. The humidity was 74%, and the wind was blowing at 10.4 miles per hour from the west-southwest direction. Previous weather conditions included rain from 4/26/16 to 5/2/16. This could have contributed to the instability of the soil.
INVESTIGATION
On Wednesday, May 4, 2016, the Kentucky Fatality Assessment and Control Evaluation Program was made aware by local media coverage of a fatality involving a trench collapse. An immediate site visit and investigation was subsequently conducted.
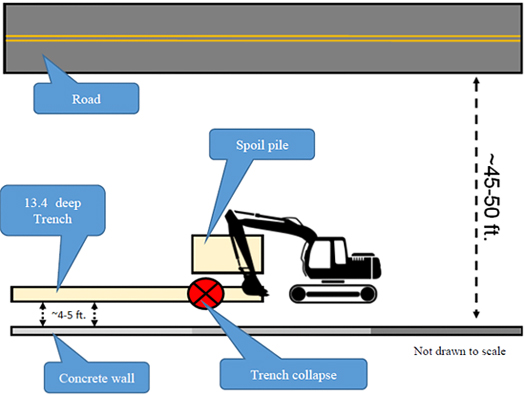
Figure 3. Diagram of incident scene
A local highway construction company had been hired as a sub-contractor to install an 18-inchdiameter storm sewer drainage pipe alongside a two-lane road. On the morning of the incident, the superintendent of the crew of 10 held a pre-work meeting to discuss the work to be done that day. The meeting included general safety awareness but did not specifically address proper trench safety and trench collapse hazards. The crew superintendent assigned the victim to assist the excavator operator in taking trench grade measurements. Soil testing was not performed prior to beginning work. No thorough inspection was conducted prior to beginning work; a trench box and/or shoring supports were not on site.
Work began at 6:30 am. Prior to the incident, the excavator broke down at approximately 7:00 am. Repairs were made on site and work commenced at 9:00 am. The excavator operator stated he was benching the street side of the trench similar to a previous job they had performed in the past. Photos of the scene suggest partial benching of the top of the trench (see figure 1C). The excavator operator also stated that the superintendent witnessed the victim enter and exit the unprotected trench multiple times that morning.
At approximately 9:30 am, the construction worker jumped into the trench to take grade measurements. The excavator operator observed the collapsing of the concrete wall facing side of the trench, and yelled to the construction worker to jump out. The construction worker did not have adequate time to escape, and the trench collapsed and buried him under dirt and gravel. Nearby employees jumped into the collapsing trench and tried to rescue the victim by digging. Emergency Medical Services were called at 9:38 am, and arrived at 9:47 am. A trench collapse special response unit from the fire department arrived to recover the construction worker. He was recovered at 10:52 am and was unresponsive. The coroner pronounced the victim dead at the scene at 10:52 am.
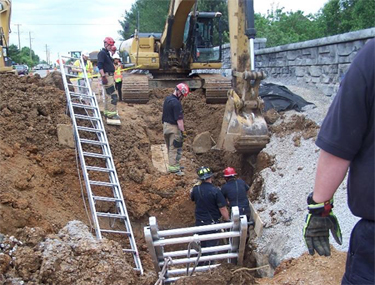
Figure 4. Trench collapse special response unit attempting to
recover the victim.
Lack of Trench Protective System
Performance of a soil test and an adequate trench protective system could have prevented this incident. OSHA requires that all workers in trenches 5 feet or more in depth be protected by sloping, shoring, or the use of shields. Since the soil was a mixture of class B and C soils, the soil should have been classified as class C soil. Trench excavation with class C soil requires sloping at 1½ H:1V (or 34°), meaning that the soil needed to be cut back 1½ ft. for every 1 ft. of depth (Figure 5). Given the proximity of the trench to the concrete wall, it was impossible to achieve the necessary slope on both sides of the trench. Since the concrete wall made conventional sloping techniques impossible, a trench box or shoring system should have been installed prior to allowing entry into the trench.
The excavation operator commented that he was to bench the road-facing side of the trench. However, OSHA requires that type C soil be sloped and never benched. Furthermore, sloping and benching techniques must be applied to both sides of the trench to be effective. The side of the trench facing the concrete wall was the side that was most unstable and suffered the fatal collapse.
OSHA Sloping Requirements | ||
---|---|---|
Soil Type | Slope | Angle (degrees) |
A | 3/4H:1V | 53° |
B | 1H:1V | 45° |
C | 1 1/2H:1V | 34° |
CAUSE OF DEATH
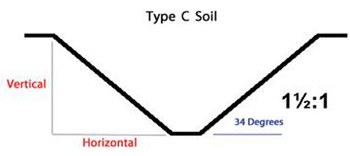
Figure 5. OSHA sloping requirements for type C soil.
This method would not have been possible due to the
proximity of the trench to the concrete wall.
The cause of death was traumatic asphyxia and smothering due to dirt trench collapse.
CONTRIBUTING FACTORS
This investigation identified the following factors that may have contributed to the fatality:
- Soil was not classified.
- The trench was entered without a protective support system in place.
- Ladders were not provided for trench egress and ingress.
- Company safety policies and procedures were not enforced.
- Trench safety was not specifically addressed during the pre-shift safety meeting.
RECOMMENDATIONS AND DISCUSSIONS
Recommendation #1: Alternative methods for measuring trench grade and depth (that do not require an employee to enter the trench) should be utilized.
Alternative methods for measuring trench grade and depth are available, including measuring rulers or poles, and excavator depth monitors. Excavator depth monitors allow the excavator operator to monitor the depth and grade from the safety of the operator’s cab. The monitors display highly accurate calculations and often eliminate the need for an operator assistant to check trench grade and/or depth. Modern excavator depth monitors are wireless, require minimal installation, and can be moved between machines.
Recommendation #2: Employers and site managers should ensure employees working in trenches five feet or more in depth are protected from cave-in by adequate protection systems.
Employees working in trenches of five feet or more in depth should be protected from cave-ins by adequate protection systems appropriate for the conditions in the trench, including sloping or benching techniques, shoring, or shields (trench boxes).1 Sloping involves making sure that the soil is at an angle to prevent the soil from caving into the trench. In this particular incident, sloping was not a viable option due to the proximity of the trench to the adjacent concrete wall. When sloping methods are not feasible, trench shields or aluminum hydraulic shoring systems should be used. In addition to the use of correct protective systems, the spoil pile should also be at least two feet from the edge of the trench. When installing miles of pipeline or cable, the amount of soil that must be moved along with the associated cost of excavator fuel, operator time, backfill, compaction, etc., can make sloping inefficient and time consuming in regard to project deadlines. Rather than foregoing the use of a protective system altogether, it is strongly recommended that employers at least require trench shields or aluminum hydraulic shoring systems, both of which are OSHA-approved protective systems that can be rented, if needed. These protective systems can still adequately protect workers while increasing project expediency and efficiency.
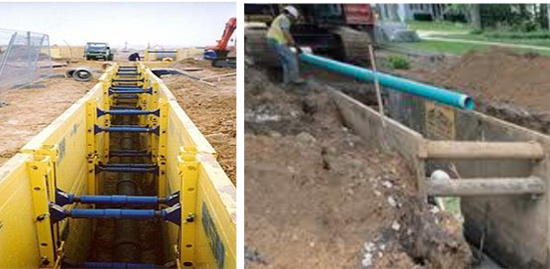
Figure 6. Stock photos of trench shoring (left), trench box (right).
Recommendation #3: Employers should ensure that concrete formwork is braced and tied down adequately to stay in alignment and retain stability.
A competent person is defined by OSHA 1926.650(b) as “a person capable of identifying existing and predictable hazards in the surroundings, or working conditions which are unsanitary, hazardous, or dangerous to employees, and who has authorization to take prompt corrective measures to eliminate the hazards”.2 Inspections should occur throughout the day and as conditions change. The competent person on the job site was the superintendent who did not perform a soil test or inspection of the work area prior to allowing work to begin. This was important because the stability of the soil was affected by seven straight days of rain prior to the fatal incident. An adequate soil test should have taken into account that the soil near the concrete wall’s foundation had been previously disturbed, increasing the likelihood of a trench collapse and increasing the need for a required trench protection system.3 The employer had a digital tool to identify soil classification, however, the tool was not used on the day of the incident.
Recommendation #4: Daily toolbox talks should be conducted which emphasize safety topics related to the upcoming job tasks prior to allowing work to begin on the job site.
Pre-work meetings were held before the start of the workday. During the meetings, general safety hazards were discussed; trench safety was not discussed.
Recommendation #5: Employers should intervene when unsafe acts on the jobsite are witnessed.
During the investigation and interview process it was discovered that the victim had climbed into and out of the unprotected trench several times that morning. Superintendents and other site management personnel should intervene when they witness unsafe job practices.
Recommendation #6: Safe means of ingress and egress should be provided in all excavations prior entry.
The fatality investigation found no ladder or other safe means of ingress or egress in the trench. OSHA regulations require safe egress and ingress in a trench measuring greater than 4 feet in depth.3 Acceptable means of ingress and egress include ladders, steps, and ramps.
Please take the time to complete our brief survey regarding this report: (https://uky.az1.qualtrics.com/SE/?SID=SV_ahG4NwOSoSnSWj3)
Electronic access to this full report can be found here: (http://www.mc.uky.edu/kiprc/face/reports/pdf/16KY017.pdf)
Keywords: Construction, Confined space, Trench, Cave-in, Excavation, Entrapment, Trench protective systems
REFERENCES
- Specific Excavation Requirements. 29 CFR 1926.651(c)(2). Occupational Safety and Health Administration. [https://www.osha.gov/laws-regs/regulations/standardnumber/1926/1926.651]
- 29 CFR 1926 OSHA Standards for the Construction Industry, Second Edition. Subpart P Excavations. 2009. Print.
- Soil Classification. 29 CFR 1926 Subpart P App A(c). Occupational Safety and Health Administration. [https://www.osha.gov/laws-regs/regulations/standardnumber/1926/1926SubpartPAppA]
ACKNOWLEDGEMENT
The Kentucky FACE program would like to thank KY OSH and the county coroner for their assistance with this report.
PHOTO CREDIT
The FACE Program would like to thank the Lexington Herald Leader for the title page photograph, Kentucky WLEX news for Figure 1A, Google Maps for Figure 1B and Kentucky OSHA for Figure 4. All other non-stock photos are credited to the Kentucky FACE program.
PROGRAM FUNDING
The Kentucky Fatality Assessment & Control Evaluation Program (FACE) is funded by grant 2U60OH008483-12 from the National Institute for Occupational Safety and Health (NIOSH).
DISCLAIMER
This case report was developed to draw the attention of employers and employees to a serious safety hazard and is based on preliminary data only. This publication does not represent final determinations regarding the nature of the incident, cause of the injury, or fault of employer, employee, or any party involved.
This case report was developed by the Kentucky Fatality Assessment and Control Evaluation (FACE) Program. Kentucky FACE is a NIOSH - funded o ccupational fatality surveillance program with the goal of preventing fatal work injuries by studying the worker, the work environment, and the role of management, engineering, and behavioral changes in preventing future injuries. The FACE Program is located in the Kentucky Injury Prevention and Research Center (KIPRC). KIPRC is a bona fide agent for the Kentucky Department for Public Health.
Email: kyfaceprogram@uky.edu | Telephone: 859-257-5839
333 Waller Avenue Suite 242, Lexington, KY 40504
FACE on Social Media:
https://www.facebook.com/Kyfaceprogram/